Introduction to EPS Foam Mold
Introduce the basic concept and application scope of EPS foam mold, explaining its importance in various industries.
EPS foam mold, short for Expanded Polystyrene foam mold, refers to a tool or form used to shape and produce EPS foam products.
It plays a crucial role in multiple industries due to its unique properties and wide range of applications.
In the packaging industry, EPS foam molds are indispensable.
They are used to create protective packaging for fragile items such as electronics, glassware, and delicate machinery.
The custom-shaped molds ensure a snug fit, providing excellent shock absorption and protection during transportation and storage.
The construction industry also benefits from EPS foam molds.
They can be employed to manufacture insulation materials that help improve energy efficiency in buildings by reducing heat transfer.
Additionally, EPS foam molds are used for creating decorative elements and architectural components.
In the automotive sector, EPS foam molds are used to produce lightweight components for vehicle interiors, contributing to fuel efficiency and reducing the overall weight of the vehicle.
The importance of EPS foam molds lies in their ability to create precise and consistent products that meet specific requirements.
They offer cost-effective solutions for mass production, allowing for efficient manufacturing processes and high-quality output.
Moreover, the flexibility of EPS foam molds enables the creation of complex shapes and designs, making them suitable for a wide variety of applications across different industries.
Production Process of EPS Foam Mold
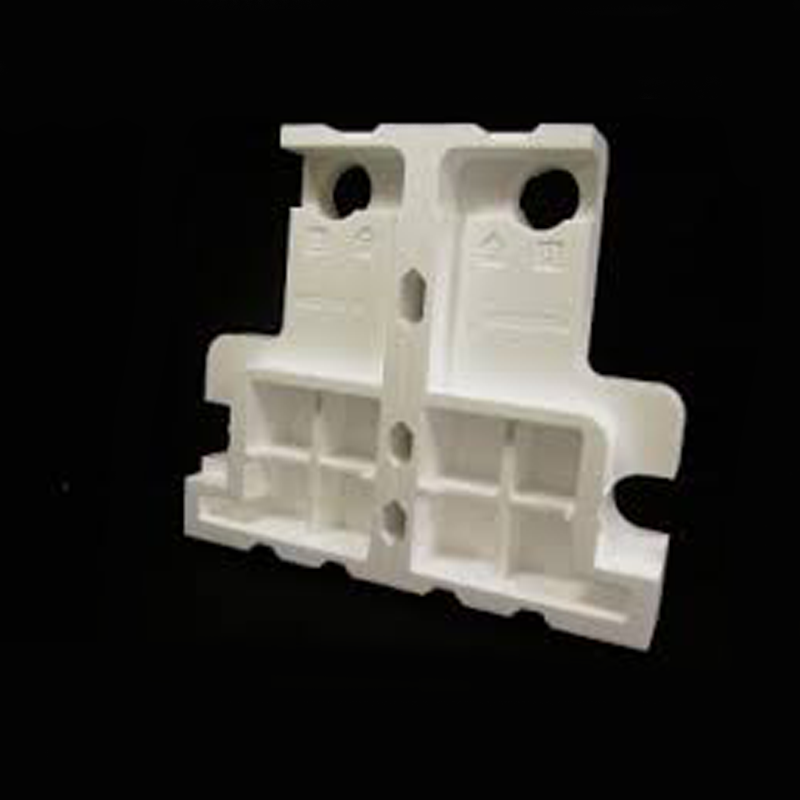
1.Raw Material Preparation
The selection of raw materials for EPS foam mold production is crucial.
EPS particles of high quality are typically chosen, ensuring uniform size and density.
Additives such as flame retardants and colorants may also be incorporated depending on the specific requirements of the final product.
Water is another important component, and its purity and quantity need to be precisely controlled.
Before use, the EPS particles are often dried to remove any moisture that could affect the foaming process.
2.Pre-Foaming
The pre-foaming process is a critical step. It is carried out in specialized equipment under controlled temperature and pressure conditions.
Typically, the temperature is maintained within a specific range, usually around 90-100°C, and the pressure is adjusted accordingly.
This helps the EPS particles expand and form a preliminary foam structure.
3.Maturation
Maturation is an important process that follows pre-foaming.
During this stage, the foam is left to stabilize and the structure becomes more uniform.
This allows for better mechanical properties and dimensional stability of the final foam product.
The duration of maturation depends on various factors such as the type of EPS used and the processing conditions.
4.Forming
The forming process involves placing the pre-foamed and matured material into molds.
The molds are designed to give the desired shape to the EPS foam mold.
Key points in this process include ensuring proper filling of the mold, uniform distribution of the foam, and maintaining the correct pressure and temperature to achieve a dense and consistent structure.
5.Demolding and Cutting
After the forming process is complete, demolding is carried out.
Careful handling is necessary to avoid damaging the foam mold.
The final product is then cut to the exact dimensions and shape as per the design requirements.
Sophisticated cutting tools and techniques are employed to ensure clean and precise cuts, resulting in a high-quality EPS foam mold.
Material Selection for EPS Foam Mold
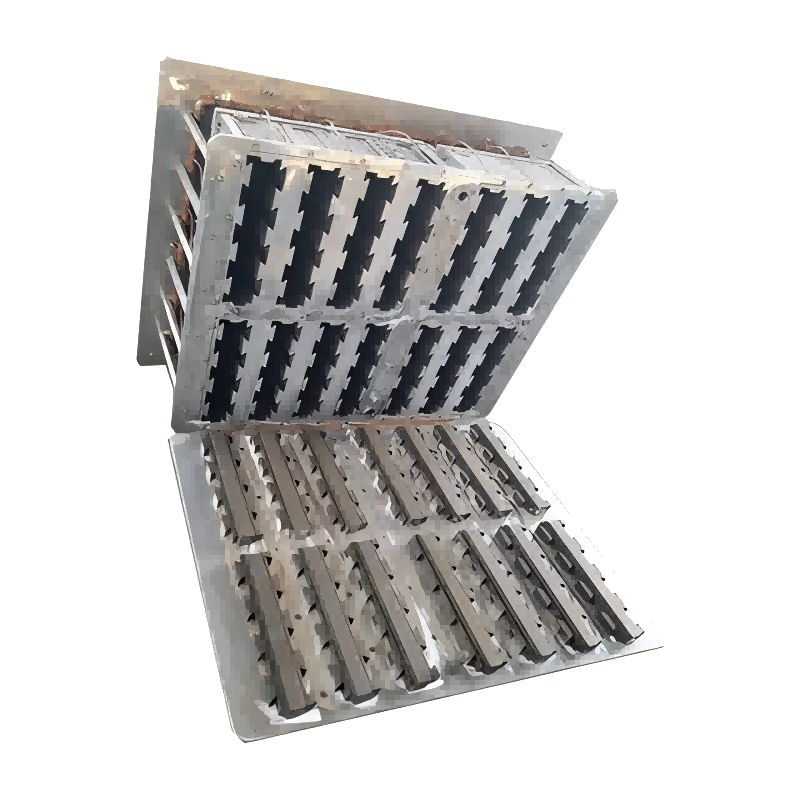
1.Traditional Materials and Their Limitations
Traditionally, EPS foam molds have relied on materials like pure EPS or simple blends.
Pure EPS offers decent insulation and lightweight properties but may lack sufficient strength and durability for certain demanding applications.
Simple blends, while sometimes enhancing certain characteristics, often have limitations in terms of heat resistance and chemical stability.
For instance, in high-temperature environments or when exposed to certain chemicals, these traditional materials might deform, lose their structural integrity, or show reduced performance over time.
2.Composite Materials
Composite materials, such as EPS-Resin composites, have emerged as a game-changer in the field.
These composites combine the lightweight and insulation properties of EPS with the strength and durability of resins.
This makes them suitable for applications where both mechanical strength and thermal insulation are crucial.
For example, in the automotive industry, EPS-Resin composites can be used to create complex structural components that need to withstand vibrations and varying temperatures.
Their enhanced mechanical properties also make them ideal for use in aerospace and high-performance engineering applications.
3.New Materials and Trends
In recent years, there has been a growing interest in new materials for EPS foam molds.
Nanomaterials, for instance, are being explored for their potential to improve the performance of the foam at a microscopic level.
Smart materials that can respond to changes in the environment, such as temperature or pressure, are also on the horizon.
Looking towards the future, there is a trend towards developing sustainable and recyclable materials that minimize the environmental impact of EPS foam mold production.
Materials derived from renewable sources or those that can be easily recycled and reused are likely to gain more prominence.
Additionally, research is ongoing to create materials with enhanced fire resistance and improved electrical conductivity to meet the evolving needs of various industries.
Key Points and Precautions
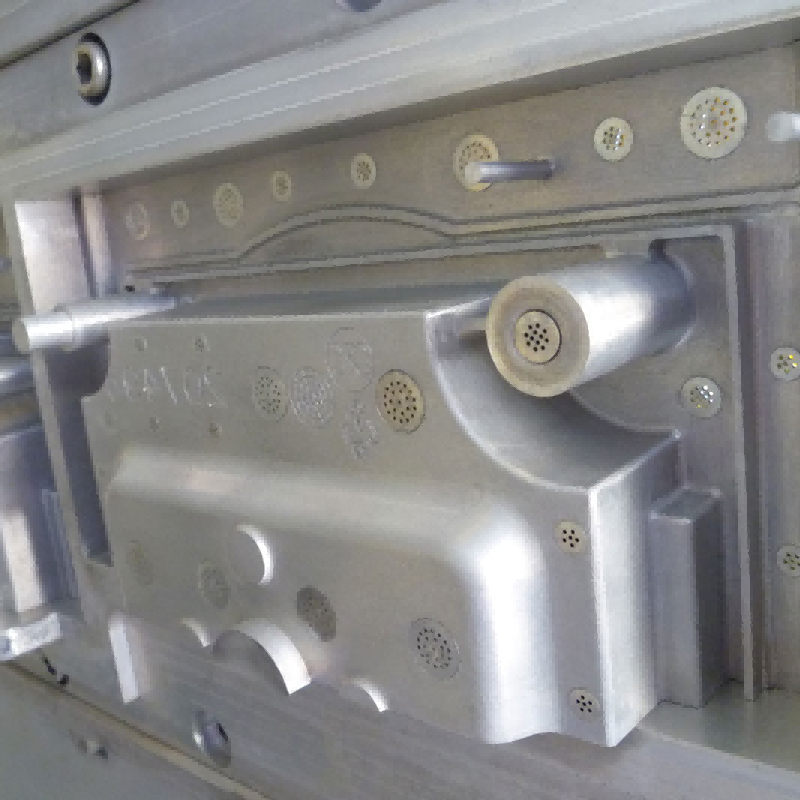
1.Temperature and Pressure Control
Precise control of temperature and pressure is of paramount importance in the production of EPS foam molds.
Temperature variations can significantly affect the foaming process and the final properties of the foam.
If the temperature is too low, the expansion of the EPS particles may be incomplete, resulting in a less dense and structurally weak foam.
On the other hand, if the temperature is too high, it can cause over-expansion, leading to an unstable foam structure with poor mechanical strength.
Pressure also plays a crucial role. Inadequate pressure can prevent the EPS particles from fully expanding and adhering to each other, while excessive pressure can cause excessive densification and loss of flexibility.
To ensure quality, it is essential to maintain the temperature and pressure within the specified narrow ranges throughout the production process.
This often requires advanced monitoring and control systems to make real-time adjustments and ensure consistency.
2.Material Proportioning
The correct proportioning of materials has a direct impact on the performance of the EPS foam mold.
The ratio of EPS particles to additives such as flame retardants and colorants needs to be carefully balanced.
An excessive amount of additives may compromise the mechanical properties of the foam, reducing its strength and durability.
Conversely, insufficient additives may fail to provide the desired functional properties, such as fire resistance or color consistency.
Moreover, the proportion of water can affect the foaming process and the final density of the foam.
Too much water can lead to excessive steam generation during foaming, causing voids and irregularities in the foam structure.
Insufficient water, on the other hand, can result in incomplete foaming and an uneven distribution of cells.
Therefore, precise material proportioning is crucial to achieving the desired performance characteristics of the EPS foam mold.
3.Mold Maintenance
Regular and proper mold maintenance is essential to ensure the longevity and consistent performance of EPS foam molds.
After each production cycle, the molds should be thoroughly cleaned to remove any residue or debris that could affect the next molding process.
This can be done using suitable cleaning agents and tools, taking care not to damage the mold surface.
Inspections should be conducted at regular intervals to identify any signs of wear, damage, or corrosion.
Minor issues should be addressed promptly to prevent them from escalating. Lubrication of moving parts is also important to reduce friction and ensure smooth operation.
The frequency of maintenance depends on factors such as the production volume, the complexity of the molds, and the nature of the materials being processed.
In high-volume production environments, more frequent maintenance may be necessary to prevent premature mold failure and maintain product quality.
Common Problems and Solutions
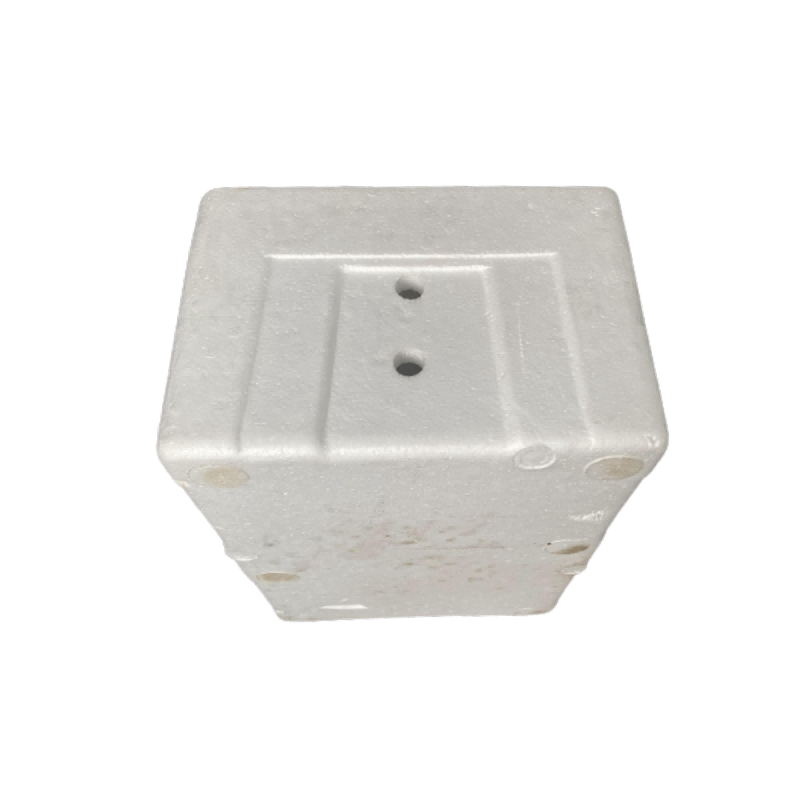
1.Surface Imperfections
Common surface problems in EPS foam molds include uneven texture, surface cracks, and blisters.
Uneven texture may occur due to inconsistent foaming or improper filling of the mold.
To address this, ensuring uniform pressure and temperature during the foaming process and optimizing the mold filling technique can help.
Surface cracks can result from rapid cooling or excessive stress during demolding.
Slowing down the cooling rate and using proper demolding techniques can reduce the occurrence of cracks.
Blisters often arise from trapped air or moisture. Thorough drying of raw materials and proper venting of the mold can prevent blisters.
2.Deformation Issues
Mold deformation can be caused by several factors.
Excessive heat during processing can cause the mold to lose its original shape.
To prevent this, strict control of processing temperatures is necessary.
Inadequate material strength or improper mold design can also lead to deformation.
Choosing high-quality EPS materials and designing molds with appropriate structural support can minimize the risk.
Additionally, improper storage or handling of the molds can cause distortion.
Storing molds in a controlled environment and handling them with care can prevent deformation.
3.Size Accuracy Problems
Factors affecting size accuracy of EPS foam molds include variations in raw material properties, inaccurate mold dimensions, and changes in processing conditions.
Inconsistent EPS particle size and density can result in variations in the final product size.
Using standardized and high-quality raw materials can improve size consistency.
Inaccurate mold dimensions can be rectified through precise manufacturing and regular calibration.
Fluctuations in temperature and pressure during processing can also affect size accuracy.
Maintaining stable processing conditions through advanced control systems is crucial for achieving accurate sizes.
Implementing quality control checks at various stages of production can help identify and rectify size accuracy problems promptly.