What is Foam Corner
Foam corners are widely used in decoration, and their importance cannot be ignored.
Foam corners can not only add beauty to the room, but also cover up the defects at the junction of the wall and the ceiling.
In the decoration process, the cutting of foam corners is a key link, which directly affects the final decoration effect.
The cutting of foam corners requires precise measurement and operation.
First, determine the length and angle of the foam corners according to the size and design requirements of the room.
Then, use professional tools such as knives or saws to cut. During the cutting process, pay attention to keeping the tool stable and vertical to ensure the flatness and smoothness of the cut surface.
The cutting accuracy of foam corners is crucial to the quality of installation.
If the cutting is inaccurate, there may be a gap between the corners and the wall or ceiling, affecting the beauty and sealing.
In addition, inaccurate cutting may also cause the corners to be spliced unsmoothly, affecting the overall effect.
In actual decoration, the cutting of foam corners can be adjusted according to different needs and design styles.
For example, different angles and lengths can be selected to create a unique decorative effect.
At the same time, customized cutting can be performed according to the shape and size of the room to ensure that the corner line fits the room perfectly.
In short, the cutting of the foam corner line is an important part of decoration and needs to be taken seriously.
Through precise measurement and operation, the installation quality and aesthetics of the foam corner line can be ensured, adding a unique charm to the room.
Cutting foam corner molding safety precautions
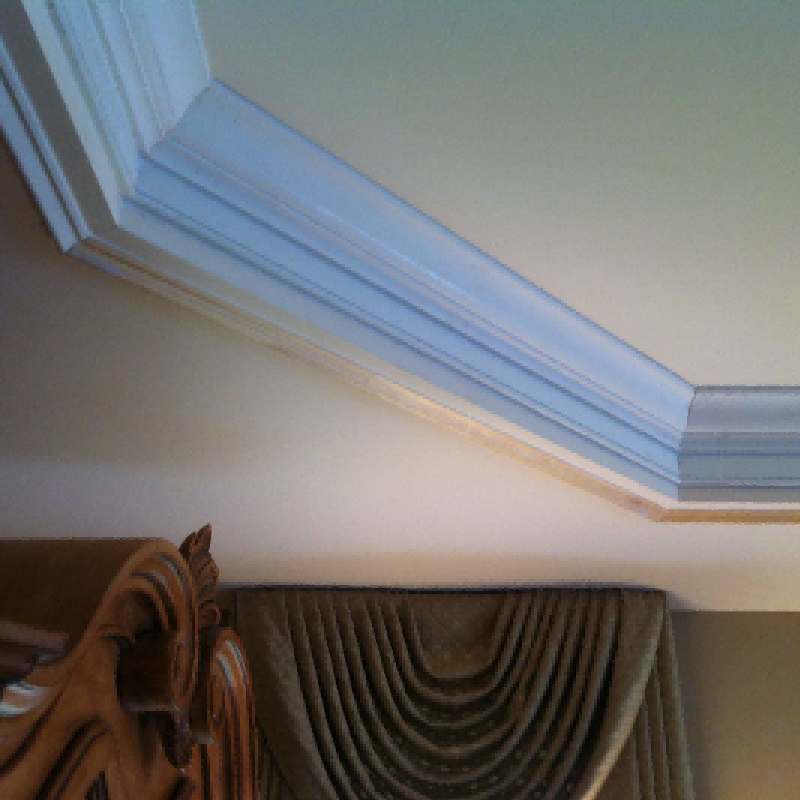
Understand safety precautions
When cutting foam top corners, safety is of vital importance.
First, wear appropriate protective equipment, such as gloves to prevent your hands from being scratched by cutting tools, and goggles to protect your eyes from flying debris.
At the same time, ensure that the work area is well ventilated, because foam may produce some odor and dust during the cutting process, and good ventilation can reduce the adverse effects on the human body.
In addition, when using electric cutting tools, check whether the power cord of the tool is intact to avoid electric shock accidents.
For some methods that require heating and cutting, such as cutting with electric heating wire, pay special attention to controlling the temperature to prevent overheating and fire.
According to data, the foam cutting temperature is below 200 degrees, and it does not need to be burned to red heat at all, which will anneal the electric heating wire and soften it.
Follow safety regulations
Cutting in strict accordance with safety operating specifications is the key to ensuring construction safety.
When using manual tools such as knives or saws, keep your hands stable and apply force evenly to avoid accidental injuries caused by the deviation of the tool.
If you use power tools, such as CNC foam cutting machines, you should first be familiar with the operating instructions and safety precautions of the equipment.
For example, when the power is on or the machine is running, do not touch any electrical components in the electrical cabinet and operating table to avoid electric shock.
At the same time, do not operate any switch knobs with wet hands, and do not check the wires or replace electrical components with power on.
For equipment such as CNC foam cutting machines, only maintenance personnel with corresponding technical qualifications and in strict accordance with the technical requirements of electrical maintenance can repair the equipment to prevent accidents.
During the cutting process, always pay attention to the surrounding environment to ensure that there are no people or other objects in front to avoid hitting others or damaging items.
After each cutting, the cutting tool should be placed in a safe place to avoid accidental touch and injury.
For some large cutting equipment, during maintenance, ensure that the machine is in a stopped working state and hang a warning sign to avoid man-made accidents caused by sudden operation of the machine.
Cutting foam corner molding skills
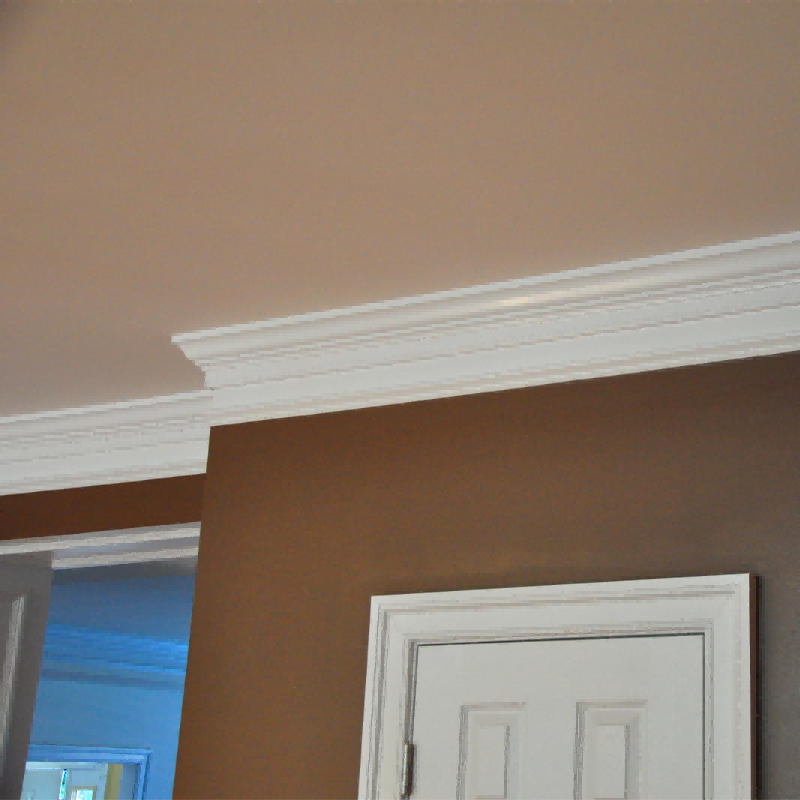
Choose the right tool
To achieve smooth cutting of foam top corners, it is crucial to choose the right tool.
Among them, the electric jigsaw is a good choice.
It can cut in a more precise way, and the cutting speed and angle can be adjusted according to different cutting requirements.
According to the searched information, the electric jigsaw can provide a more stable cutting effect when cutting materials such as foam, making the cutting surface smoother.
In addition, sharp hand knives can also be used in some specific situations.
For example, when performing fine cutting in a small range, hand knives can better control the cutting accuracy.
But it should be noted that when using hand knives, the sharpness of the knives must be maintained to ensure the smoothness of the cutting.
Master the cutting method
When cutting foam top corners, mastering specific techniques can achieve a smoother cutting effect.
First of all, before cutting, the top corners should be accurately measured and marked to ensure that the cutting length and angle meet the design requirements.
For the use of electric tools, cut at a stable speed and uniform force.
Avoid operating too fast or too hard to avoid uneven cutting surfaces.
For example, when using an electric jigsaw, you can first test cut at a slower speed, and then gradually increase the speed after finding the right cutting feeling.
If you use a manual tool for cutting, you should use a sawing method.
Gently pull the tool along the marked line, and the distance of each pull should not be too large to ensure the accuracy and smoothness of the cutting.
At the same time, during the cutting process, you can touch the cutting surface with your hand from time to time to feel the flatness of the cutting so as to adjust the cutting method in time.
In addition, in order to further improve the smoothness of the cutting, the cutting surface can be lightly polished after cutting.
Use fine sandpaper to gently polish the cutting surface to remove some tiny burrs and unevenness, so that the top angle line is smoother and more beautiful.
But pay attention to the strength when polishing to avoid excessive polishing and damage to the top angle line.
Cutting foam corner molding method
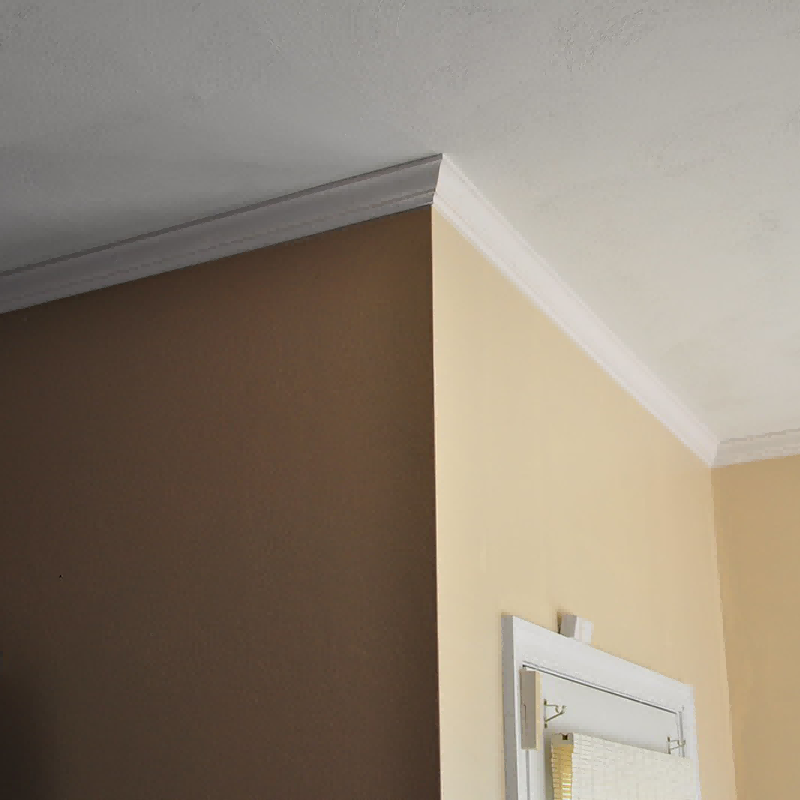
Accurate use of tools
To achieve accurate cutting of foam top corners, accurate use of tools is the key.
For power tools, such as electric jigsaws, the angle and height of the saw blade should be carefully adjusted before use to ensure that they match the required cutting angle and depth.
For example, if you want to cut a 45-degree top corner, you need to adjust the saw blade to a precise 45-degree angle to ensure the accuracy of the cutting.
At the same time, pay attention to the cutting speed of the electric jigsaw.
Too fast a speed may lead to inaccurate cutting, while too slow a speed will affect work efficiency.
According to actual operating experience, a moderate cutting speed can improve work efficiency while ensuring accuracy.
For manual knives, ensure the sharpness and straightness of the knives. Sharp knives can cut into foam materials more easily and reduce cutting errors.
When using manual knives, keep the knife perpendicular to the top corner, apply force evenly, and avoid the knife from deviating from the cutting line.
A ruler or square ruler can be used to assist in cutting to ensure that the knife cuts along a straight line.
Strategies to improve cutting accuracy
First, accurate measurement before cutting is an important step to improve cutting accuracy.
Use tools such as a tape measure or laser measuring instrument to accurately measure the length and angle of the required cut, and mark the top corner line.
The marking should be clear and accurate so that you can accurately cut along the marked line when cutting.
Secondly, use multiple measurements and verification methods. When performing important cutting tasks, do not rely solely on the results of a single measurement.
You can make multiple measurements and verify the measurement results to ensure the accuracy of the measurement.
For example, you can use different measuring tools to measure and then compare the measurement results to determine the most accurate value.
In addition, stay focused and patient during the cutting process.
Don’t rush for success, carefully observe the progress of the cutting, and adjust the angle and strength of the cutting tool in time.
If you find that the cutting is deviated, stop cutting immediately, recheck whether the measurement and marking are correct, and adjust the cutting tool to correct it.
Finally, you can use some auxiliary tools to improve the accuracy of the cutting.
For example, use a clamp to fix the top corner line to avoid inaccurate cutting caused by the movement of the top corner line during the cutting process.
You can also use a template or mold to cut the top corner line according to the shape of the template or mold, which can ensure the accuracy and consistency of the cutting.
Cutting foam corner molding tools
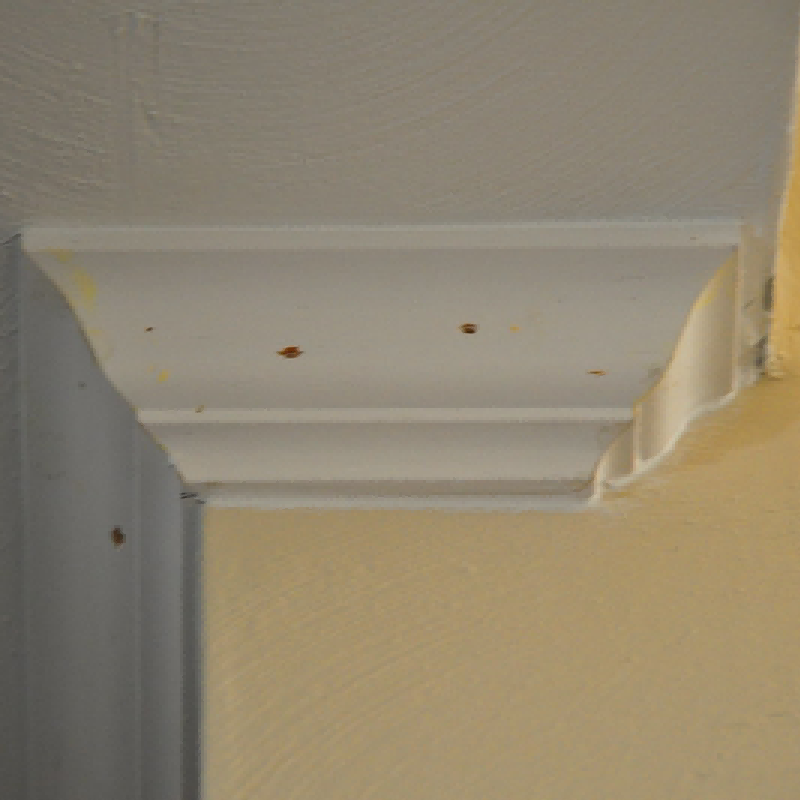
Introduction to various tools
Electric jig saw: Electric jig saw is a common cutting tool suitable for cutting foam top corners.
It has adjustable cutting speed and angle, which can be adjusted according to different needs.
The saw blade of electric jig saw is usually thinner, which can make fine cutting and make the cutting surface smoother.
In addition, electric jig saw can also be equipped with different saw blades to adapt to different materials and cutting requirements.
Handmade knives: Handmade knives include art knives, wallpaper knives, etc., which are simple and easy to use cutting tools.
The advantages of handmade knives are cheap price, easy operation, and can make fine cutting in a small range.
However, the cutting efficiency of handmade knives is low, and it requires certain skills and experience to master.
CNC foam cutting machine: CNC foam cutting machine is a high-precision cutting tool suitable for large-scale foam top corner cutting.
CNC foam cutting machine can realize automatic cutting through computer programming, and has the advantages of high cutting accuracy, fast efficiency, and good repeatability.
However, the price of CNC foam cutting machine is relatively high, and professional operators are required to operate it.
Comparison of tool advantages
Electric jig saw:
Advantages: fast cutting speed, adjustable angle, smooth cutting surface, and can be equipped with different saw blades.
Applicable scenarios: suitable for medium and large-scale foam top corner line cutting, especially for situations where a certain angle cutting is required.
Hand-made knives:
Advantages: cheap, easy to operate, suitable for small-scale fine cutting.
Applicable scenarios: suitable for small-scale foam top corner line cutting, or cutting in some places where it is difficult to use electric tools.
CNC foam cutting machine:
Advantages: high cutting accuracy, fast efficiency, good repeatability, and automatic cutting.
Applicable scenarios: suitable for large-scale foam top corner line cutting, and very suitable for situations with high cutting accuracy requirements.
In summary, different cutting tools have their own advantages, and readers can choose the best tool according to their needs and actual conditions.
If it is a small-scale cutting task, you can choose a manual knife;
if it is a medium-to-large-scale cutting task, you can choose an electric jig saw;
if the cutting accuracy requirements are high, you can choose a CNC foam cutting machine.