Geofoam is a lightweight engineered fill material made from expanded polystyrene (EPS) or extruded polystyrene (XPS) foam that has revolutionized civil engineering and construction projects worldwide.
This ultra-light, high-strength material typically weighs less than 1% of traditional earth materials while providing exceptional compressive strength and insulation properties.
Originally developed in Norway in the 1970s, geofoam has become an essential solution for reducing settlement, stabilizing slopes, and insulating foundations in challenging construction environments.
Composition and Types of Geofoam
Expanded Polystyrene (EPS) Geofoam
Manufacturing Process:
- Raw polystyrene beads are expanded using steam
- Expanded beads are molded into large blocks (typically 4′ x 4′ x 8′)
- Blocks are cured and trimmed to precise dimensions
Key Properties:
- Density range: 0.7 to 2.85 lbs/ft³ (11 to 46 kg/m³)
- Compressive strength: 317 to 2,680 lbs/ft² (15 to 130 kPa)
- Closed-cell structure (98% air)
- R-value: ~3.6 to 4.4 per inch
Extruded Polystyrene (XPS) Geofoam
Manufacturing Process:
- Polystyrene resin melted with blowing agents
- Extruded through dies to form continuous boards
- Cut to required dimensions after cooling
Key Properties:
- Higher density than EPS (1.5 to 3.0 lbs/ft³)
- Greater compressive strength (15 to 100 psi)
- More moisture resistant
- Smoother surface texture
Comparison Table: EPS vs XPS Geofoam
Property | EPS Geofoam | XPS Geofoam |
---|---|---|
Manufacturing Method | Bead expansion | Continuous extrusion |
Cell Structure | Slightly open | Fully closed |
Water Absorption | 2-4% by volume | 0.3% by volume |
Compressive Strength | Lower range | Higher range |
Cost | $20-$50/yd³ | $40-$80/yd³ |
Common Applications | Embankments, lightweight fill | Below-grade insulation, roofing |
Engineering Properties and Specifications
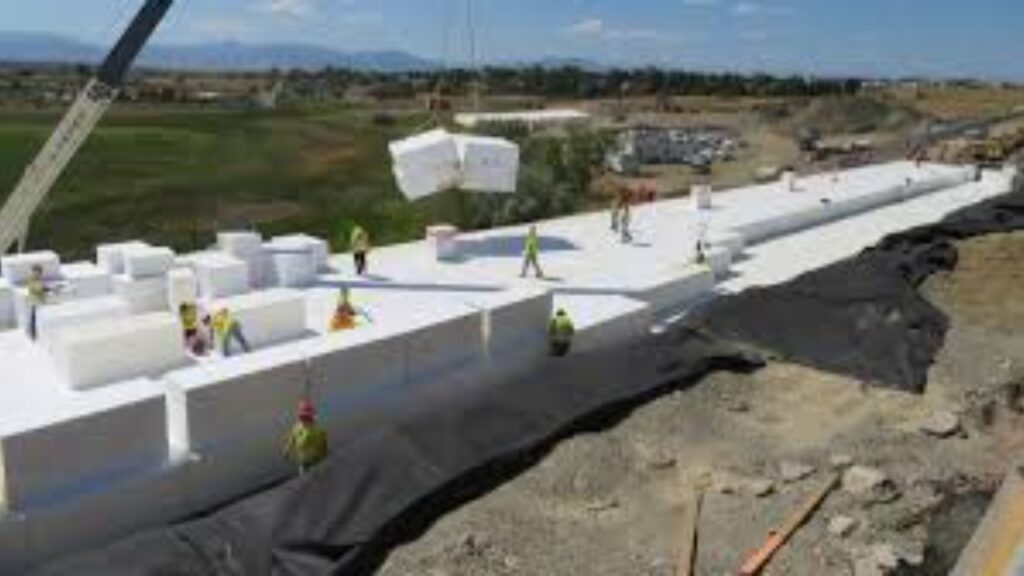
Physical Characteristics
Ultra-Light Weight:
- 1% the weight of soil (15-50 kg/m³ vs 1600-2000 kg/m³ for soil)
- Reduces dead load on underlying soils by up to 99%
Compressive Strength:
- ASTM D6817 standard classifications:
- Type I: 317 lbs/ft² (15 kPa)
- Type XV: 2,680 lbs/ft² (130 kPa)
- Strength increases with density
Deformation Properties:
- Elastic modulus: 2,000-10,000 kPa
- Creep deformation <1% per decade under proper loads
Geotechnical Advantages
Settlement Reduction:
- Eliminates consolidation settlement
- Immediate load-bearing capacity
Slope Stability:
- Reduces driving forces in fills
- 3:1 (H:V) maximum slope recommendation
Lateral Pressure:
- Generates only 1-2% of equivalent soil pressure
- Ideal for retaining wall backfill
Major Applications in Construction
Transportation Infrastructure
Roadway Construction:
- Lightweight embankments over soft soils
- Bridge approach fills to minimize settlement
- Railway track bed stabilization
Airport Projects:
- Runway extensions over compressible soils
- Taxiway embankments
- Apron area stabilization
Building Foundations
Below-Grade Applications:
- Lightweight fill for podium decks
- Parking garage ramp support
- Foundation insulation
Expansive Soil Solutions:
- Moisture barrier for clay soils
- Foundation cushioning
- Slab-on-grade support
Retaining Structures
Backfill Material:
- Reduces lateral earth pressure by 95%+
- Allows thinner retaining wall designs
- Ideal for seismic zones
Green Roof Systems:
- Lightweight growing medium support
- Provides drainage and insulation
Installation Guidelines and Best Practices
Site Preparation
Subgrade Requirements:
- Remove organic material
- Compact to 90% Standard Proctor
- Install separation geotextile (optional)
Moisture Protection:
- Avoid prolonged water exposure
- Use drainage layers when needed
- Seal joints in wet conditions
Block Placement
Layering Technique:
- Stagger vertical joints like brickwork
- Maximum lift height: 3-5 feet
- Use pins or adhesives for stability
Cover Systems:
- Minimum 12″ soil cover for protection
- Geogrid reinforcement for steep slopes
- Paving or armor stone for exposed applications
Special Considerations
Chemical Compatibility:
- Avoid petroleum-based solvents
- Resistant to most salts and mild acids
- Protect from UV exposure
Fire Safety:
- Use flame-retardant grades when needed
- Cover with non-combustible materials
- Follow local building codes
Cost Analysis and Value Engineering
Material Costs
EPS Geofoam Pricing:
- $20-$50 per cubic yard
- Density-dependent pricing
- Volume discounts available
XPS Geofoam Pricing:
- $40-$80 per cubic yard
- Higher performance premium
Installation Savings
Labor Efficiency:
- 10x faster than conventional fills
- No compaction required
- Minimal equipment needs
Project Acceleration:
- Immediate loading capability
- Weather-resistant installation
- Eliminates settlement waiting periods
Lifecycle Cost Benefits
Reduced Foundation Costs:
- Smaller footings
- Less deep soil improvement
- Lower seismic loads
Maintenance Savings:
- No consolidation settlement repairs
- Resistant to biological degradation
- Long-term performance stability
Environmental Considerations
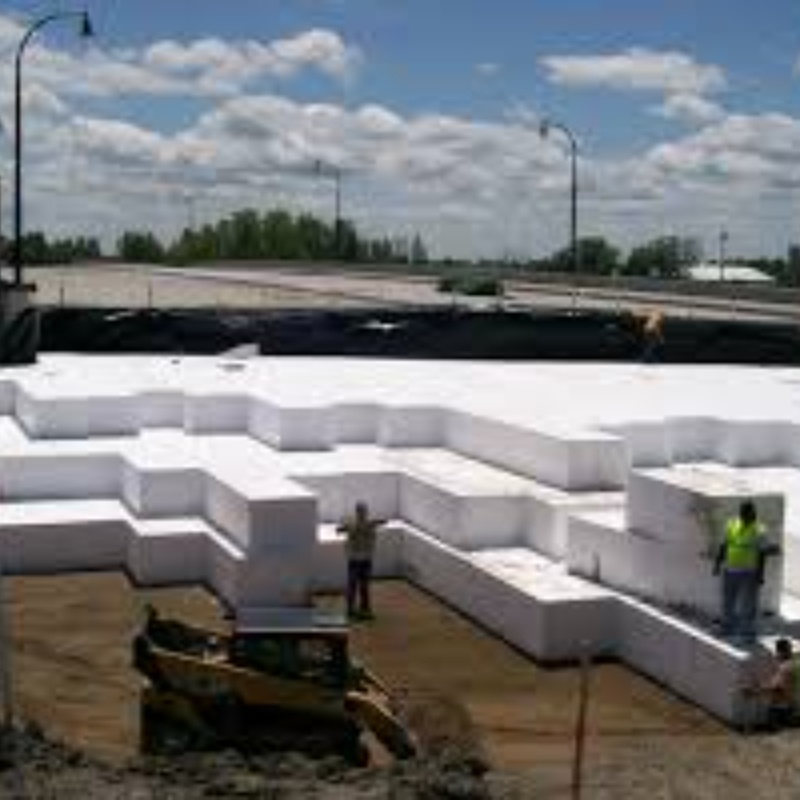
Sustainability Features
Material Composition:
- 98% air by volume
- No CFCs or HCFCs in modern production
- Recyclable at end-of-life
Carbon Footprint:
- Lower embodied energy than earthwork
- Reduced transportation emissions
- Less equipment fuel consumption
LEED Contribution Points
Potential credits include:
- Materials & Resources (recycled content)
- Energy & Atmosphere (insulation value)
- Innovation in Design (performance solutions)
How Much Does Geofoam Cost?
Current Geofoam Market Prices
Expanded Polystyrene (EPS) Geofoam Pricing
Standard Block Pricing (4′ x 4′ x 8′ blocks):
- Type I (15 psi): $25-$35 per cubic yard
- Type II (22 psi): $30-$40 per cubic yard
- Type VIII (40 psi): $45-$60 per cubic yard
- Type XV (100 psi): $70-$90 per cubic yard
Project-Scale Discounts:
- Small projects (<100 yd³): +15-25% premium
- Medium projects (100-1,000 yd³): Base rates
- Large projects (>1,000 yd³): 10-20% discount
Extruded Polystyrene (XPS) Geofoam Pricing
Higher-Density Options:
- Standard XPS (25 psi): $50-$70 per cubic yard
- High-Density XPS (40 psi): $70-$90 per cubic yard
- Premium XPS (100 psi): $100-$130 per cubic yard
Cost Factors Affecting Geofoam Prices
1. Material Specifications
- Density requirements (+$5/yd³ per 1 lb/ft³ increase)
- Compressive strength (Type XV costs 2-3x Type I)
- Special additives (flame retardants +15-25%)
2. Project Location
- Regional price variations:
- West Coast: +10-15%
- Midwest: Base rates
- Northeast: +5-10%
- South: -5% to base
- Transportation costs ($1.50-$3.00 per mile beyond 100 miles)
3. Order Volume
- Truckload quantities (20-25 yd³ per load) get best rates
- Seasonal demand (spring/summer +5-10%)
4. Custom Requirements
- Special sizes (non-standard blocks +20-40%)
- Pre-cut shapes (+$50-$150 per hour CNC cutting)
- Surface treatments (texturing, coatings +$5-$15/yd³)
Installation Costs Breakdown
Professional Installation Rates
- Basic placement: $5-$10 per cubic yard
- Complex installations: $15-$30 per cubic yard
- Retaining wall backfill: $20-$40 per cubic yard
Equipment Requirements
- Small projects: Manual handling (no added cost)
- Medium projects: Small forklift ($150-$300/day)
- Large projects: Lull or crane ($500-$1,200/day)
Site Preparation Costs
- Subgrade preparation: $2-$5 per square foot
- Geotextile layer: $0.25-$0.50 per square foot
- Drainage systems: $3-$8 per linear foot
Cost Comparison to Traditional Fill Materials
Material | Cost per yd³ | Weight (lbs/ft³) | Notes |
---|---|---|---|
EPS Geofoam | $25-$90 | 0.7-2.85 | Lightest option |
XPS Geofoam | $50-$130 | 1.5-3.0 | Higher strength |
Structural Fill | $15-$30 | 120-140 | Requires compaction |
Lightweight Aggregate | $40-$80 | 30-50 | Natural alternative |
Soil Cement | $30-$60 | 100-120 | Rigid but heavy |
Lifecycle Cost Advantages
Long-Term Savings Considerations
- Foundation Cost Reduction: 20-40% savings on substructures
- Accelerated Construction: 30-50% faster installation
- Zero Maintenance: No settlement repairs needed
- Durability: 50+ year service life expectancy
How to Make Geofoam
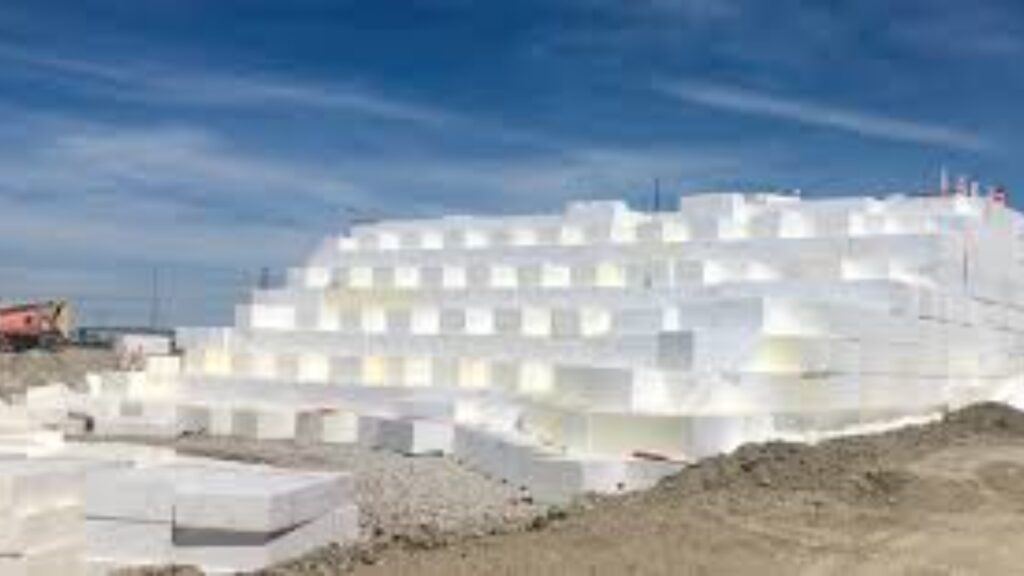
Raw Materials Needed
Material | Purpose |
---|---|
EPS raw beads (pentane-blown) | Base material |
Steam | Expansion agent |
Anti-static agent | Prevents bead clumping |
Flame retardants (optional) | For fire-rated geofoam |
Manufacturing Process Overview
- Pre-expand EPS beads to desired density
- Mold into large blocks
- Cure for 24-48 hours
- Cut to project specifications
- Test for quality compliance
Step 1: EPS Bead Pre-Expansion
Equipment: Pre-expander machine
Process:
- Load raw beads into expansion chamber
- Inject steam (212-220°F) for 2-5 minutes
- Beads expand 20-50x original size
- Adjust density (0.7-3.0 lb/ft³) by controlling steam/time
Step 2: Block Molding
Equipment: Hydraulic block molding machine
Process:
- Fill mold with pre-expanded beads
- Inject steam (230-250°F) to fuse beads
- Apply 15-30 psi pressure
- Cool with water spray
- Eject block (standard size: 36″x48″x96″)
Step 3: Curing & Stabilization
- Store blocks vertically for 24-48 hours
- Allows pentane gas to dissipate
- Stabilizes internal structure
Step 4: Cutting to Size
Methods:
- Hot wire cutting (for smooth edges)
- Band saws (for precision cuts)
- CNC routers (for complex shapes)
Common Sizes:
- Road construction: 24″x48″x96″
- Landscaping: Custom thicknesses
Step 5: Quality Testing
ASTM Standards:
- D6817 (Physical properties)
- D7180 (Compressive resistance)
- E84 (Flame spread rating)
Equipment Requirements
Equipment | Purpose | Cost Range |
---|---|---|
Pre-expander | Bead expansion | $50,000-$150,000 |
Block mold | Forming blocks | $100,000-$300,000 |
Steam boiler | Provides steam | $20,000-$80,000 |
Cutting system | Size customization | $15,000-$100,000 |
Safety Considerations
- Ventilation: Required for pentane gas
- Fire prevention: Install spark detectors
- PPE: Heat-resistant gloves, goggles
- Training: OSHA-compliant operation
Conclusion
Geofoam has established itself as an indispensable material in modern civil engineering, offering unparalleled advantages for lightweight filling, thermal insulation, and vibration damping.
Its unique combination of physical properties enables innovative solutions to traditional geotechnical challenges while providing cost-effective alternatives to conventional earthwork.
As material science advances and sustainability becomes increasingly important, geofoam continues to evolve, promising even broader applications in infrastructure development and building construction.