The thickness of the foam mold has a crucial impact in many aspects.mold thickness also affects production efficiency.
Thicker molds may require longer heating and cooling times, thus extending the production cycle.
However, if the mold is too thin, it may not be able to guarantee sufficient strength and stability, and it is easy to be damaged during the production process, increasing the time cost of repairing and replacing the mold.
Taking the foam packaging production mold for air-conditioning cabinets as an example, the thickness of its mold core will affect the heating and heat dissipation efficiency of the mold, and thus affect the speed of the entire production process.
In addition, the thickness of the foam mold is also closely related to the cost. Too thick molds are more expensive to make and may consume more energy during use.
However, too thin molds may need to be replaced more frequently, which will also increase the overall cost.
Therefore, choosing the right foam mold thickness is crucial to balancing product quality, production efficiency and cost.
Factors Affecting Foam Mold Thickness
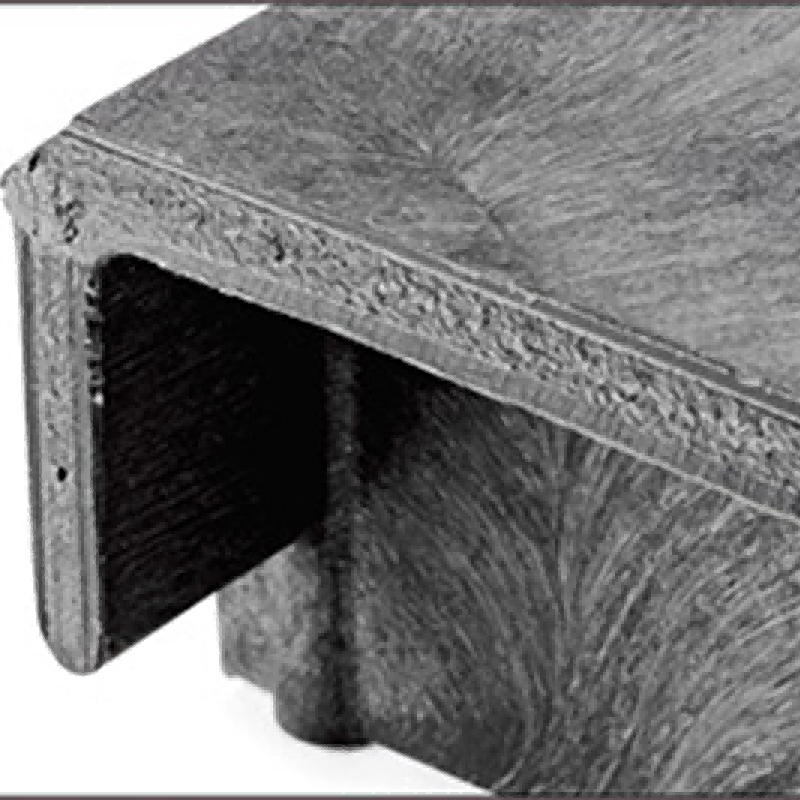
1. Product Demand Factors
Different products have specific requirements for foam mold thickness. The size of the product is an important influencing factor.
Larger products usually require thicker molds to ensure the stability and integrity of their structure.
For example, the production of large foam boards requires thicker molds to withstand the pressure during the foaming process and prevent deformation due to their large area.
If the mold thickness is insufficient, it may cause problems such as dents and unevenness in the board.
The shape of the product will also affect the thickness of the foam mold.
Products with complex shapes may require thicker molds to ensure that all parts can be fully filled and formed.
For example, foam products with deep grooves or protrusions require thicker molds to provide sufficient support and strength to ensure that these parts can be accurately formed.
2. Material Property Factors
The properties of the foam material play a decisive role in the thickness of the mold.
The hardness of the foam material will affect the choice of mold thickness.
Harder foam materials require greater pressure during the foaming process, so thicker molds are required to withstand this pressure.
For example, in polyurethane foam materials, varieties with higher hardness usually require thicker molds to prevent the mold from being damaged during the foaming process.
The density of the foam material will also affect the mold thickness.
Foam materials with higher density will produce greater expansion force during the foaming process, and thicker molds are required to control their expansion.
For example, the production of high-density polystyrene foam materials requires thicker molds to ensure the uniformity and stability of the foam.
3. Production process factors
The process parameters in the production process play an important role in the thickness of the foam mold.
Temperature is a key factor. Higher temperatures will accelerate the foaming process of the foam, but will also increase the thermal stress of the mold.
Therefore, in the high-temperature foaming process, thicker molds are required to withstand this thermal stress and prevent mold deformation.
For example, in the high-temperature foaming process of polyurethane foam, the mold temperature is usually above 100°C, which requires a thicker mold to ensure its stability.
Pressure is also an important factor affecting mold thickness.
In the high-pressure foaming process, the foam material will be subjected to greater pressure, and a thicker mold is required to withstand this pressure.
For example, in the production of some automotive interior foam products, a high-pressure foaming process is used, which requires a thicker mold to ensure the quality and stability of the product.
Methods for calculating the thickness of foam molds
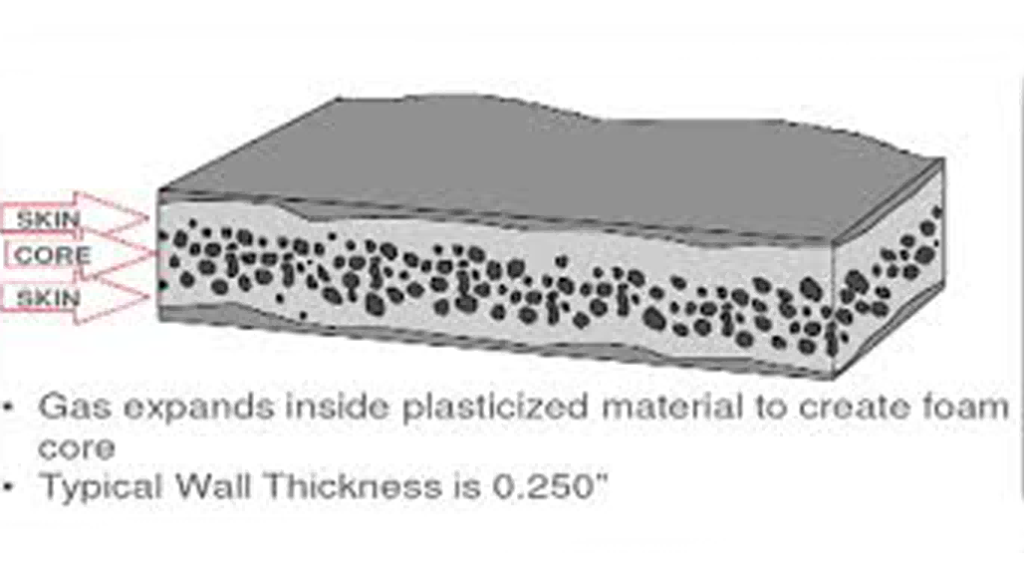
1. Formula derivation method
The thickness of foam molds can be deduced and calculated by some physical formulas.
First, we can consider the relationship between the pressure on the mold and the thickness of the mold.
According to the knowledge of material mechanics, the pressure on the mold is proportional to the cross-sectional area of the mold and inversely proportional to the thickness of the mold.
Assuming that the pressure on the mold is , the cross-sectional area of the mold is , and the thickness of the mold is , then there is (where is the force acting on the mold, and is the width of the mold).
Through this formula, we can calculate the required mold thickness based on the known pressure and mold size.
In addition, the relationship between the expansion coefficient of the foam material and the volume of the mold can also be considered.
The foam material will expand during the foaming process, and its expanded volume should be equal to the volume of the mold.
Assuming that the initial volume of the foam material is , the expanded volume is , and the expansion coefficient is , then there is .
If we know the initial volume and expansion coefficient of the foam material, as well as the shape and size of the mold, we can calculate the required mold thickness through this formula.
For example, according to the mold calculation formula data searched, for some specific mold structures, the following formula can be used for calculation: mold weight = length × width × height × specific gravity × 0.65 (0.55).
Although this formula does not directly calculate the thickness of the foam mold, the thickness of the mold can be inferred from the known parameters such as mold weight, size and specific gravity.
2. Experience reference method
In actual production, the thickness of the foam mold is often determined based on past experience and cases.
For example, for some common foam products, such as foam packaging materials, foam sheets, etc., manufacturers usually summarize the mold thickness range corresponding to different product sizes and shapes based on past production experience.
For example, for small foam packaging products, experience shows that the mold thickness is generally between 10mm and 30mm; while for medium-sized foam sheets, the mold thickness may be around 50mm-100mm.
For some special-shaped foam products, such as foam molds with complex curved surfaces, it may be necessary to refer to product cases of similar shapes to determine the appropriate mold thickness.
In addition, you can also refer to the experience of other manufacturers in the same industry.
Through visits, learning, exchanges and cooperation, we can understand the mold thickness they use when producing similar products, and provide a reference for our own production.
3. Experimental determination method
The experimental determination method is a more accurate method to determine the thickness of the foam mold. The specific steps are as follows:
① First, prepare the foam material, mold and measuring tools required for the experiment. The measuring tools can include calipers, micrometers, laser measuring instruments, etc.
② Put the foam material into the mold and conduct a foaming experiment.
During the foaming process, you can observe the expansion of the foam, record the volume change of the foam and the deformation of the mold.
③ After the foaming is completed, use the measuring tool to measure the thickness of the foam and the size of the mold.
Multiple measurements can be made at different locations, and the average value can be taken to improve the accuracy of the measurement.
④ According to the measurement results, analyze the expansion characteristics of the foam material and the bearing capacity of the mold.
If the thickness of the foam exceeds the expected range, or the mold has problems such as deformation, the thickness of the mold can be adjusted and the experiment can be repeated.
⑤ Through multiple experiments, the thickness of the mold is continuously adjusted until the optimal mold thickness that meets the product quality requirements and production process requirements is obtained.
For example, in the test method of thermal conductivity tester for foam plastics, a thickness measuring tool with an accuracy of not less than 0.05mm is used to measure the thickness of at least four places around the sample, and the arithmetic average is taken as the thickness of the sample before the test.
This method can provide a certain reference for determining the thickness of the foam mold.
At the same time, advanced measurement technologies such as laser measurement can also be used to improve the precision and accuracy of the measurement.
Precautions in practical application
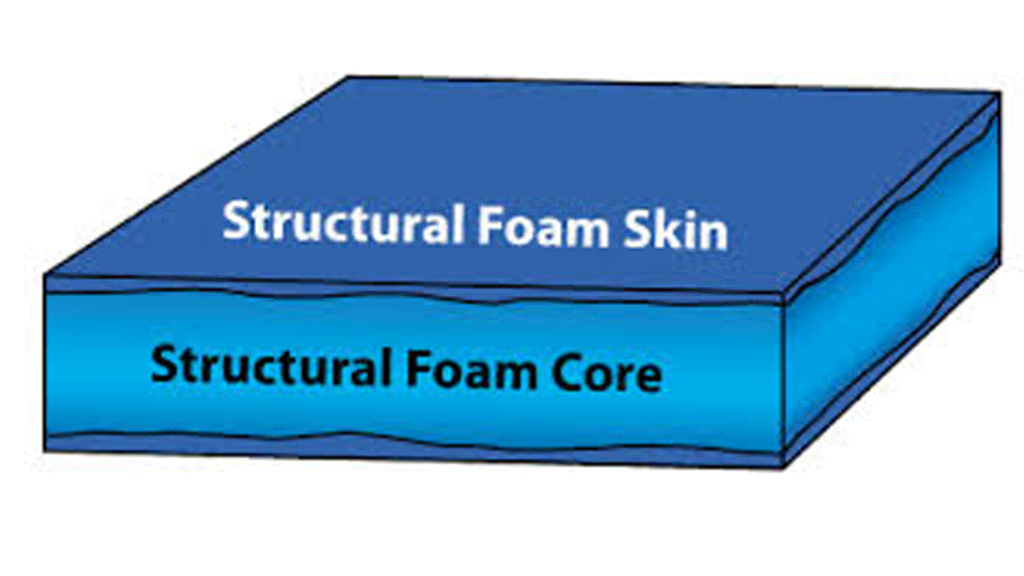
1. Error control
In the actual calculation and application of foam mold thickness, error control is crucial.
First, there may be errors in measuring the performance parameters of foam materials.
For example, the expansion coefficient of foam materials may vary due to factors such as production batches and ambient temperature, which requires multiple measurements to be averaged during measurement to reduce errors. According to relevant studies, the expansion coefficient of polyurethane foam materials in different batches may have an error of ±5%.
Secondly, there may also be errors in the size measurement of the mold. In actual production, the manufacturing accuracy of the mold may affect the calculation results of the thickness.
Generally speaking, high-precision mold manufacturing can control the size error within ±0.5mm.
Therefore, when choosing a mold manufacturer, companies with high-precision processing capabilities should be given priority.
In addition, approximate processing in the calculation process may also introduce errors.
In the formula derivation method, the application of some physical formulas may require approximate processing, which requires error evaluation.
For example, when considering the relationship between the pressure on the mold and the thickness of the mold, it is assumed that the force on the mold is evenly distributed, but in fact there may be local stress concentration, which will cause a certain deviation between the calculation result and the actual situation.
In order to control the error, the following measures can be taken:
First, conduct multiple measurements and experiments, and take the average value to improve the accuracy of measurement and calculation;
second, evaluate the errors introduced by different factors and give the error range in the calculation results;
third, regularly calibrate the measuring tools and equipment to ensure the accuracy of the measurement.

2. Safety factors
In practical applications, safety factors are also issues that need to be considered.
First, thicker foam molds may pose safety hazards to operators due to their heavy weight during use.
For example, the weight of a large foam mold may reach hundreds of kilograms or even tons.
If it is improperly operated during handling, installation and removal, it may cause injuries.
Therefore, appropriate lifting equipment and tools should be used during operation, and operators should be trained in safety.
Secondly, foam materials may generate high temperature and high pressure during the foaming process.
If the design and manufacture of the mold are unreasonable, safety accidents such as explosions may occur.
For example, during the foaming process of polyurethane foam, the reaction temperature may reach more than 150°C and the pressure may reach several MPa.
Therefore, safety factors should be taken into account when designing the mold, such as setting up safety valves, pressure sensors and other equipment to ensure that timely measures can be taken in abnormal situations.
In addition, foam materials may release harmful gases during the foaming process, which may cause harm to the health of operators if ventilation is poor.
For example, some chemical foaming agents release toxic gases such as carbon monoxide and hydrogen sulfide during decomposition.
Therefore, good ventilation conditions should be maintained during the production process, and operators should be equipped with necessary protective equipment.