Importance of smooth surface of foam mold
Foam molds with smooth surfaces offer many advantages in product manufacturing.
First, it can significantly improve product quality.
Taking EPS parts as an example, a good foam mold has a high surface gloss, which can prevent the parts from being scratched by the uneven mold surface during demoulding, reduce product surface defects, and improve product integrity.
At the same time, for foam particle parts such as expandable polypropylene (EPP), the smooth mold surface helps to improve the surface finish of the product and make the product more beautiful.
For example, in the automotive field, EPP parts are widely used. High-quality foam molds can ensure that automotive parts such as bumpers, seats, etc. look exquisite and improve the overall quality of the car.
In the field of packaging, packaging and transportation containers made from smooth foam molds not only have the characteristics of thermal insulation, heat resistance, and corrosion resistance, but their smooth surface can also improve the quality of the product, contain no volatile organic compounds, and are environmentally friendly.
In addition, for precision parts manufacturing, the smooth surface of the foam mold can provide reliable protection for precision parts, preventing potential damage to the parts during manufacturing, transportation and storage, ensuring the quality and performance of the parts.
In short, foam molds with smooth surfaces play a vital role in improving product quality and aesthetics.
Understanding the meaning of “smooth”
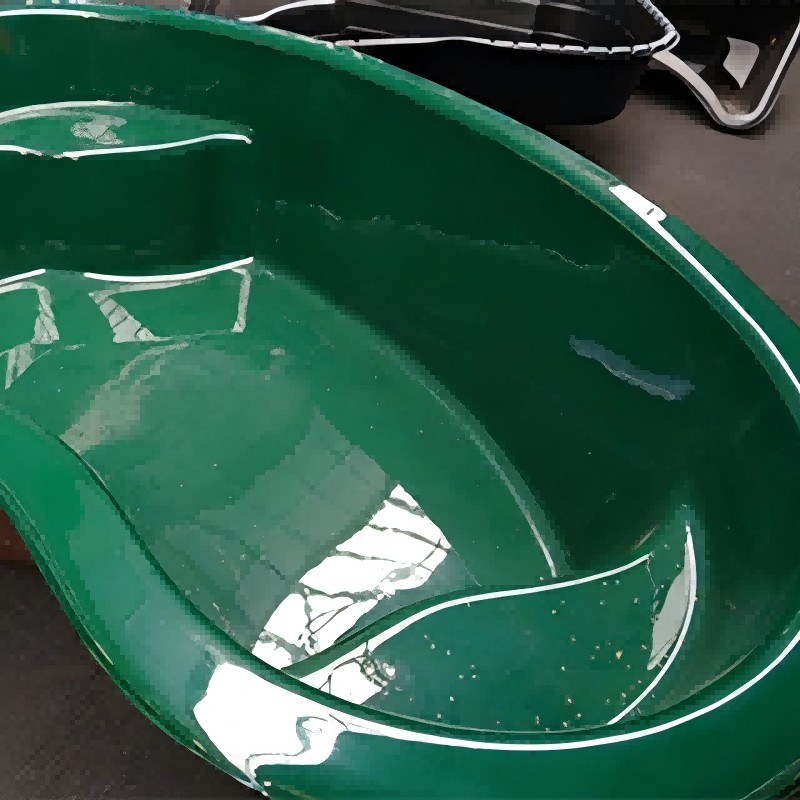
Multi-dimensional analysis of “smooth”
“Smooth” has many specific manifestations in foam molds. From the perspective of physical properties, the smooth surface of a foam mold means that its surface roughness is low.
For example, with advanced measuring instruments, the surface roughness of a good foam mold may be several microns or even lower.
This makes the foam material have very little friction with the mold surface when it is molded in the mold, which is convenient for demolding and reduces scratches and flaws on the product surface.
In terms of visual effects, the smooth surface of a foam mold has good glossiness, which can reflect light and give people a bright and neat feeling.
For example, some high-quality foam mold surfaces are like mirrors, which can clearly reflect surrounding objects.
This glossiness not only improves the appearance quality of the product, but also makes the product more competitive in the market.
In addition, the smooth surface of a foam mold also has uniformity.
This means that the smoothness of the entire mold surface is consistent, and there are no obvious uneven or locally rough areas.
For example, when making large foam products, such as foam ship models, the uniform smoothness of the entire mold surface is crucial to ensure the shape accuracy and appearance quality of the ship model.
If there are uneven areas on the mold surface, the ship model may have inconsistent thickness and uneven surface in some parts, affecting the performance and appearance of the ship model.
Distinction from related concepts
“Smooth” is related to but different from concepts such as “flat” and “uniform”.
“Flat” mainly emphasizes that the mold surface has no obvious ups and downs, focusing on the levelness of the plane.
“Smooth” emphasizes the fineness and low roughness of the surface. Even if the surface is flat, it cannot be called smooth if the roughness is high.
For example, a foam mold with a seemingly flat surface may have fine particles or lines when touched or observed under a magnifying glass. This is not a smooth surface.
“Uniform” focuses on the consistency of the entire mold surface in various parts.
Although a smooth surface usually has a certain degree of uniformity, uniformity does not necessarily mean smoothness.
For example, a mold surface has consistent thickness in various parts, but there may be some tiny flaws or places with high roughness, which is not a smooth surface.
The smooth foam mold surface not only has low roughness in various parts, but also has a high degree of consistency in appearance and performance.
Preparation for a smooth surface
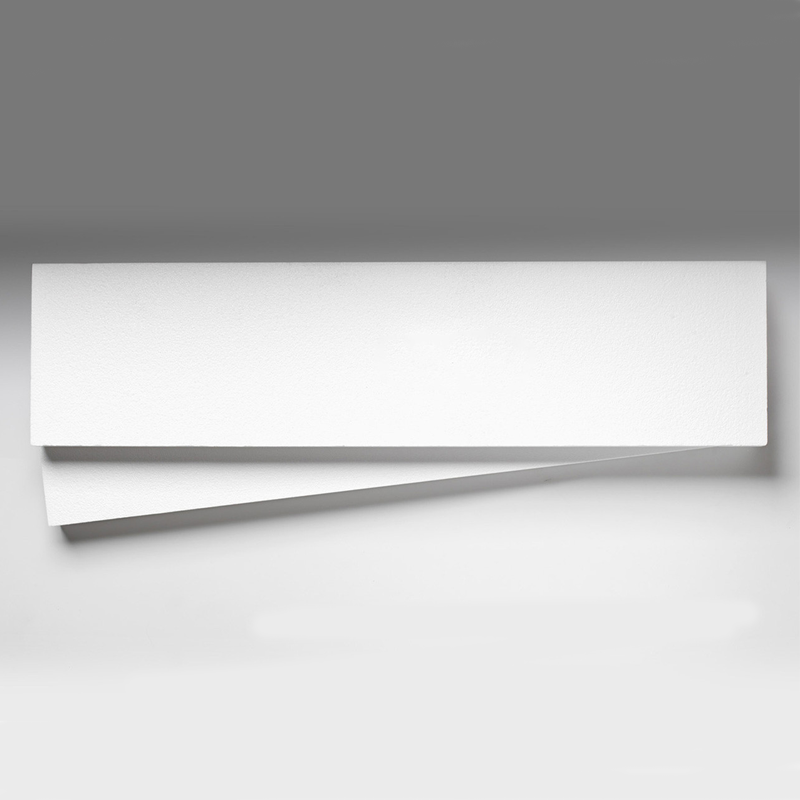
Choosing the right foam mold material
The choice of foam mold material is crucial to achieving a smooth surface. Different materials have different effects on the smooth surface.
For example, for iron casting, ceramic materials such as alumina with high thermal tolerance and stability are usually used.
This material can maintain good shape stability at high temperatures, which helps to form a smooth surface during the casting process.
For aluminum casting, polystyrene foam or polystyrene foam coated with silica sand (EPS/SLS) materials are more commonly used because they can withstand lower casting temperatures and have a relatively smooth surface, which is beneficial to the surface finish of aluminum products.
For brass casting, the thermal conductivity of the mold material needs to be considered.
Gypsum or other low thermal conductivity materials are usually used to avoid uneven heat conduction during the casting process.
When selecting foam mold materials, multiple factors should be considered comprehensively.
The first is temperature tolerance. Make sure that the material can withstand the high temperatures during the casting process.
For example, high specific surface area calcium hydroxide is usually not suitable for applications that are in direct contact with molten metal because of its low temperature tolerance.
Secondly, thermal conductivity. Materials with higher thermal conductivity help dissipate heat, but may cause the casting surface to be rough.
In cases where fine surface quality is required, materials with lower thermal conductivity can be selected.
In addition, the density and strength of the material are also critical. Appropriate density and strength can provide sufficient structural support without making the mold too fragile or too heavy.
Chemical stability should not be ignored. The chemical compatibility between the foam mold material and specific metals or alloys should be considered to avoid corrosion of certain alloys on the mold material.
Finally, cost and availability should also be considered to ensure that the selected material is feasible within the budget and time constraints.
Prepare necessary tools and materials
Some necessary tools and auxiliary materials are required to achieve a smooth surface.
First, advanced measuring equipment, such as a surface roughness meter, is required to detect the roughness of the foam mold surface to ensure that the smooth standard is met.
Secondly, sandpaper and oilstone can be used to perform preliminary grinding on the mold surface to remove surface flaws and unevenness.
Wool wheels can be used for further polishing to improve the gloss of the surface. Alloy files and fiber oilstones can play a role in places where fine finishing is required.
For mold materials made of aluminum or copper alloys, a release agent should be prepared on the cavity surface.
On the one hand, the release agent can protect the mold cavity from corrosion, and on the other hand, it makes the mold easy to demold. In addition, some coating materials with good self-lubrication and corrosion resistance can be prepared, such as TPU leveling agents used to improve the surface finish and flatness of TPU plastics.
This leveling agent is mainly made of polysiloxane, magnesium silicate and other materials, which can form a uniform film on the mold surface and fill the tiny holes on the uneven surface, thereby improving the surface quality of the mold.
At the same time, for foam molds that need to be treated at high temperatures, some materials with good heat resistance can be prepared, such as coatings that can adapt to temperatures within 300°C to ensure that the mold surface remains smooth under high temperature conditions.
Specific operation steps
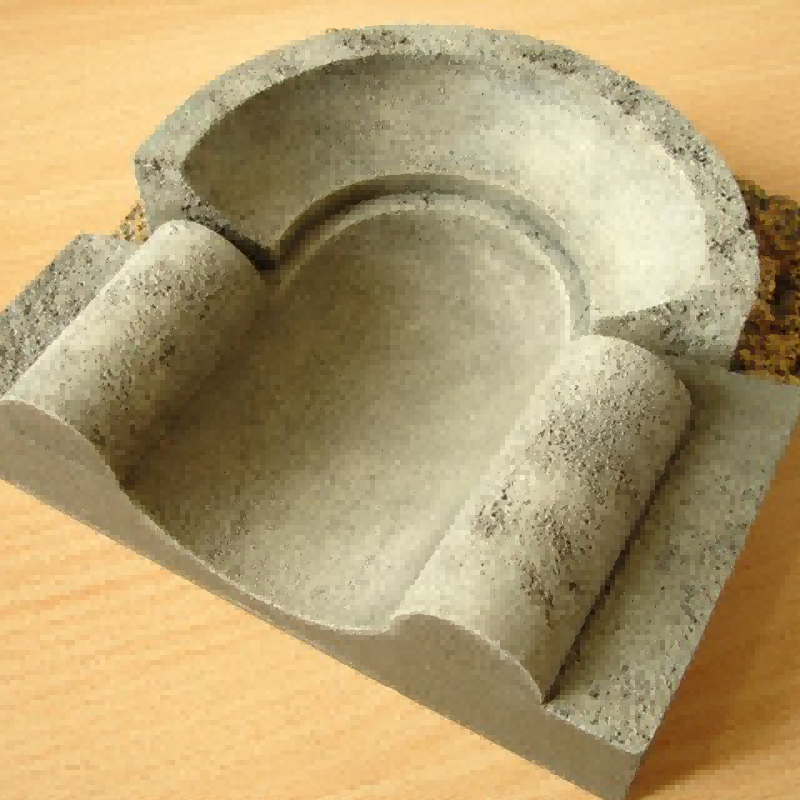
Preliminary treatment of foam mold
Cleaning is the first step to achieve a smooth surface of the foam mold.
Since foam mold cleaning is a very tricky problem, the foam glue on the mold surface is very sticky and difficult to clean.
Dry ice cleaning technology can be used.
Under the action of high-speed airflow, dry ice particles will evaporate quickly when they contact the mold surface, producing a condensation effect, instantly freezing and bursting the dirt on the mold surface, thereby achieving the cleaning effect.
For example, polyurethane foam cleaning machine and mold dry ice cleaning machine are both equipment specially used for cleaning foam molds.
They use dry ice cleaning technology, with a dedicated spray gun and airflow system, to finely clean the mold surface, which is efficient, environmentally friendly and safe.
Removing impurities is also a key link. After heating and evaporation, water will form scale such as magnesium carbonate and calcium carbonate, which seriously affects the cooling effect of the mold.
You can choose a scale filter according to the amount of water used, or a magnetic water processor commonly used in industry to remove scale, to effectively remove scale impurities in the mold.
Use specific technical means
Grinding is one of the important methods to achieve smoothness.
A foam mold surface grinding device can be used, which includes a box body, a three-axis mobile platform is installed on the top of the inner side of the box body, and a grinding mechanism is arranged on the mobile platform of the platform.
The grinding mechanism includes a motor ⅰ, and a grinding sand rod is connected to the output shaft of the motor ⅰ, and a connecting plate is connected to the grinding sand rod.
Five inverted U-shaped sliding rods that can move up and down are evenly spaced along the radial direction of the connecting plate, and an annular grinding wheel is connected to the bottom.
The diameters of the five annular grinding wheels increase from the inside to the outside.
By controlling the three-axis mobile platform and the motor ⅰ to work, the grinding sand rod and the annular grinding wheel are used to grind the surface of the foam mold.
At the same time, a driving component is provided on the connecting plate, which can drive a single inverted U-shaped sliding rod to move down, and select an annular grinding wheel of appropriate size for grinding, so as to meet diversified needs and improve grinding efficiency.
Applying special materials can also improve smoothness. In the case where the mold material is aluminum or copper alloy, a release agent can be applied to the surface of the cavity.
On the one hand, it protects the mold cavity from corrosion, and on the other hand, it makes the mold easy to demold.
In addition, some coating materials with good self-lubrication and corrosion resistance can also be used, such as TPU leveling agents used to improve the surface finish and flatness of TPU plastics, forming a uniform film on the mold surface, filling tiny holes, and improving surface quality.
For foam molds that need to be treated at high temperatures, you can apply a coating that adapts to temperatures within 300°C to ensure that the mold surface remains smooth under high temperature conditions.
Inspection and Adjustment
There are many ways to check the smoothness of the foam mold.
First, you can observe the mold surface to see if there are slight scratches, unevenness, darkening of light and shadow, etc.
Place the mold under a bright light source and observe from different angles to fully evaluate its flatness.
Secondly, touch the mold surface with your hand to feel whether it is smooth and whether there are burrs, sand holes and other unevenness.
You can also use standard samples for comparison, such as the unpolished surface of the same mold, the surface of other molds, or industry standard samples, to find out whether there are minor unevenness or flaws on the mold surface through comparison and observation.
Use precision measuring tools such as dial indicators or micrometers to measure the mold surface and quantify the flatness of the mold surface.
Observe the gloss of the mold surface. High gloss usually means that the mold surface is very smooth and flat.
It can be measured using professional equipment such as gloss meters.
Use a magnifying glass or microscope to observe the microstructure of the mold surface to see if there are minor defects such as scratches and flaws.
For mirror molds, you can judge whether the mold polished surface is flat and smooth by whether the mold surface imaging reference is rippled.
If it is found that the smoothness does not meet the requirements, necessary adjustments need to be made.
According to the inspection results, select the appropriate grinding tool or adjust the thickness of the coating material, etc., and process again until the smoothness meets the requirements.
Subsequent maintenance and care
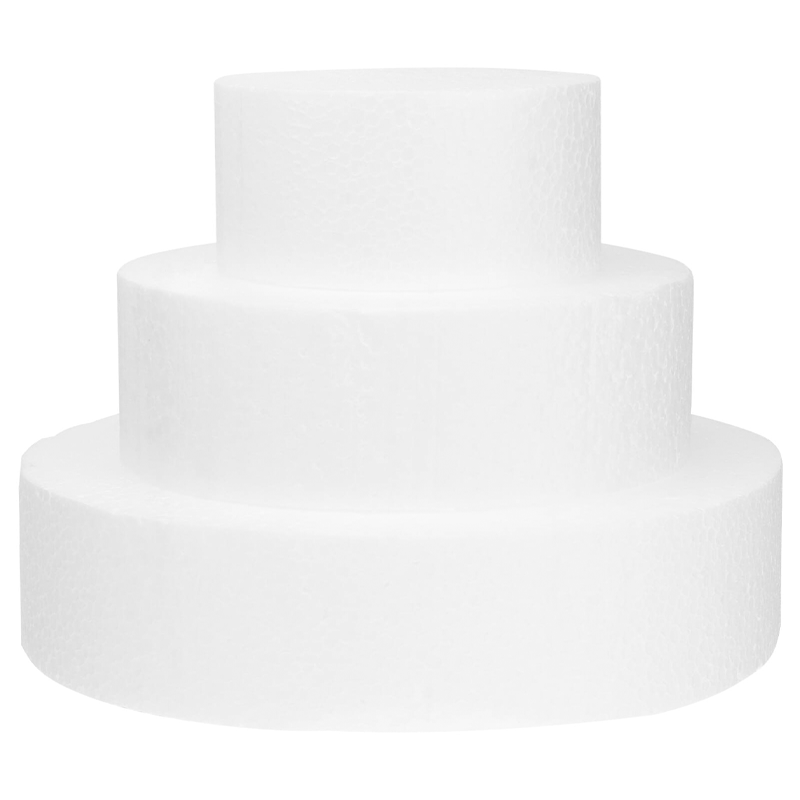
Daily use precautions
When using foam molds in daily life, they should be handled with care.
According to relevant information, molds should be handled with care during production and use.
The release agent should be sprayed wet when used. Shake well before use.
The crust stuck on the surface of the mold should be cleaned with a production knife before making the next mold.
This can avoid damage to the mold surface due to collision or improper operation, affecting the smoothness.
At the same time, be careful to prevent the mold from being scratched by sharp objects.
For example, during storage and transportation, make sure that there are no sharp corners or protrusions in the surrounding environment to avoid accidentally scratching the mold surface.
Regular cleaning and maintenance
Regular cleaning of foam molds is an important part of maintaining a smooth surface.
You can use dry ice cleaning technology or professional cleaning equipment similar to the initial treatment to deeply clean the mold every once in a while.
Such as polyurethane foam cleaning machine and mold dry ice cleaning machine, they can effectively remove dirt and residual foam on the mold surface and restore the smoothness of the mold.
For the hinges of the mold and other parts that are prone to rust, add engine oil and butter for maintenance to prevent rust when not in use, causing the gap to be too large, resulting in the mold being misaligned and unusable.
In addition, the mold surface can also be regularly treated with anti-rust to prevent rust caused by water leakage, condensation, rain and fingerprints.
For example, carefully wipe the cavity, ejection mechanism and row position, and spray the mold rust remover and grease.
Reasonable storage
The storage environment of the foam mold also has a great impact on the maintenance of its smooth surface and service life.
The mold should not be piled up in the open air as much as possible. If conditions permit, it can be covered with a rain cloth and painted for protection.
This can prevent the mold from being affected by natural factors such as sunlight, rain, wind erosion, etc., and prevent surface aging, rust or damage.
When the mold is not in use, it should be taken off the mold frame and laid flat on the ground to prevent deformation.
And the mold lock should be tightened to further ensure the stability of the mold shape.
If conditions permit, when the mold is withdrawn from the production line, a mold product can be placed inside without being taken out.
This can prevent deformation and help maintain the smooth surface of the mold.
At the same time, attention should be paid to the dryness and ventilation of the storage environment to avoid the mold from getting moldy or rusting due to the humid environment.
Timely repair and replacement of vulnerable parts
During the continuous operation of the mold, the smooth surface of the mold may be affected due to problems such as component wear, pressure damage, partial damage, water leakage and movement.
Therefore, mold maintenance is required in a timely manner. Regularly remove rust (appearance, PL surface, cavity, core, etc.), re-lubricate (ejection mechanism, production line position, etc.), and replace vulnerable parts (rods, bolts, etc.).
For example, when scratches or wear are found on the surface of the mold, it should be polished and repaired in time; if some parts of the mold are severely damaged and cannot be repaired, they should be replaced in time to ensure the overall performance and smooth surface of the mold.
In short, through daily use precautions, regular cleaning and maintenance, reasonable storage, and timely repair and replacement of vulnerable parts, the smooth surface of the foam mold can be effectively maintained, its service life can be extended, and reliable guarantee can be provided for the production of high-quality foam products.
Summary
Methods and key points for achieving smooth surface of foam mold
Achieving a smooth surface for a foam mold requires multiple aspects.
First, understand the importance of a smooth surface, which not only improves product quality and aesthetics, but also provides reliable protection for precision parts.
When understanding the meaning of “smooth”, it is necessary to analyze it from multiple dimensions, including low surface roughness, good gloss and uniformity, and at the same time distinguish it from concepts such as “flat” and “uniform”.
In terms of preparation, it is crucial to choose the right foam mold material, taking into account factors such as temperature tolerance, thermal conductivity, density, strength, chemical stability, as well as cost and availability.
At the same time, prepare the necessary tools and materials, such as advanced measuring equipment, grinding tools, release agents, coating materials, etc.
The specific steps include preliminary processing of the foam mold, such as using dry ice cleaning technology to remove dirt and impurities; using specific technical means, such as grinding and applying special materials to improve smoothness; and checking and adjusting to ensure that the smoothness meets the requirements.
Subsequent maintenance and care should not be neglected. In daily use, it should be handled with care to prevent scratches; regular cleaning and maintenance, using dry ice cleaning technology and rust prevention treatment; reasonable storage to avoid the influence of natural factors; timely repair and replacement of vulnerable parts to ensure the overall performance and smooth surface of the mold.