Mold EPS (Expanded Polystyrene) is a process where EPS beads are expanded and fused inside a mold to create a specific shape or form. This process utilizes the unique properties of EPS to produce items with excellent insulating properties, durability, and strength while remaining lightweight.
Understanding EPS(Expanded Polystyrene)
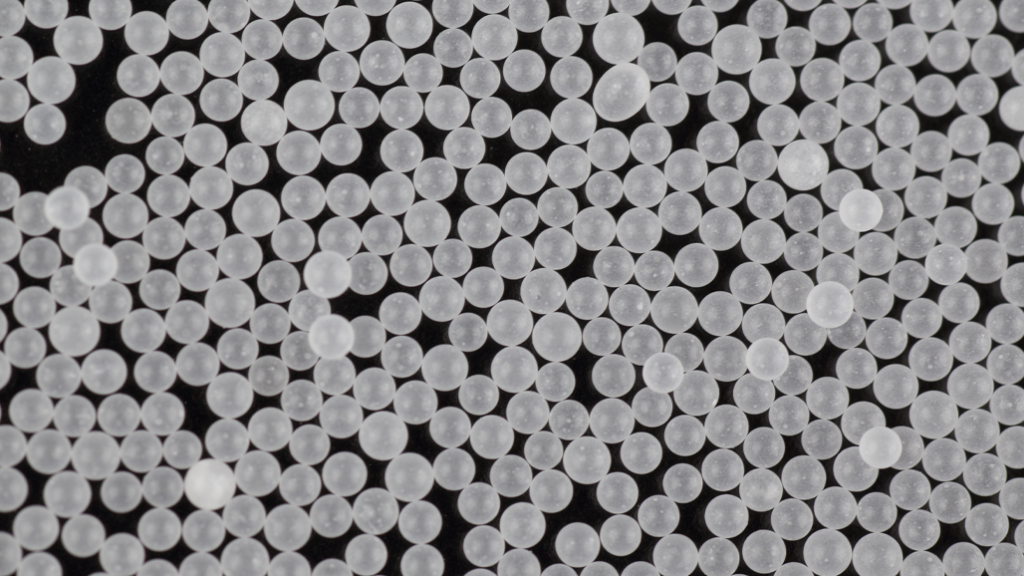
Before diving into the molding process, it’s essential to grasp what EPS is and why it’s so widely used.
EPS is a lightweight, rigid foam made from polystyrene beads that expand when exposed to steam.
Approximately 98% air, EPS offers excellent insulating and protective properties, making it a popular choice across various sectors.
Common Applications of EPS
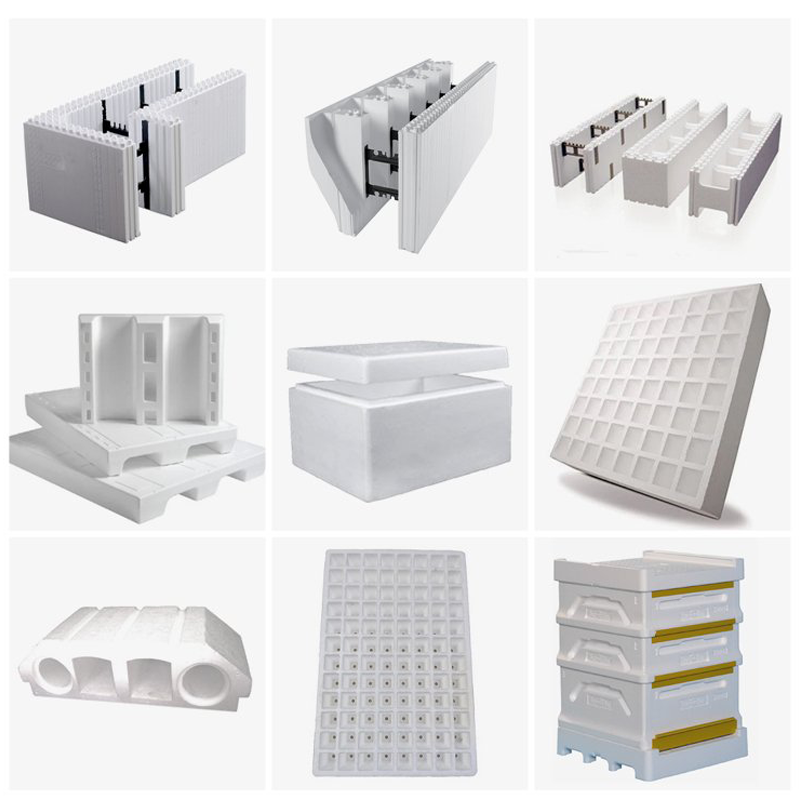
1.Packaging: EPS is frequently used for packaging due to its cushioning properties, making it ideal for protecting fragile items during shipping.
2.Construction: In the building industry, EPS is used for insulation and as a lightweight fill material.
3.Consumer Goods: Items like disposable coffee cups, coolers, and protective packaging for electronics often use EPS.
4.Industrial: EPS is used in various industrial applications, including as a core material in sandwich panels.
The EPS Molding Process
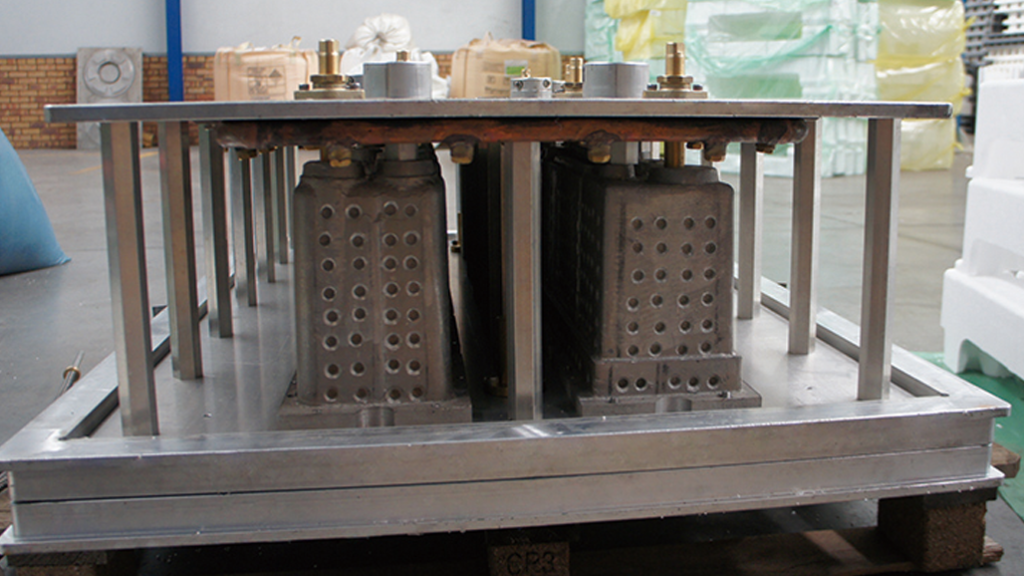
The time required to mold expanded polystyrene (EPS) depends on several factors。
Including the size and complexity of the mold, the density of the EPS beads, the type of molding equipment used, and the specific requirements of the final product.
Here is a general breakdown of the EPS molding process and typical timeframes:
Step 1: Pre-expansion
The first stage involves heating raw polystyrene beads in a pre-expander using steam.
This causes the beads to expand significantly. The expanded beads are then stabilized by cooling, allowing the air inside to settle and the beads to harden slightly.
Time Required: Pre-expansion typically takes about 1-2 hours, including stabilization time.
Step 2: Aging
After pre-expansion, the beads undergo an aging process where they are stored in ventilated containers or silos. This step ensures the beads achieve the desired density and are ready for molding.
Time Required: Aging can take from 12 to 48 hours, depending on the desired properties and environmental conditions.
Step 3: Molding
Aged beads are transported to molding machines where they are subjected to heat and pressure.
The beads are injected into molds and steam is applied again, causing them to expand further and fuse together.
Time Required: The actual molding cycle typically ranges from 3 to 10 minutes per cycle, depending on the mold’s size and complexity.
Step 4: Cooling
Once molded, the EPS products need to cool to retain their shape and achieve the desired mechanical properties. Cooling is often facilitated by air or water.
Time Required: Cooling usually takes 10 to 30 minutes, though larger or more complex shapes may require longer.
Step 5: Ejection and Post-Processing
After cooling, the molded EPS products are ejected from the mold. Additional steps such as trimming, shaping, or applying surface treatments may be necessary.
Time Required: Ejection and post-processing typically take an additional 5 to 15 minutes.
While the active molding time for EPS can be relatively short (5-20 minutes), the entire process from pre-expansion to final product can span from several hours to a few days depending on actual conditions.
Factors Influencing the Molding Time
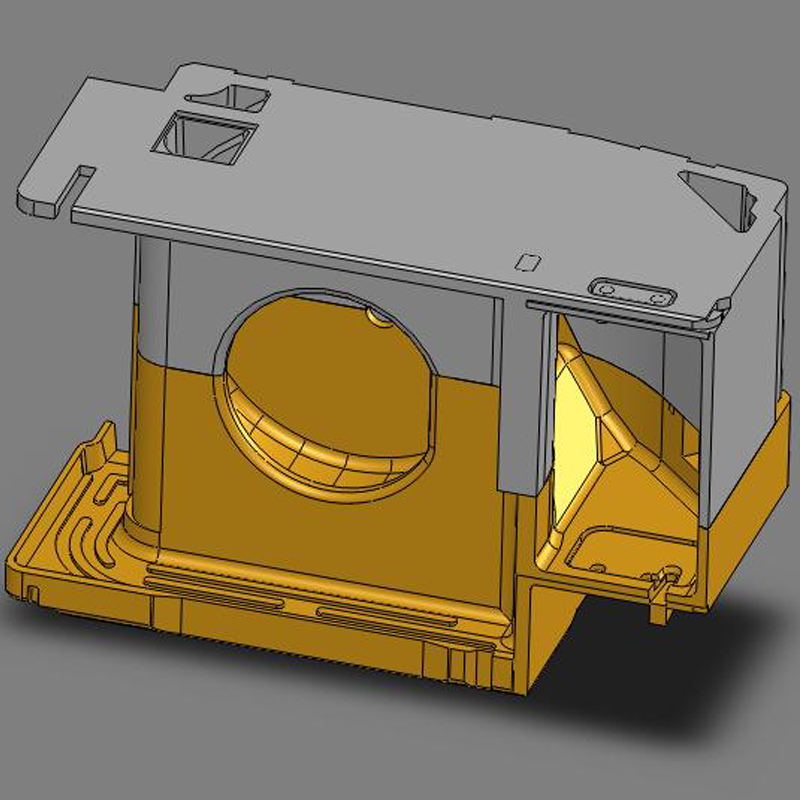
Several factors can influence the time required to mold EPS. Understanding these variables helps manufacturers optimize their processes.
Mold Complexity
Complex molds with intricate details generally require more time to fill and fuse compared to simpler designs.
Bead Size and Density
The size and density of the polystyrene beads affect expansion and cooling times. Smaller or denser beads may require more time to achieve the desired results.
Machine Efficiency
Modern, high-efficiency molding machines with advanced controls can significantly reduce cycle times. Automation and real-time monitoring further enhance efficiency.
Environmental Conditions
Ambient temperature and humidity can impact the aging and cooling stages. Warmer conditions might reduce cooling time but could affect bead stability during aging.
Steam Quality and Pressure
Consistent steam quality and pressure are crucial for uniform expansion and fusion. Variations can lead to inconsistencies and longer cycle times.
Best Practices for Efficient EPS Molding
To optimize the EPS molding process, manufacturers can adopt several best practices. These not only reduce production time but also improve product quality.
Regular Maintenance of Equipment
Regular maintenance of pre-expanders, molding machines, and cooling systems ensures they operate at peak efficiency, preventing downtime and reducing cycle times.
Optimal Storage Conditions
Maintaining optimal storage conditions for aged beads ensures they remain stable and ready for molding. Controlled environments with consistent temperature and humidity are ideal.
Quality Control Measures
Implementing strict quality control measures at each stage helps identify and address issues promptly, reducing rework and production delays.
Training and Skill Development
Investing in workforce training ensures operators are proficient in handling the machinery and processes, leading to more efficient production cycles.
Use of Advanced Technology
Leveraging advanced technologies such as automation, real-time monitoring, and data analytics can significantly enhance the efficiency of the EPS molding process.
Automated systems reduce manual intervention and optimize each stage of production.
The Future of EPS Molding
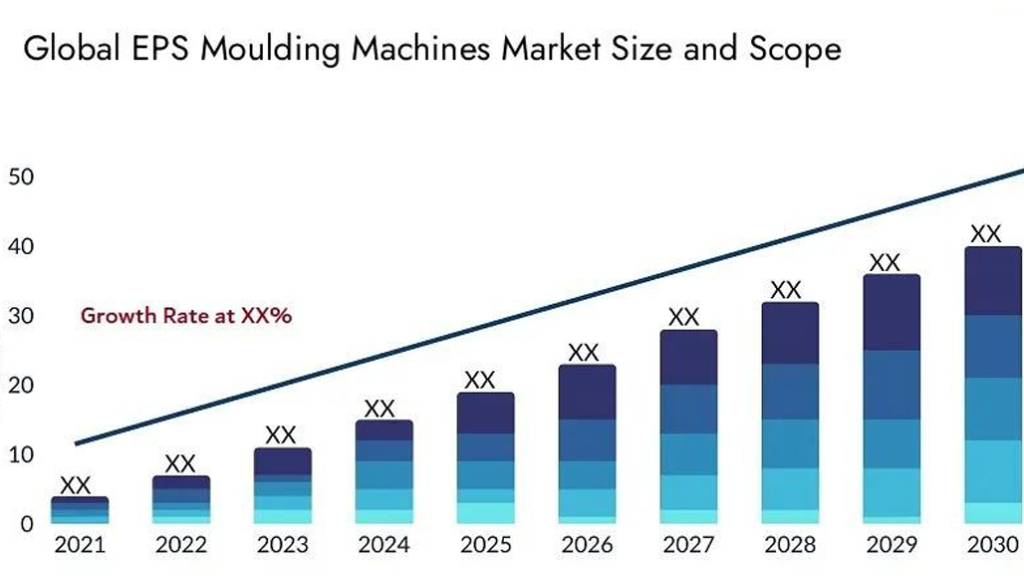
As technology advances, the EPS molding process continues to evolve. Innovations in machinery, materials, and techniques promise to further reduce production times and enhance product quality.
Automation and Robotics
The integration of automation and robotics in the molding process can streamline operations, reduce manual labor, and increase precision.
Automated systems can handle multiple tasks simultaneously, significantly cutting down production time.
Advanced Materials
Research and development in polymer science are leading to the creation of advanced EPS formulations with improved properties. These new materials can enhance performance and reduce processing times.
Sustainable Practices
As sustainability becomes a priority, the EPS industry is exploring eco-friendly practices.
Recycling programs, energy-efficient machinery, and sustainable sourcing of raw materials are becoming more common, contributing to a greener future.
Future Innovations in EPS Molding
Continuous developments in technology and methods in the EPS molding industry promise greater efficiency and performance
Advances in automation can streamline the entire production line, increase production speeds, reduce labor costs, and achieve greater precision.
Developments in mold design, including the use of computer-aided design (CAD) and 3D printing, allow for the creation of more complex and precise molds.
These innovations can reduce molding time and improve the quality of the final product.
EPS recycling and the use of bio-based materials are important as environmental issues become more pressing.
Implementing a closed-loop system is important. Recycling waste EPS into the production process can significantly reduce waste.
Balancing cost management with technological advancement is also important.
The initial investment in advanced machinery and smart technology can be high, but it is necessary to achieve long-term efficiency and productivity gains.
Conclusion
Understanding the time required to mold EPS is crucial for manufacturers across various industries.
The process involves several stages, each contributing to the overall production time.
By considering factors such as mold complexity, bead size, machine efficiency, environmental conditions, and steam quality, manufacturers can optimize their processes.
Adopting best practices like regular equipment maintenance, optimal storage conditions, strict quality control, workforce training, and advanced technologies can further enhance efficiency and reduce production time.
Real-world examples demonstrate the potential for significant improvements in productivity through these measures.
As technology continue to evolve, the future of EPS molding promises even greater efficiency and environmental benefits.
Whether in packaging, construction, consumer goods, or industrial applications, EPS remains a versatile and valuable material, with the molding process playing a critical role in its wide.