Expanded Polystyrene (EPS) is a versatile material that has become a staple in many industries due to its lightweight, insulating, and shock-absorbing properties. It is widely used in applications such as packaging, insulation, and even in the construction of various consumer goods. EPS molding equipment plays a crucial role in the manufacturing process of EPS products, enabling the efficient and effective transformation of raw polystyrene into usable forms.
What is EPS (Expanded Polystyrene) Molding
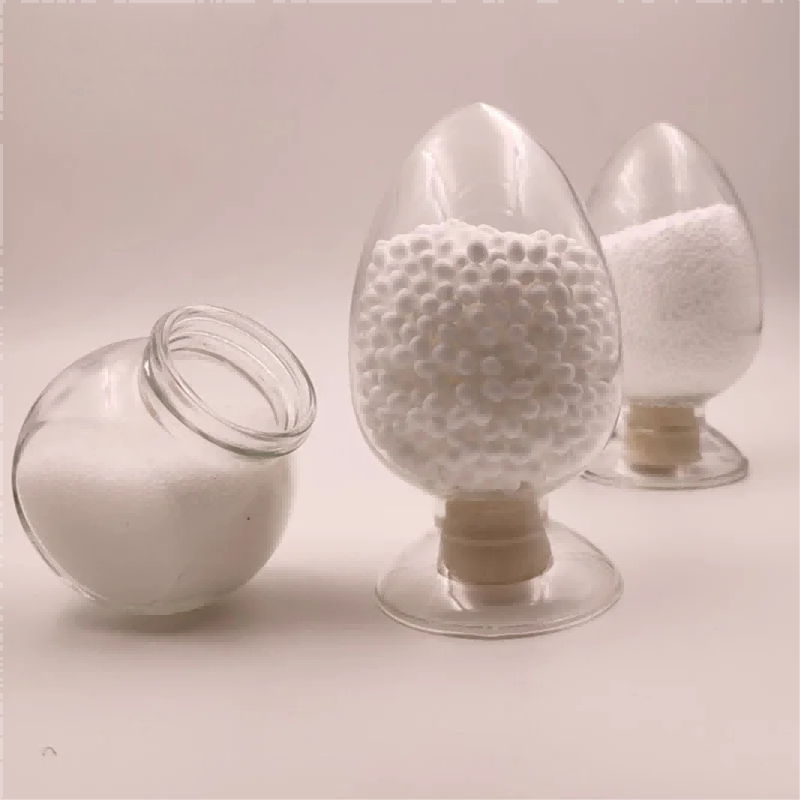
What is EPS?
EPS, or Expanded Polystyrene, is a foam material composed of small, air-filled beads that are fused together to form a solid material. EPS is created through the polymerization of styrene, followed by expansion and foaming. The result is a lightweight material with excellent insulation properties, shock resistance, and buoyancy. Because of these properties, EPS is widely used in packaging, food containers, insulation boards, and even in the automotive and construction industries.
Despite its versatility, EPS can be challenging to mold due to its sensitivity to heat and pressure. EPS molding equipment has been developed to address these challenges and to produce EPS products that meet the various needs of industries worldwide.
The EPS Molding Process
The EPS molding process involves several key stages that transform raw EPS beads into usable products. These stages require specialized equipment to ensure precision and efficiency in the production of high-quality EPS foam products.
1. Pre-Expansion
The first stage of the EPS molding process is pre-expansion, where raw polystyrene beads are heated and expanded. This is typically done in a machine called an EPS pre-expander, which heats the beads with steam, causing them to expand to several times their original size. During this process, the beads absorb the steam and expand into tiny foam particles. The pre-expanded beads are then cooled and dried.
- Purpose: To create foam beads of a uniform size that will later be molded into the final shape.
- Equipment Used: EPS pre-expanders, steam generators, cooling units.
2. Molding
After the beads are pre-expanded, they are ready to be molded into the desired shape. This is where EPS molding equipment comes into play. The pre-expanded beads are placed into a molding machine, where they are subjected to heat and pressure to fuse them together into the final product shape. The molding process typically takes place in a molding mold designed to accommodate the specific dimensions and characteristics of the product being produced.
- Purpose: To mold the pre-expanded beads into the desired shape, such as packaging materials, insulation panels, or molded components.
- Equipment Used: EPS molding machines, molds, heating plates, cooling systems.
3. Cooling and Ejection
Once the EPS foam has been molded into the desired shape, it needs to cool and solidify. The cooling process helps to ensure that the foam maintains its integrity and does not deform under stress. Cooling can be achieved through a combination of air and water cooling systems.
- Purpose: To solidify the molded product and prepare it for removal from the mold.
- Equipment Used: Cooling systems, air compressors, water chillers.
4. Cutting and Finishing
After the EPS foam has cooled, it is removed from the mold and undergoes finishing processes such as trimming, cutting, and surface treatment. This step ensures that the final product meets the required specifications and quality standards.
- Purpose: To remove excess foam, refine the edges, and shape the product into its final form.
- Equipment Used: Cutting machines, trimming equipment, surface treatment machines.
Types of EPS Molding Equipment
There are several types of EPS molding equipment, each designed to cater to different aspects of the EPS molding process. These include machines for pre-expansion, molding, cooling, and finishing. Below are some of the key types of EPS molding equipment:
1. EPS Pre-Expander
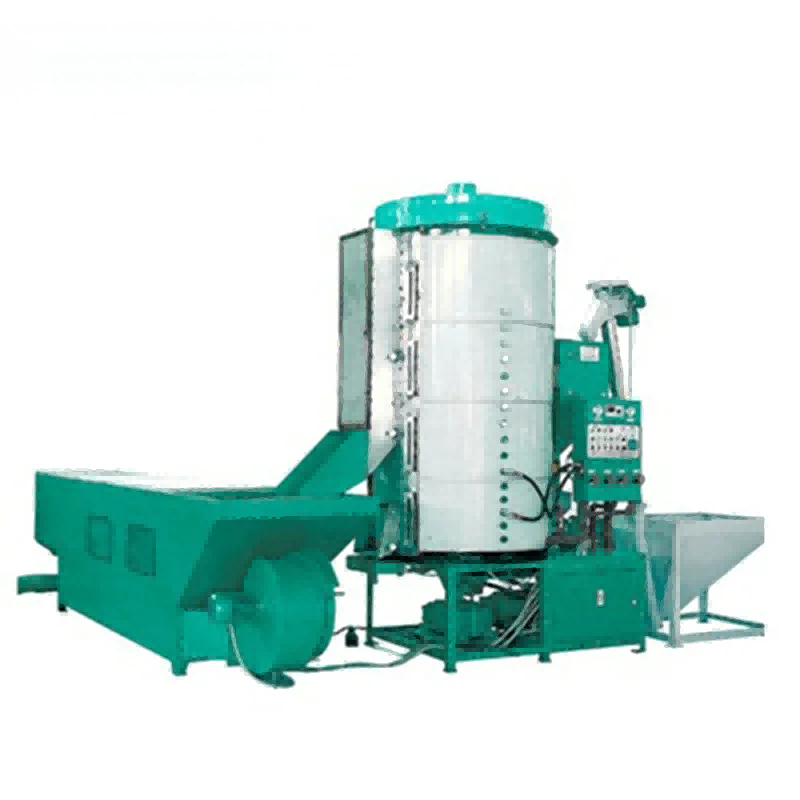
An EPS pre-expander is a machine used in the initial stage of the molding process. It expands raw polystyrene beads by introducing steam into the chamber. The pre-expansion process is critical for achieving uniform bead size and creating a consistent foam structure in the final product.
- Function: To expand raw EPS beads into foam particles.
- Features: Adjustable steam temperature, automatic control, and bead size regulation.
2. EPS Molding Machine
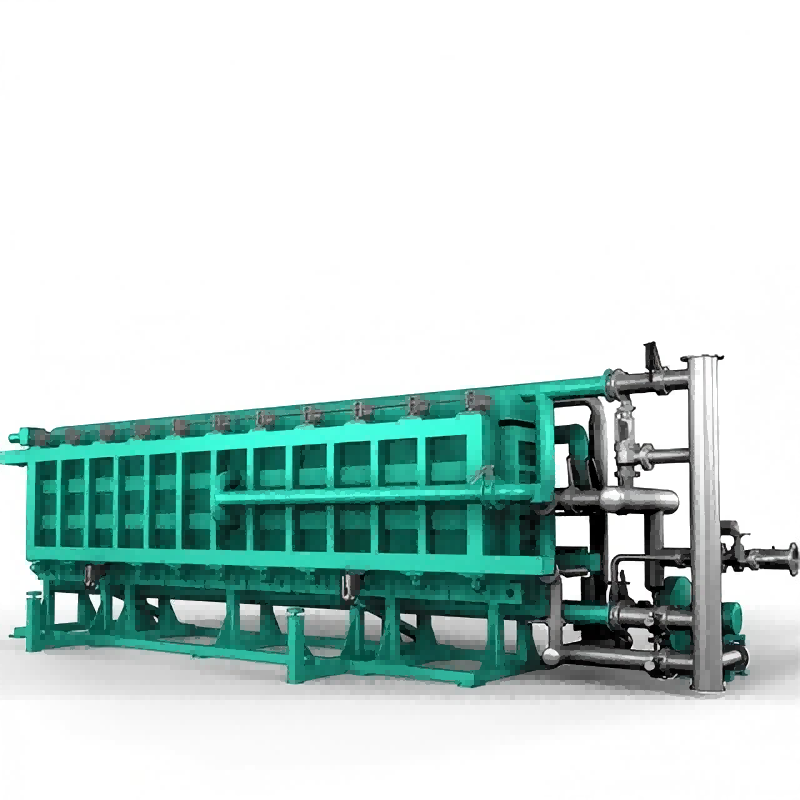
An EPS molding machine is used to mold the pre-expanded EPS beads into the final shape. These machines apply heat and pressure to fuse the beads together into the desired shape. There are different types of EPS molding machines depending on the shape and size of the product being produced.
- Function: To mold EPS foam into specific shapes.
- Types:
- Block Molding Machines: Used for large, rectangular blocks of EPS foam.
- Shape Molding Machines: Used for custom, complex shapes like packaging and automotive parts.
- Injection Molding Machines: Used for high-precision, small parts.
3. EPS Cooling System
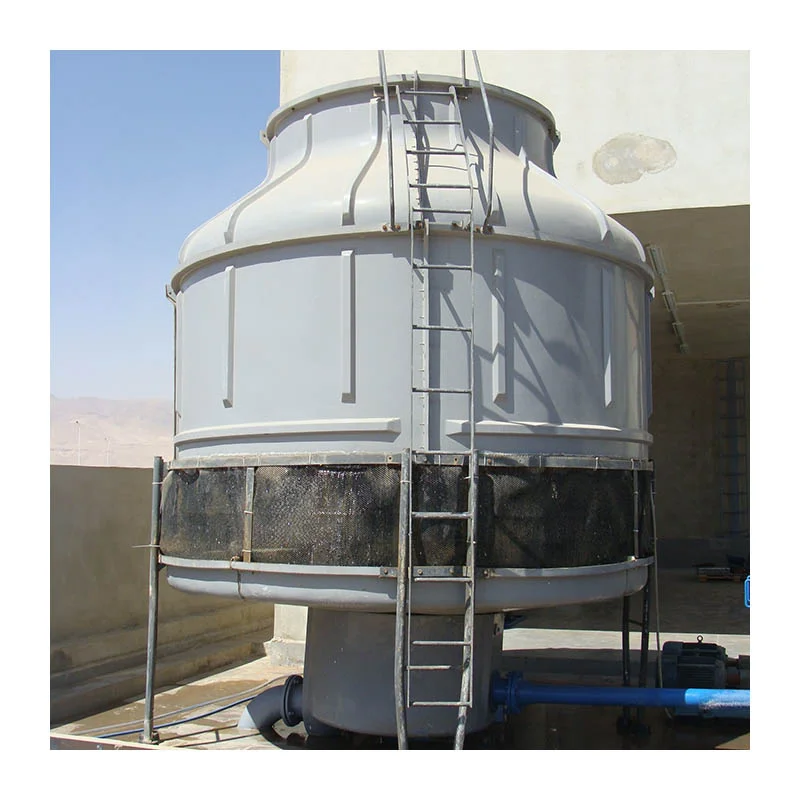
An EPS cooling system is used to cool the molded EPS foam after it has been shaped. Cooling is essential to ensure that the foam retains its shape and integrity. The cooling system usually consists of a combination of water and air cooling technologies.
- Function: To cool the molded foam and prevent deformation.
- Features: Adjustable cooling temperature, high-efficiency fans, and water chillers.
4. EPS Cutting Machine
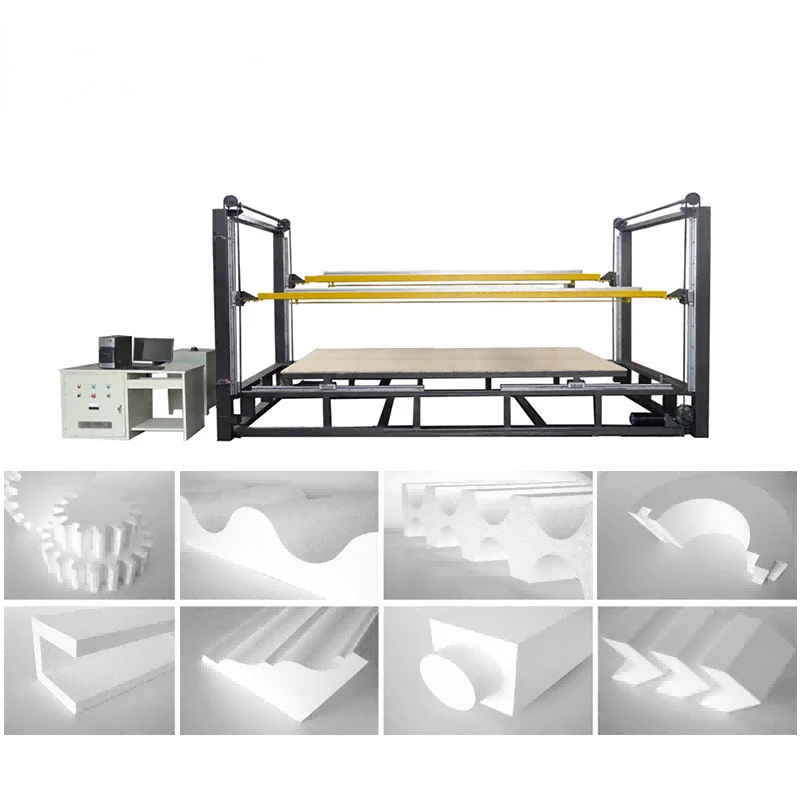
After the EPS foam has been molded and cooled, it often needs to be cut into specific shapes and sizes. EPS cutting machines are used to trim and shape the foam, remove excess material, and produce the final product.
- Function: To cut molded EPS foam into desired sizes and shapes.
- Types:
- Hot Wire Cutting Machines: Use heated wires to slice through EPS foam with precision.
- CNC Cutting Machines: Computer-controlled cutting systems for high-precision cuts.
5. EPS Surface Treatment Equipment
In some cases, the surface of the molded EPS product needs to be treated to improve its appearance or functionality. Surface treatment equipment can include systems for coating, polishing, or adding texture to the foam’s surface.
- Function: To enhance the surface quality of the molded EPS foam.
- Types: Coating machines, polishing machines, texture machines.
Applications of EPS Molding Equipment
EPS molding equipment is used in a wide range of industries to produce various products. Below are some of the primary applications of EPS molding:
1. Packaging Industry
EPS is widely used in the packaging industry due to its lightweight and protective qualities. EPS molding equipment is used to create custom packaging solutions for fragile items such as electronics, appliances, and food products.
- Applications: Protective packaging, custom inserts, and thermal insulation packaging.
2. Construction Industry
EPS is commonly used as an insulation material in the construction industry due to its excellent thermal properties. EPS molding equipment is used to create insulation panels, blocks, and custom shapes for building materials.
- Applications: Insulation panels, foundation blocks, roofing materials.
3. Automotive Industry
EPS foam is used in the automotive industry for lightweight components, cushioning, and insulation. EPS molding equipment is used to create custom shapes for various automotive parts such as seat cushions, headrests, and bumpers.
- Applications: Automotive seat foam, crash protection, sound insulation.
4. Food and Beverage Industry
EPS is often used for food packaging, particularly for disposable containers, trays, and cups. EPS molding equipment enables the creation of food-safe, molded products that meet industry standards.
- Applications: Disposable cups, food containers, trays.
5. Consumer Goods
EPS is used in the production of various consumer goods, including electronic packaging and protective cases for fragile items. EPS molding equipment allows manufacturers to create intricate designs and customized products for consumers.
- Applications: Electronics packaging, custom protective cases, insulation for appliances.
Benefits of EPS Molding Equipment
Using EPS molding equipment offers numerous advantages, including:
1. Cost Efficiency
EPS molding equipment helps reduce material waste and ensures the efficient use of raw materials, leading to cost savings. The automated nature of many molding machines also reduces labor costs and increases production speed.
2. Precision and Quality
EPS molding machines are designed to produce high-quality, consistent products with tight tolerances. This ensures that the final products meet the required standards and specifications.
3. Versatility
EPS molding equipment can be used to produce a wide variety of products, from large insulation blocks to small, intricate packaging components. This versatility makes EPS molding equipment suitable for various industries and applications.
4. Environmental Benefits
EPS is a recyclable material, and the use of EPS molding equipment helps reduce waste by enabling the recycling and reuse of EPS foam. This contributes to a more sustainable manufacturing process and reduces the environmental impact of EPS waste.
Conclusion
EPS molding equipment plays a pivotal role in transforming raw polystyrene into valuable products across multiple industries. The molding process itself is complex, requiring precise control of heat, pressure, and cooling. With advancements in technology, EPS molding equipment is becoming more efficient, versatile, and sustainable. As the demand for EPS products continues to rise, manufacturers must adapt to evolving trends and focus on enhancing efficiency, reducing waste, and adopting environmentally friendly practices.