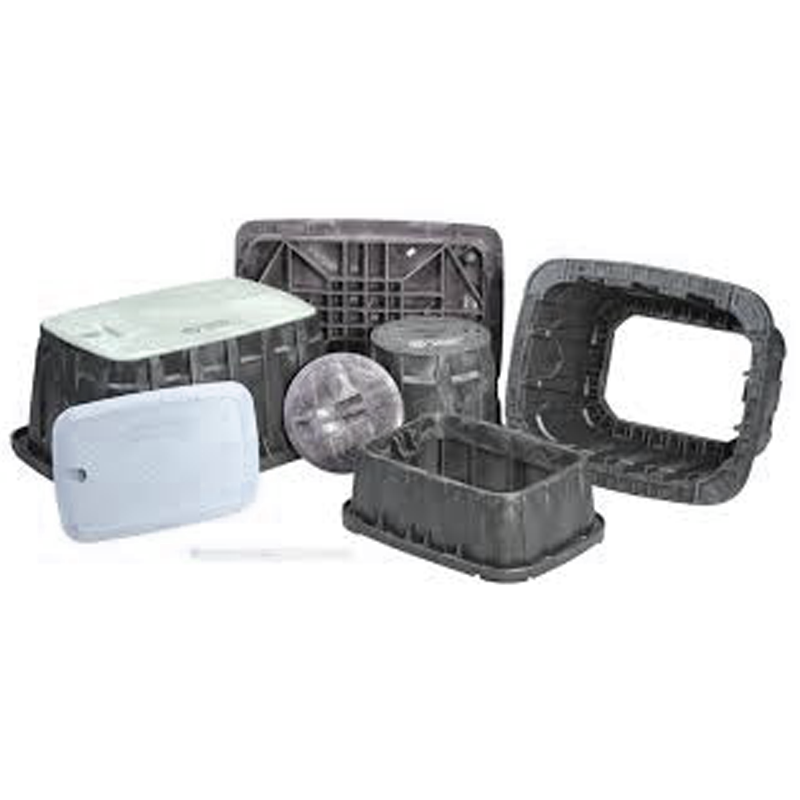
A foam mold is a type of mold made from foam material, typically used in manufacturing and prototyping to create lightweight and intricate parts.
These molds are employed in various industries, including automotive, aerospace, packaging, and consumer goods.
Creating foam molds is a fascinating and practical skill, useful for a wide range of projects including casting, prototyping, and sculpting.
Foam molds are lightweight, easy to work with, and can be used with various casting materials such as plaster, resin, or concrete.
1. Introduction to Foam Molding
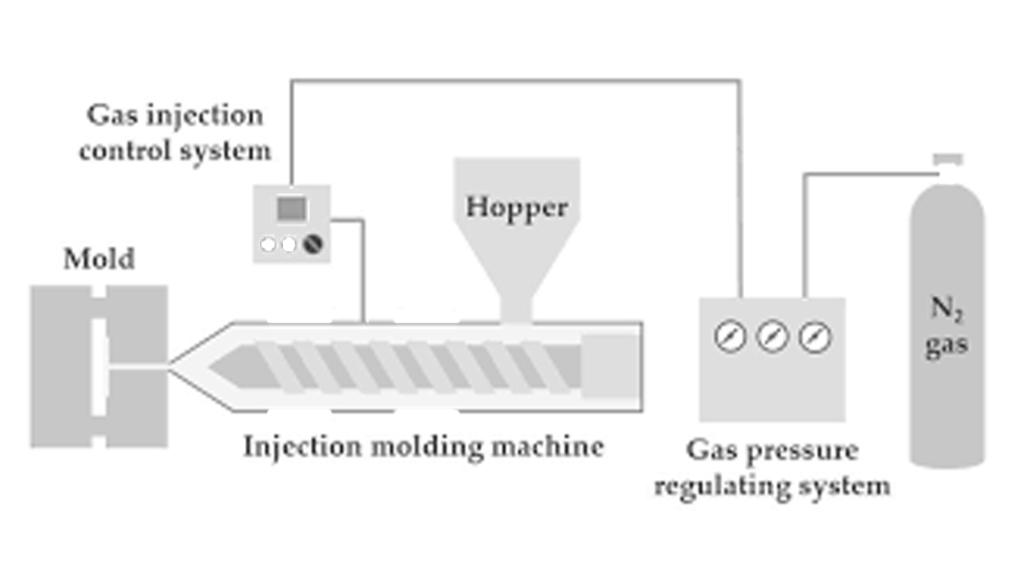
Foam molding is a technique where foam blocks are shaped into molds for casting materials.
This method is widely used in industries like automotive, construction, and arts and crafts.
Foam molds are particularly popular because they are inexpensive, lightweight, and easy to manipulate.
2. Materials and Tools Needed
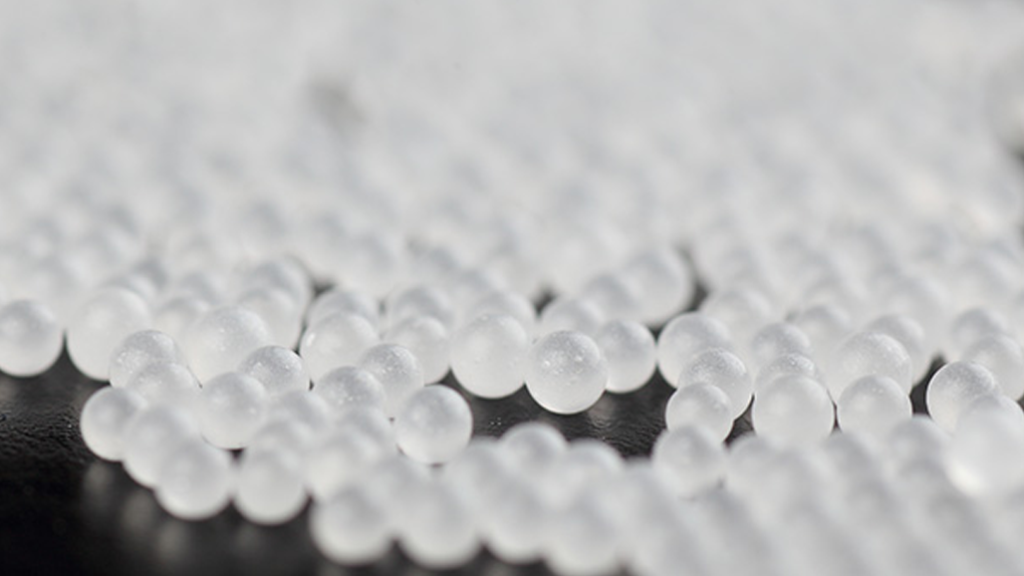
Before starting your foam molding project, gather the following materials and tools:
– Foam Blocks: Choose high-density foam for better durability and precision.
– Cutting Tools: Utility knives, hot wire cutters, and scalpels for shaping the foam.
– Sandpaper: Various grits for smoothing the surface.
– Sealant: PVA glue, epoxy resin, or latex paint to seal the foam.
– Release Agent: To prevent casting material from sticking to the mold.
– Casting Material: Plaster, resin, or concrete depending on your project.
– Mixing Containers and Stirrers: For preparing the casting material.
– Protective Gear: Gloves, goggles, and a mask for safety.
3. Designing Your Mold
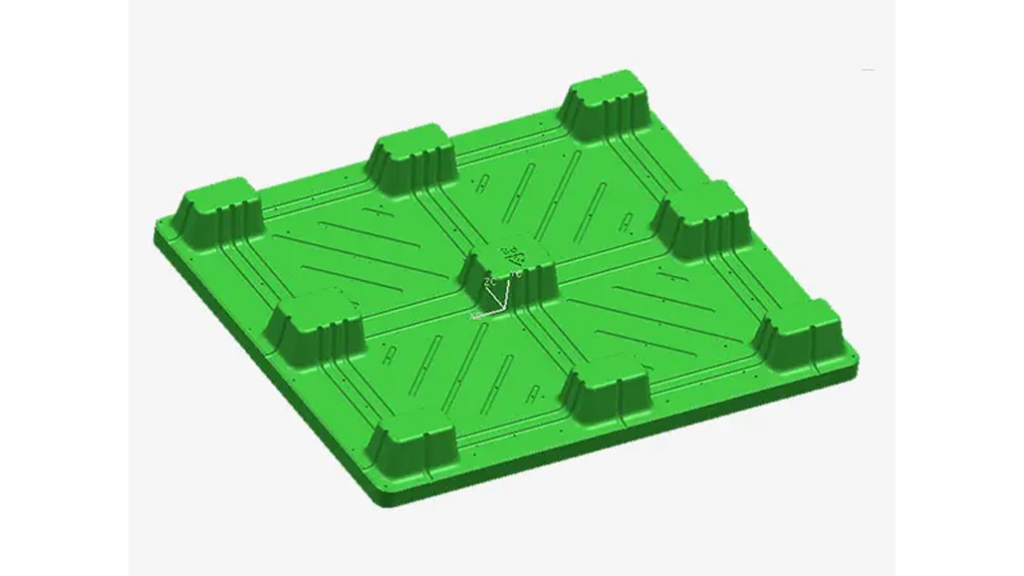
Start by sketching your design. Consider the dimensions and details you want to incorporate.
It’s essential to plan the mold in sections if it’s a complex shape, ensuring easy removal of the cast.
For beginners, simple designs like geometric shapes are ideal.
4. Preparing the Foam Block
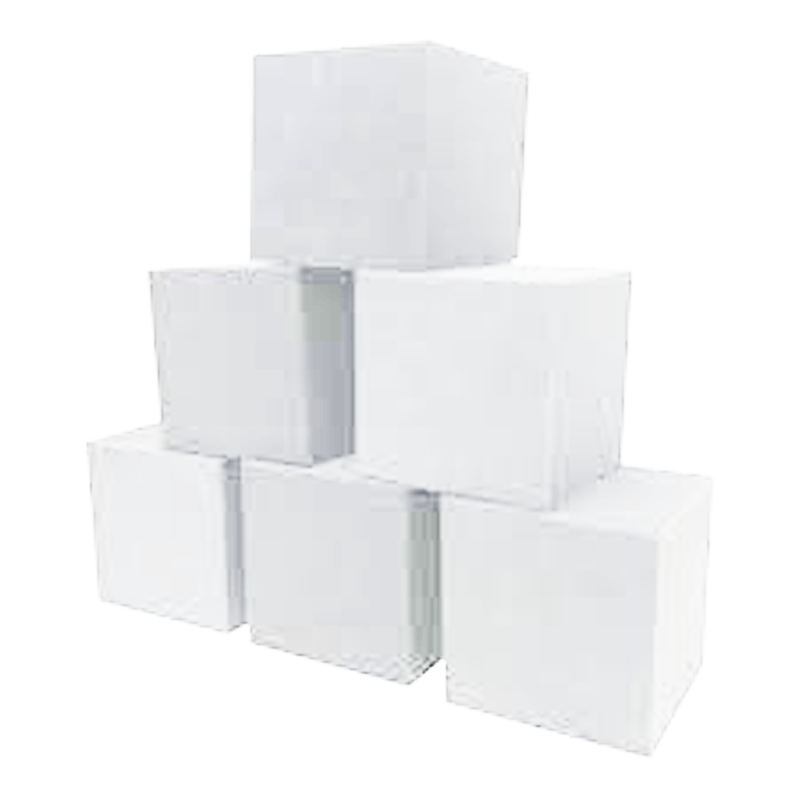
Cut the foam block to the approximate size of your design. Ensure you have extra foam around the edges to allow for final adjustments.
If your project requires multiple pieces, cut the foam accordingly and mark each section for easy assembly.
5. Carving the Foam Mold

Step-by-Step Carving Process:
1. Outline Your Design: Transfer your design onto the foam block using a marker.
2. Rough Cuts: Use a utility knife or hot wire cutter to remove large sections of foam.
3. Detailing: Switch to finer tools like scalpels or smaller knives for intricate details.
4. Smoothing: Use sandpaper to smooth out rough edges and refine the shape.
Tips for Carving:
– Work slowly and carefully, especially with detailed sections.
– Regularly compare your progress with your design sketch.
– Keep your tools sharp to make clean cuts.
6. Sealing the Foam Mold
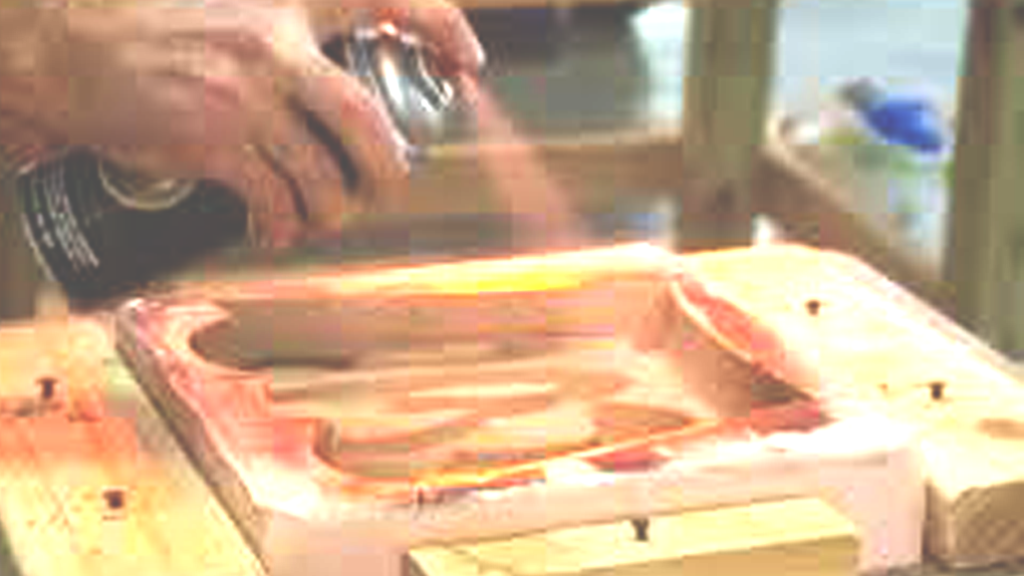
Sealing the foam mold is crucial to ensure the casting material does not damage the foam or adhere to it. Follow these steps to seal your mold:
1. Apply Sealant: Brush on a thin layer of PVA glue, epoxy resin, or latex paint.
2. Drying: Allow the sealant to dry completely. This may take several hours.
3. Additional Coats: Apply multiple coats if necessary, ensuring each layer dries before adding the next.
7. Casting the Mold
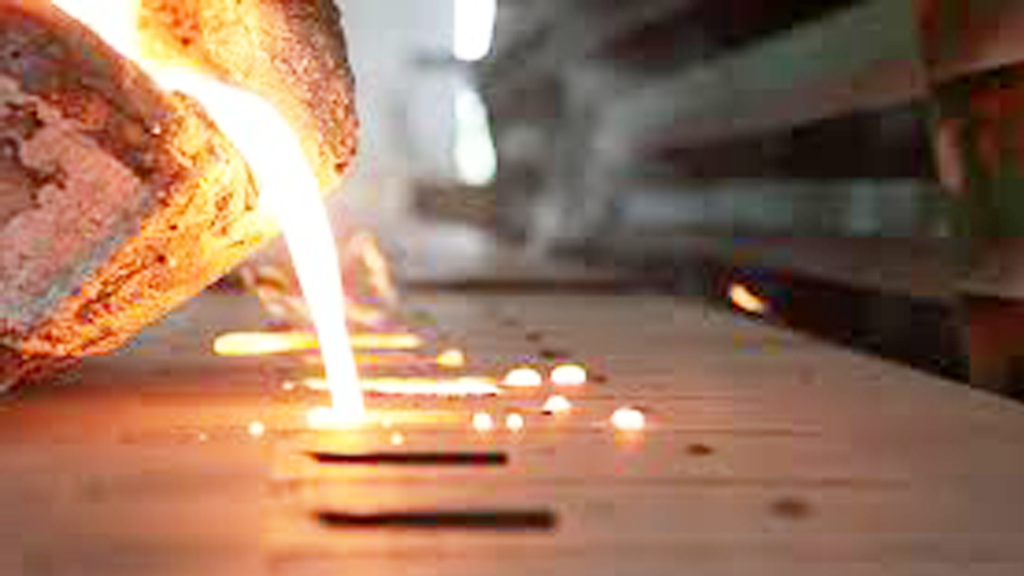
Once your mold is sealed and ready, it’s time to cast. Here’s how to do it:
Preparing the Casting Material:
1. Read Instructions: Follow the manufacturer’s instructions for mixing your casting material.
2. Mixing: Combine the components in a mixing container and stir thoroughly to avoid lumps.
Pouring the Cast:
1. Release Agent: Apply a release agent to the mold to facilitate easy removal of the cast.
2. Pouring: Slowly pour the casting material into the mold, ensuring it reaches all areas.
3. Tapping: Gently tap the mold to remove air bubbles.
8. Removing the Cast
After the casting material has set (refer to the manufacturer’s instructions for setting times), carefully remove the cast from the foam mold:
1. Disassemble Sections: If your mold is in sections, gently separate them.
2. Extract the Cast: Carefully pull out the cast, starting from the edges.
3. Clean the Cast: Remove any remaining release agent or residue.
9. Finishing Touches
Once you have removed the cast, you may need to perform some finishing touches:
1. Sanding: Use fine-grit sandpaper to smooth out any imperfections.
2. Painting: Paint or finish the cast as desired to achieve the final look.
10. Tips and Tricks for Successful Foam Molding
– Choose the Right Foam: High-density foam provides better detail and durability.
– Sharp Tools: Keep your cutting tools sharp for precise and clean cuts.
– Proper Ventilation: Work in a well-ventilated area, especially when using sealants and casting materials.
– Patience: Take your time with each step to ensure the best results.
11. Common Mistakes and How to Avoid Them
Mistake: Using Low-Density Foam
Solution: Always opt for high-density foam to ensure your mold retains its shape and details.
Mistake: Insufficient Sealing
Solution: Apply multiple layers of sealant and allow each to dry thoroughly.
Mistake: Air Bubbles in Cast
Solution: Tap the mold gently after pouring the casting material to release trapped air.
12. Applications of Foam Molds
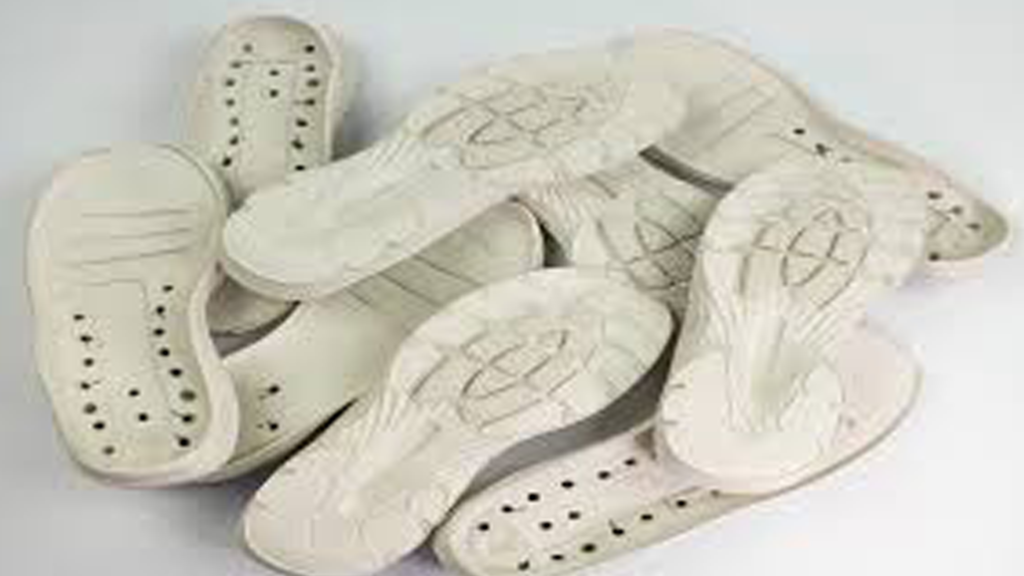
Foam molds have a wide range of applications across various industries:
– Prototyping:Creating prototypes for products and designs.
– Art and Sculpture:Crafting intricate sculptures and artistic pieces.
– Construction:Making architectural models and decorative elements.
– Automotive:Designing car parts and custom modifications.
13. Maintenance and Storage of Foam Molds
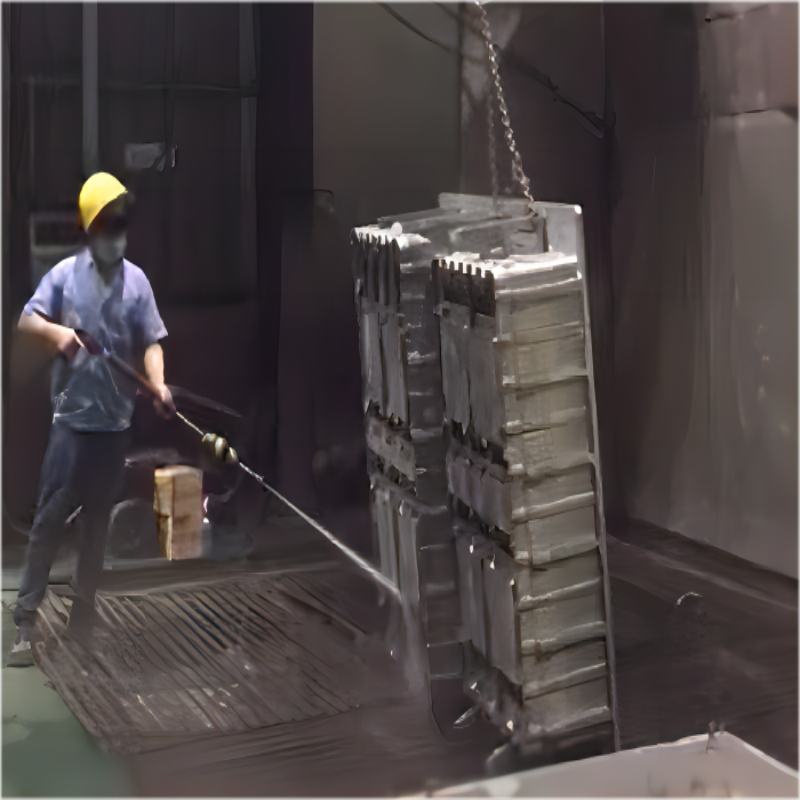
Proper maintenance and storage of your foam molds will extend their lifespan and usability.
Cleaning the Mold
After each use, clean your foam mold to remove any residual casting material:
1. Gentle Cleaning: Use a soft brush or cloth to gently remove any debris or residue.
2. Mild Cleaners: If necessary, use mild soap and water. Avoid harsh chemicals that can damage the foam or sealant.
Storing the Mold
Store your foam molds properly to prevent damage:
1.Dry Environment: Ensure the molds are stored in a dry, cool place to avoid moisture damage.
2.Protective Covering: Cover the molds with plastic wrap or store them in protective containers to prevent dust and physical damage.
14. Troubleshooting Common Issues
Even experienced mold makers encounter challenges. Here are solutions to some common issues:
Issue: Uneven Surfaces
Solution: Ensure your foam block is uniformly cut and sanded before starting. During carving, use a steady hand and consistent pressure to maintain even surfaces.
Issue: Mold Deformation
Solution: Reinforce the mold with additional support structures. Always handle the mold gently, especially during the casting and removal process.
Issue: Difficult Cast Removal
Solution: Apply a sufficient amount of release agent before casting. Consider designing the mold in sections to facilitate easier removal.
15. Environmental Considerations
Foam molding involves materials that can impact the environment. Here’s how to minimize your ecological footprint:
Recycling and Reusing Foam
Whenever possible, recycle or reuse foam scraps:
1.Repurposing:Use leftover foam pieces for smaller projects or as filler for other molds.
2.Recycling:Check local recycling programs for proper foam disposal options.
Eco-Friendly Alternatives
Explore eco-friendly alternatives to traditional foam and casting materials:
1.Biodegradable Foams:Use biodegradable or recyclable foam options.
2.Natural Casting Materials:Opt for natural casting materials like eco-resin or clay.
16. Conclusion
Foam molding is a versatile and accessible technique that opens up a world of creative and practical possibilities.
Whether you are a hobbyist looking to create unique art pieces or a professional aiming to prototype new products, mastering the art of foam molding can significantly enhance your capabilities.