What is Foam sheets
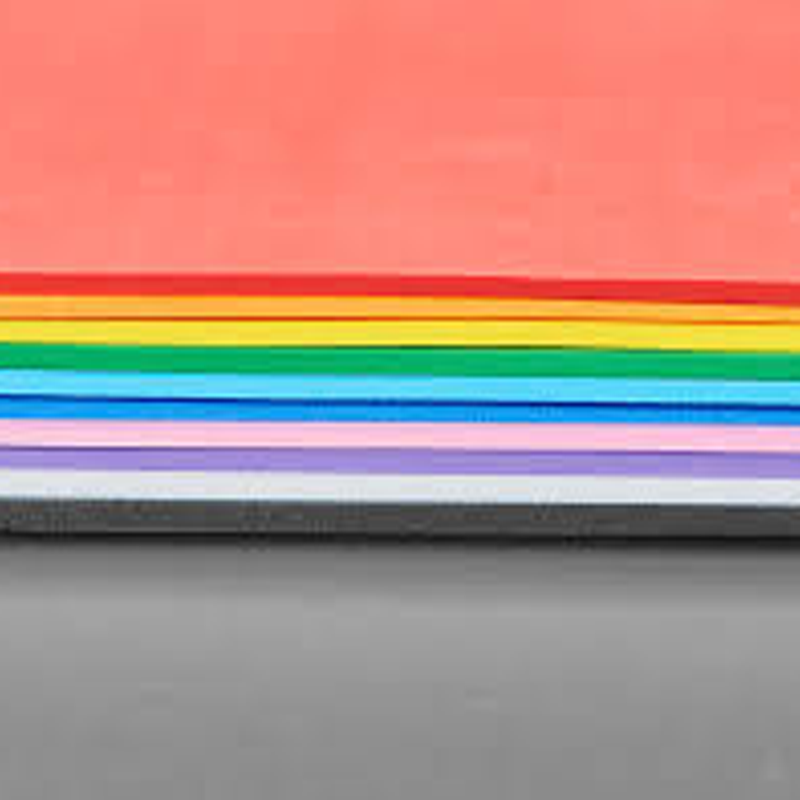
Foam sheets are material with multiple characteristics and has been widely used in many fields.
The characteristics of foam sheets are very significant.
First of all, after its various series of products are made with weather-resistant formula, the color can remain unchanged for a long time and is not easy to age.
It is light in texture and easy to store, transport and construct.
It can be constructed using general wood processing tools, and can also be welded according to general welding procedures, and can also be bonded with other PVC materials.
The surface is rough and can be printed. It can be drilled, sawed, nailed, planed, and glued like wood, and can be used for thermoforming, heating bending and folding.
Foam board has the properties of sound insulation, sound absorption, heat insulation, and heat preservation.
The board is flame retardant and can self-extinguish without fire. It is safe and reliable.
All series of products have moisture-proof, mildew-proof, non-absorbent properties, and good shockproof effect.
Foam board has a wide range of applications.
In the field of construction, it can be used for building wall and roof insulation, which can protect the main structure of the building.
Extend the life of the building, effectively eliminate “thermal bridges”, improve the wall moisture and temperature, help to maintain stable room temperature, and increase the usable area of the house.
In steel structures, the application of color steel tile sandwich composite panels accounts for 50%.
It accounts for 20% in floor heating and cold storage, and 20% in exterior wall insulation.
In addition, it is also used in decoration materials and retail fields, each accounting for 5%.
In the field of cold chain logistics, cold storage buildings and refrigerated trucks, foam sheets have excellent resistance to water vapor penetration and pressure resistance.
It makes the performance of cold storage and refrigerated trucks unchanged for a long time and prevents condensation.
In the geotechnical field, such as highway engineering, it can prevent the penetration of water vapor, frost, etc., effectively control the frost heave of the ground, and extend the service life of the highway.
In railway engineering, high-strength foam sheets can be used as effective load-bearing and elastic buffer layers under the track slabs to reduce vibration and noise.
In channel engineering, it can solve the problem of freezing damage to concrete water supply channels.
Preparation before molding
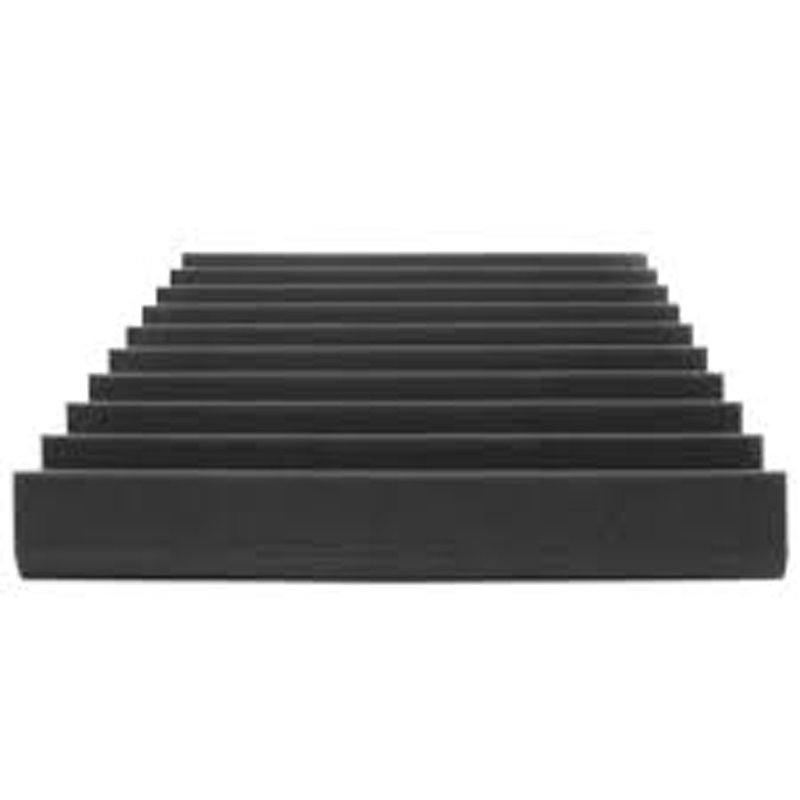
1.Material selection
There are many types of foam materials, and different types of foam materials have different characteristics.
For example, soft foam plastics use resin as the main raw material, are soft in texture, and have the advantages of excellent elasticity, sound absorption, and heat preservation.
Soft foam plastics are widely used in packaging materials and car and ship hulls.
At room temperature, the polymers that make up hard foam plastics are crystalline or amorphous, with a hard texture, good compressive resistance and heat insulation, and are often used in building insulation and other fields.
Semi-rigid (or semi-soft) foam plastics are between soft and hard.
When choosing foam materials, you need to consider specific needs.
If you need good cushioning performance, you can choose soft foam plastics.
If you have high requirements for heat insulation and pressure resistance, hard foam plastics are more suitable.
For occasions that require both a certain hardness and a certain elasticity, semi-rigid foam plastics are a better choice.
In addition, factors such as the environmental protection and cost of the material need to be considered.
2.Tool preparation
A series of tools are required to mold foam sheets. Among them, molds are one of the key tools.
Different types of molds can be selected according to different production needs.
For example, a tool for producing foam insulation boards usually has two half molds, each of which has a mold frame and a mold base.
The mold frame defines the end faces of the insulation board to be produced, and the mold base defines the side faces of the insulation board to be produced.
The two half molds together limit the mold cavity, which roughly corresponds to the insulation board to be produced.
In addition, equipment such as a press is required.
By means of the press, the two half molds can be pressed together to ensure the quality and accuracy of the foam board forming.
At the same time, some auxiliary tools may also be required, such as filler connectors for supplying foam particles.
Positioning pins, which can be extended into the mold cavity and retracted from the mold cavity by means of linear actuators to ensure the dimensional accuracy of the foam board.
These equipment provide a strong guarantee for the efficient forming of foam sheets.
Detailed explanation of forming methods
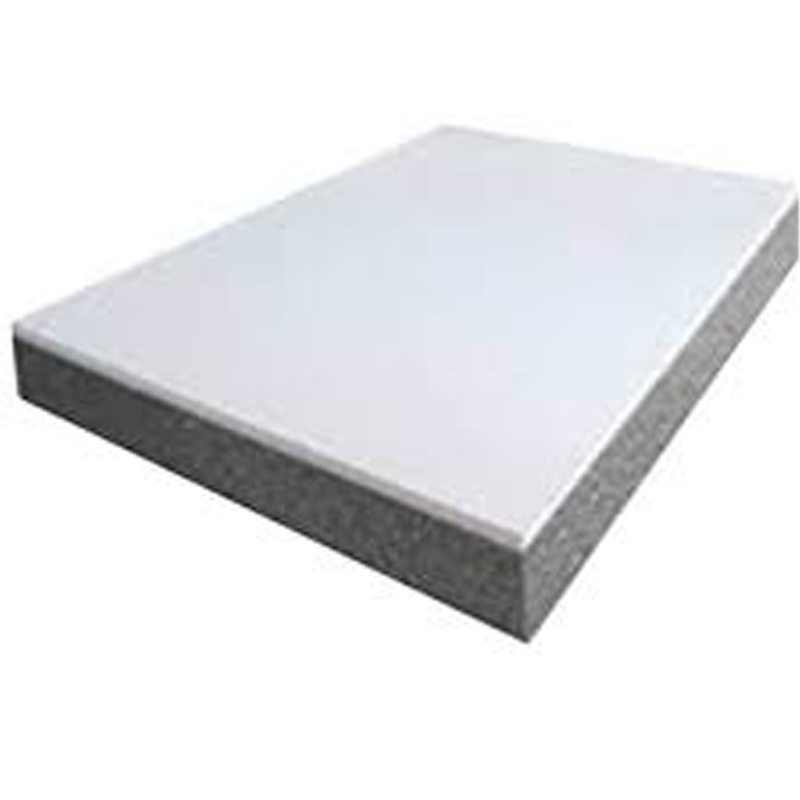
Thermoforming method
Thermoforming principle is to use thermoplastic plastic sheet as raw material, first cut the sheet into blanks of a certain size and shape.
Then clamp the blank on the frame, heat it to the softening temperature, that is, the high elastic-plastic state, and then apply pressure to bend and extend the blank.
After reaching a certain shape, it is cooled and formed into an open thin shell product.
In most cases, the pressure applied to the blank during the thermoforming process is the pressure difference formed on both sides of the blank by vacuuming and compressed air, but various forms of mechanical pressure or hydraulic pressure can also be used.
In specific operations, temperature control is crucial.
Generally speaking, the temperature of thermoforming needs to be adjusted according to different foam materials.
For example, for some common thermoplastic foam materials, the heating temperature is usually above its softening point, but not too high to avoid decomposition or burning of the material.
The specific temperature range may be between 150℃ – 250℃.
During the heating process, professional heating equipment, such as an oven or a heating plate, is required to ensure that the blank is heated evenly.
When the blank reaches the softening temperature, pressure is quickly applied for forming.
The size of the pressure also needs to be adjusted according to the requirements of the material and the product, generally between 0.5MPa – 2MPa.
After molding, it is necessary to cool and shape. The cooling speed should not be too fast to avoid internal stress and affect the quality of the product.
Compression molding method
Compression molding method is mainly used to mold thermosetting plastic foam sheets.
The process is as follows: first, add the powdered, granular, crumb-like or fibrous thermosetting plastic raw materials directly into the open mold feeding chamber; then close the mold and heat to melt the plastic.
Under the action of the mold closing pressure, the molten plastic fills the cavity.
At this time, the plastic in the cavity produces a chemical cross-linking reaction, so that the molten plastic gradually transforms into an infusible hardened and fixed plastic part.
Finally demolds the plastic part to remove it from the mold.
The advantage of compression molding is that it can be produced using an ordinary press and the mold structure is relatively simple.
At the same time, there are fewer oriented structures in the plastic part, the performance is relatively uniform, and the molding shrinkage is small.
The following points should be noted during operation:
First, the thermosetting plastic should be preheated and dried before molding to ensure the molding quality of the plastic part.
The preheating temperature is generally between 80℃ and 120℃, and the drying time depends on the humidity of the material, generally 2-4 hours.
Secondly, the feeding should be accurate.
Common feeding methods include volume mass method, capacity method and counting method.
The volume mass method can accurately control the feeding amount, but the operation is inconvenient
The capacity method is easy to operate, but the feeding amount control is not accurate enough; the counting method is suitable for pre-pressed blanks.
When closing the mold, before the punch contacts the material, the mold closing speed should be accelerated as much as possible.
After the punch contacts the material, the mold closing speed should be slowed down to avoid displacement and damage of the inserts and molding rods in the mold.
Exhaust is also critical. When compressing thermosetting plastics, the molding material will release a considerable amount of water vapor, low molecular volatiles.
And gases generated during cross-linking reactions and volume shrinkage in the mold cavity.
It is necessary to relieve the pressure to discharge the gas in the mold cavity, otherwise it will affect the quality of the plastic parts.
The number and time of exhaust are generally 1-3 times, and each time is 3-20s.
The curing time should be moderate, with a moderate degree of hardening as the standard.
For plastics with a low curing rate, it is not necessary to complete the entire curing process in the mold.
Other molding methods
Injection molding is also a common foam sheet molding method.
The process of foam plastic injection molding is basically the same as the general injection molding process.
The heating, mixing, plasticization and most of the foaming and expansion of the plastic are completed in the injection molding machine.
Injection molding can be divided into physical foaming and chemical foaming.
The physical foaming method uses physical methods to foam plastics, such as first dissolving an inert gas in a plastic melt or paste under pressure.
And then releasing the gas after decompression, thereby forming pores in the plastic to foam.
Or by evaporating a low-boiling point liquid dissolved in a polymer melt to vaporize it and foam it.
The chemical foaming method uses chemical methods to generate gas to foam plastics,
heating the chemical foaming agent added to the plastic to decompose it to release gas to foam,or using the gas released by chemical reactions between the plastic components to foam.
The characteristic of injection molding is that it can produce foam sheets with complex shapes, but it requires special injection molding machines and auxiliary equipment, and the technical difficulty is relatively high.
In addition, there is also structural foaming molding, which belongs to the chemical foaming method.
It retains many advantages of the traditional injection molding process and avoids some problems encountered in the traditional injection molding process, such as insufficient product strength, too long production cycle, and low molding rate.
Structural foam products are a kind of one-piece foam material with a dense surface layer.
Its unit weight strength and rigidity are 3-4 times higher than that of the same unfoamed material.
The biggest feature of the structural foaming method is that it can be produced by injection molding with an ordinary injection molding machine without adding equipment.
However, compared with ordinary injection molding machines, the high-pressure structural foaming injection molding machine that uses the mold cavity expansion method for foaming has a secondary mold clamping and pressure holding device.
Post-molding processing
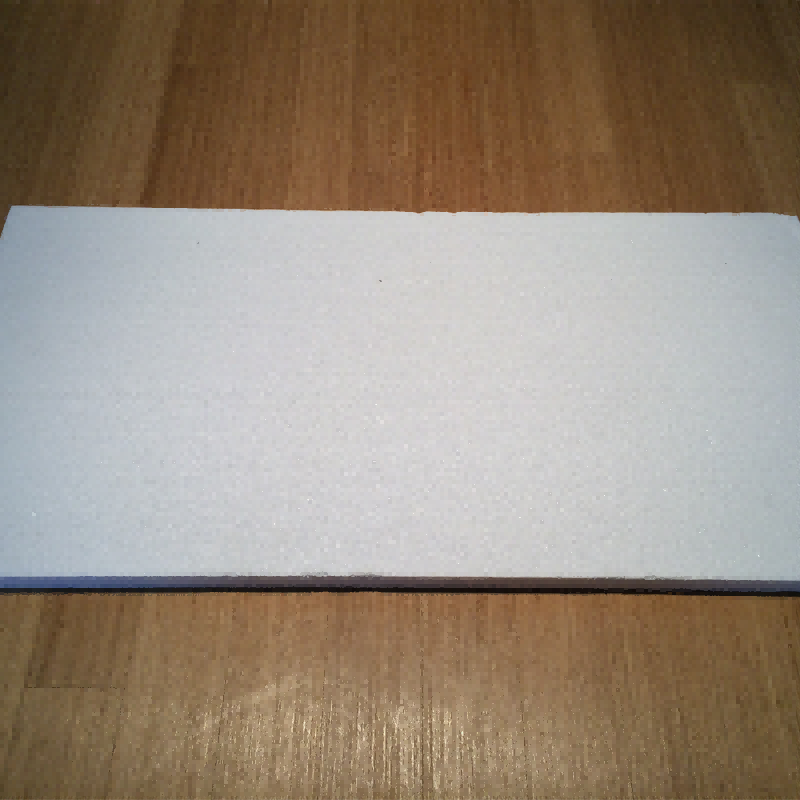
Finishing processing
Cutting: According to actual needs, the foam board may need to be cut after molding.
A special foam board cutting device can be used, such as a pneumatic foam board cutting device, which includes a foam board and a cylinder seat set at both ends.
The cylinder seats at both ends are respectively installed with cylinders, and the piston rods of the two cylinders are respectively fixedly connected with connecting rods.
A wire rope is connected between the two connecting rods.
A conveyor belt is provided under the wire rope. The foam board is placed on the conveyor belt.
The cylinder piston rod pushes the wire rope downward to press over the foam board.
It is simple to use, automatic cutting saves time and effort, and has high work efficiency.
Plane finishing: There are many methods for plane finishing of foam boards.
For example, a foam board plane trimming device is used in conjunction with a welding platform, including a T-shaped transverse telescopic part and a longitudinal fixed part.
One end of the transverse telescopic part is connected to the longitudinal fixed part by a sliding assembly, so that the transverse telescopic part can slide along the length direction of the longitudinal fixed part.
A vertical limit assembly is installed on the longitudinal fixed part, and the longitudinal fixed part is fixed on the welding platform through a vertical limit assembly;
A trimming tool is installed above the other end of the transverse telescopic part, and the trimming tool is vertically passed through the transverse telescopic part through a fixing device.
The trimming tool includes a hand drill and a hole opener installed with the drill bit of the hand drill.
The fixing device can adjust the milling depth to ensure that the grooves on the foam board are flat and improve the processing efficiency.
Grinding treatment
Selection of grinding device: In order to obtain better appearance and performance, the foam board needs to be polished after forming.
A foam board grinding and polishing device can be used, including a support frame,
a first threaded barrel is arranged on the surface of the support frame,
a first threaded rod is arranged inside the first threaded barrel,
a rotating device is arranged at one end of the first threaded rod,
a fixed plate is connected to one end of the first threaded rod,
a first motor is arranged on the surface of the support frame,
a second threaded rod is installed at the output end of the first motor,
a second threaded barrel is arranged on the surface of the second threaded rod,
a sliding device is arranged on the surface of the support frame,
a telescopic device is connected to one end of the sliding device,
a connecting frame is connected to one end of the telescopic device,
a second motor is arranged on the surface of the connecting frame,
a grinding wheel is installed at the output end of the second motor,
a vacuum cleaner is arranged at the bottom of the support frame,
a dust collecting box is arranged at the bottom of the support frame, and a dust collecting pipe is arranged on the surface of the dust collecting box.
The foam board to be polished is placed on the surface of the support frame, the fixed plate is moved by the rotating device and the first threaded rod, and the board is fixed and clamped to prevent the board from moving during polishing.
EPS foam sheet grinding: For the surface grinding of EPS foam sheet, an EPS foam sheet surface grinding device can be used, including a top plate and a bottom plate,
a conveying channel extending horizontally from left to right is formed between the top plate and the bottom plate,
a first process hole close to the input end of the conveying channel and a second process hole close to the output end of the conveying channel are opened on the bottom plate,
a first transmission roller with an axis extending horizontally forward and backward is arranged in the first process hole,
a second transmission roller with an axis extending horizontally forward and backward is arranged in the second process hole,
and a third process hole arranged between the first process hole and the second process hole is arranged in the bottom plate,
and a grinding roller with an axis extending horizontally forward and backward is arranged in the third process hole.
The EPS foam sheet to be end-faced is fed in along the input end of the conveying channel,
the first transmission roller and the second transmission roller rotating at a low speed are used to transmit the EPS foam sheet,
and the grinding roller rotating at a high speed is used to grind the EPS foam sheet, so as to remove the uneven surface features,
crush it into powder, and finally send it out from the output end of the conveying channel.
Surface treatment to improve performance
Whitening treatment: For recycled polystyrene foam boards, there are problems such as insufficient whiteness and yellowish color. Recycling additives can be added to improve this shortcoming, such as common titanium dioxide and fluorescent brighteners.
A certain amount of fluorescent brightener is directly added to the molded plastic base material for sufficient mixing. When the extruder reaches the plastic melting temperature, the mixture is squeezed into the screw extruder for melting, so that the fluorescent brightener is evenly dispersed in the melt, and finally granulated.
This dry whitening is mainly suitable for thermoplastic resins and the application method is relatively common.
Fluorescent brighteners can make the foam boards produced by recycled plastics de-yellowing and whitening, almost reaching or even exceeding the whiteness of new materials.
When the base color of the polystyrene board is not white, first use titanium dioxide for whitening, and then add fluorescent brighteners to further improve the whiteness of the polystyrene board.
Waterproof treatment: For polystyrene foam insulation boards, a highly waterproof polystyrene foam insulation board reprocessing process can be used.
The raw materials are uniformly mixed and extruded by a twin-screw extruder to obtain a foam board semi-finished product.
During the cooling process, when the temperature drops to 100-130°C, the temperature is maintained and magnetic oil balls are sprayed on one surface of the foam sheet semi-finished product;
a magnetic field is applied to the foam sheet semi-finished product to guide the magnetic oil balls to be evenly distributed on the foam sheet semi-finished product, thereby forming a magnetic oil homogenization layer on the surface of the foam sheet semi-finished product;
cooling is continued to make a plurality of magnetic oil balls evenly fixed on the surface of the foam board semi-finished product;
a pre-treated oil-absorbing liquid-spill sticky sheet is laid on the surface of the magnetic oil homogenization layer of one foam board semi-finished product,
and then the magnetic oil homogenization layer of another foam sheet semi-finished product is covered on the oil-absorbing liquid-spill sticky sheet,
and after extrusion and shaping, cooling and lamination are continued to form a pre-water-avoiding layer between the two foam board semi-finished products to obtain a re-treated foam insulation board finished product.
When the foam insulation board cracks and leaks, the pre-demagnetized balls dissolve in water, causing the waterproof oil inside to leak out and spread on the oil-absorbing and overflowing sticky sheet.
Since water and oil are immiscible, the oil-absorbing and overflowing sticky sheet in the center of the pre-water-avoiding layer is waterproof, effectively reducing the impact of cracking and water seepage on its thermal insulation.
Through the above finishing, grinding and surface treatment methods, the formed foam sheet can obtain better appearance and performance to meet the use needs of different fields.
Conclusion
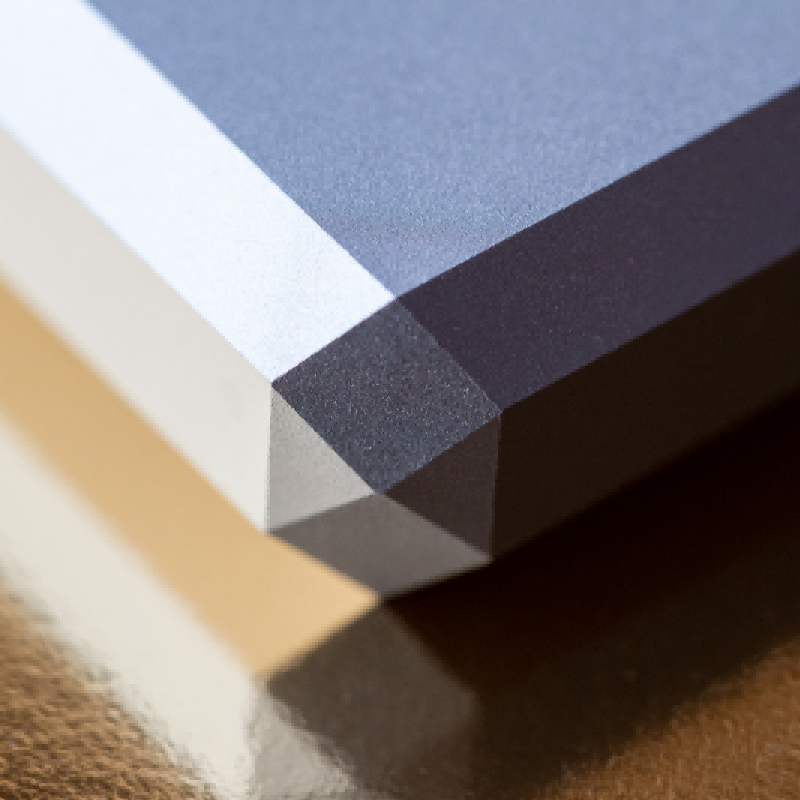
Each foam board forming method has its own advantages and disadvantages. In actual production, it is necessary to select a suitable forming method based on product requirements, production scale, cost and other factors.