What Is Injection Molding
Injection molding is a high-precision manufacturing process used to produce plastic parts in massive volumes with exceptional consistency and accuracy.
This transformative technology melts plastic pellets and injects the molten material into custom-designed molds under high pressure, creating identical components ranging from tiny medical devices to large automotive parts.
As the dominant method for mass-producing plastic products, injection molding combines efficiency, versatility, and cost-effectiveness, making it indispensable to industries worldwide.
Materials Used in Injection Molding
Common Thermoplastics
Material | Properties | Common Uses |
---|---|---|
ABS | Tough, impact-resistant | Automotive parts, toys |
Polypropylene | Chemical-resistant, flexible | Packaging, living hinges |
Polycarbonate | Transparent, high-impact | Safety glasses, medical devices |
Nylon | Strong, wear-resistant | Gears, bearings |
Polyethylene | Lightweight, chemical-resistant | Bottles, containers |
Material Selection Factors
Mechanical Requirements:
- Strength
- Flexibility
- Impact resistance
Environmental Conditions:
- Temperature range
- UV exposure
- Chemical contact
Regulatory Compliance:
- Food-grade approval
- Medical certification
- Flame ratings
Aesthetic Needs:
- Transparency
- Color options
- Surface finish
Advantages of Injection Molding
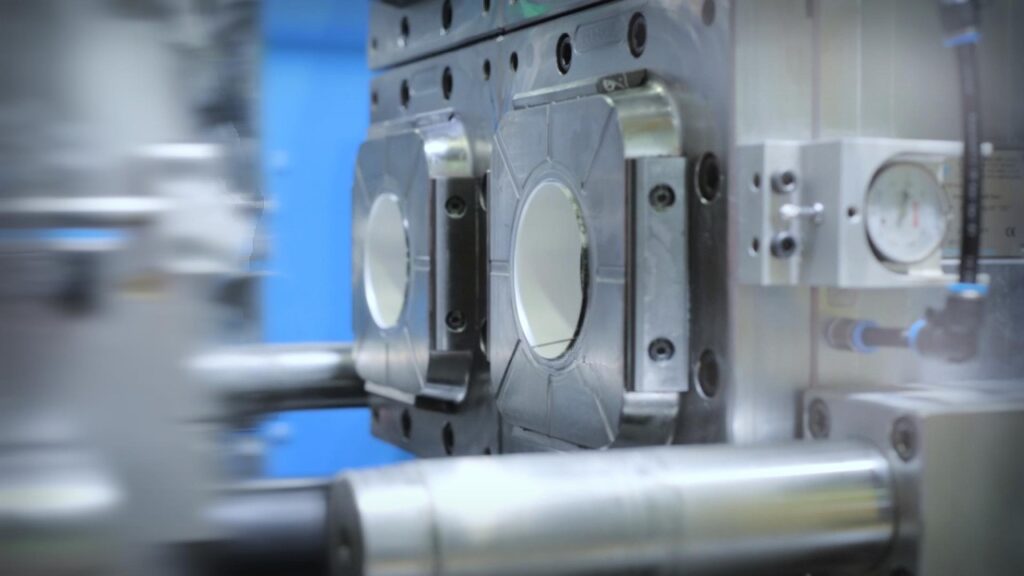
Production Benefits
High Efficiency:
- Fast cycle times (seconds to minutes)
- 24/7 operation capability
- Minimal post-processing
Precision and Consistency:
- Tight tolerances (±0.005 inches)
- Repeatable quality
- Complex geometries possible
Material Versatility:
- Hundreds of plastic options
- Color customization
- Additive incorporation (fillers, fibers)
Economic Advantages
Low Per-Unit Cost:
- Economies of scale
- Minimal material waste
- Automated production
Long Tool Life:
- Steel molds last millions of cycles
- Aluminum options for prototypes
- Durable construction
Reduced Labor Costs:
- Minimal operator involvement
- Automated part removal
- Integrated quality control
Injection Molding Process Variations
Specialized Techniques
Two-Shot Molding:
- Combines different materials/colors
- Enhanced product functionality
- Bonded substrates
Insert Molding:
- Encases metal/components in plastic
- Improved part integration
- Reduced assembly steps
Overmolding:
- Adds soft-touch surfaces
- Improves grip and ergonomics
- Multi-material construction
Advanced Technologies
Micro Molding:
- Extremely small parts
- Precision medical components
- Miniature electronics
Gas-Assisted Molding:
- Hollow sections for weight reduction
- Reduced sink marks
- Improved surface finish
Liquid Silicone Rubber (LSR) Molding:
- High-temperature elastomers
- Medical-grade materials
- Complex flexible parts
Injection Molding Tooling
Mold Design Fundamentals
Parting Line:
- Separation plane between mold halves
- Affects part ejection
- Influences flash potential
Draft Angles:
- 1-2° typically required
- Facilitates part release
- Reduces ejection force
Wall Thickness:
- Consistent sections ideal
- Typically 0.04-0.16 inches
- Affects cooling time and quality
Mold Components
Core and Cavity:
- Form the part shape
- Precision machined surfaces
- Heat-treated for durability
Runner System:
- Channels molten plastic to cavity
- Cold runners (standard)
- Hot runners (melt maintained)
Cooling Channels:
- Regulate mold temperature
- Optimize cycle time
- Prevent warpage
Ejection System:
- Pins, blades, or sleeves
- Removes finished part
- Prevents sticking
Quality Control in Injection Molding
Process Monitoring
Key Parameters:
- Melt temperature
- Injection pressure
- Cooling time
- Cycle time
Statistical Process Control (SPC):
- Real-time data collection
- Trend analysis
- Early problem detection
Part Inspection Methods
Dimensional Checks:
- CMM measurement
- Optical comparators
- Functional gauges
Visual Inspection:
- Surface defects
- Color consistency
- Flash examination
Performance Testing:
- Mechanical properties
- Fit and function
- Environmental testing
Common Defects and Solutions
Defect | Causes | Remedies |
---|---|---|
Sink Marks | Insufficient packing, thick sections | Increase pack pressure, modify design |
Warpage | Uneven cooling | Optimize cooling channels, adjust temps |
Short Shots | Incomplete filling | Increase melt temp, enlarge gates |
Flash | Excessive clamp force | Improve mold maintenance, reduce injection pressure |
Cost Factors in Injection Molding
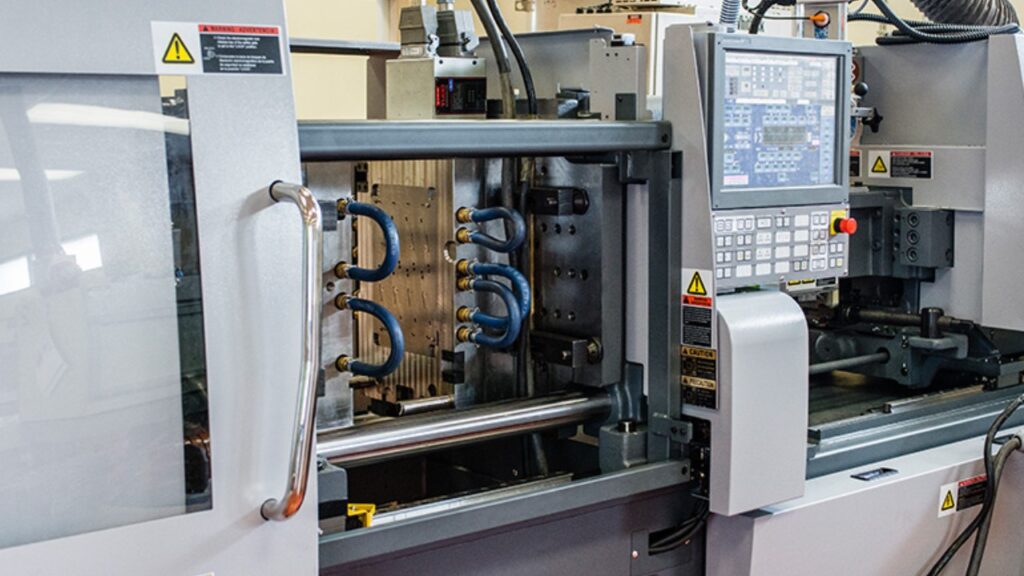
Primary Cost Drivers
Tooling Investment:
- Mold design complexity
- Cavity quantity
- Material (aluminum vs. steel)
Material Costs:
- Plastic resin type
- Part volume/weight
- Regrind percentage
Production Volume:
- Economies of scale
- Machine time allocation
- Labor requirements
Cost Reduction Strategies
Design Optimization:
- Minimize wall thickness
- Standardize features
- Eliminate unnecessary complexity
Material Selection:
- Appropriate grade selection
- Recycled content options
- Alternative resins
Process Efficiency:
- Cycle time reduction
- Energy-saving measures
- Preventive maintenance
How Does Injection Molding Work?
Injection molding is a sophisticated manufacturing process that produces identical plastic parts with high precision and efficiency.
This transformative technology melts plastic pellets and injects the molten material into custom-designed molds under intense pressure, creating everything from tiny medical components to large automotive parts.
The Core Components of an Injection Molding Machine
Injection Unit: Melting and Delivering Plastic
Hopper:
- Stores and feeds raw plastic pellets
- May include drying systems for hygroscopic materials
- Gravity-fed or vacuum-assisted designs
Barrel and Screw:
- Heated barrel contains a reciprocating screw
- Screw rotation melts and mixes the plastic
- Typical length-to-diameter ratio of 20:1
- Multiple heating zones with precise temperature control
Nozzle:
- Connects barrel to mold
- Maintains melt temperature
- Special designs for different applications
Clamping Unit: Mold Handling System
Stationary Platen:
- Fixed half of the mold mounting
- Contains sprue bushing for material entry
Moving Platen:
- Holds the ejector half of the mold
- Travels on tie bars during operation
Clamping Mechanism:
- Hydraulic, mechanical, or electric systems
- Generates tons of force to keep mold closed
- Modern machines reach 6,000+ tons clamping force
Mold: The Precision Tooling
Cavity and Core:
- Negative impression of the part
- Hardened steel or aluminum construction
- Mirror-finish or textured surfaces
Runner System:
- Channels for plastic flow
- Cold runners (solidify and get trimmed)
- Hot runners (maintain molten state)
Cooling Channels:
- Circulate temperature-controlled water
- Critical for cycle time and part quality
- Complex conformal designs in advanced molds
The Injection Molding Cycle: Step-by-Step
Stage 1: Clamping
Mold Closing:
- Hydraulic or electric motor drives platen
- Mold halves meet at parting line
- High clamping force applied (tons per square inch)
Verification:
- Sensors confirm proper closure
- Safety checks complete
- Injection sequence initiates
Stage 2: Injection
Screw Forward Movement:
- Hydraulic pressure or electric servo drives screw
- Acts as plunger to inject molten plastic
- Precise speed and position control
Fill Phase:
- Plastic flows through sprue, runners, gates
- Fills mold cavity in milliseconds
- Packing pressure follows to compensate for shrinkage
Velocity-to-Pressure Transition:
- Switch from speed control to pressure control
- Precisely timed for optimal part quality
- Prevents overpacking or underfilling
Stage 3: Cooling
Heat Transfer:
- Plastic solidifies against cooled mold walls
- Cooling time typically 50-80% of total cycle
- Conformal cooling channels optimize process
Continued Packing:
- Additional material forced in as plastic shrinks
- Maintains dimensional accuracy
- Prevents sink marks and voids
Gate Freeze-off:
- Material at gate solidifies
- Isolates part from runner system
- Allows safe mold opening
Stage 4: Ejection
Mold Opening:
- Moving platen retracts
- Part remains on ejector half
- Gradual acceleration/deceleration
Ejector System Activation:
- Pins, blades, or sleeves push part out
- Stripper plates for delicate parts
- Air blast or robot may assist
Part Removal:
- Manual handling for prototypes
- Robots for automated production
- Conveyors to next processing step
Stage 5: Reset and Repeat
Mold Closing:
- Ready for next injection
- Simultaneous plasticizing occurs
- Cycle time optimization critical
Screw Recovery:
- Screw rotates while retracting
- Next shot of material prepared
- Melt quality maintained
Continuous Cycling:
- Typical cycles from 10-60 seconds
- 24/7 operation possible
- Process monitoring ensures consistency
Material Behavior During Injection Molding
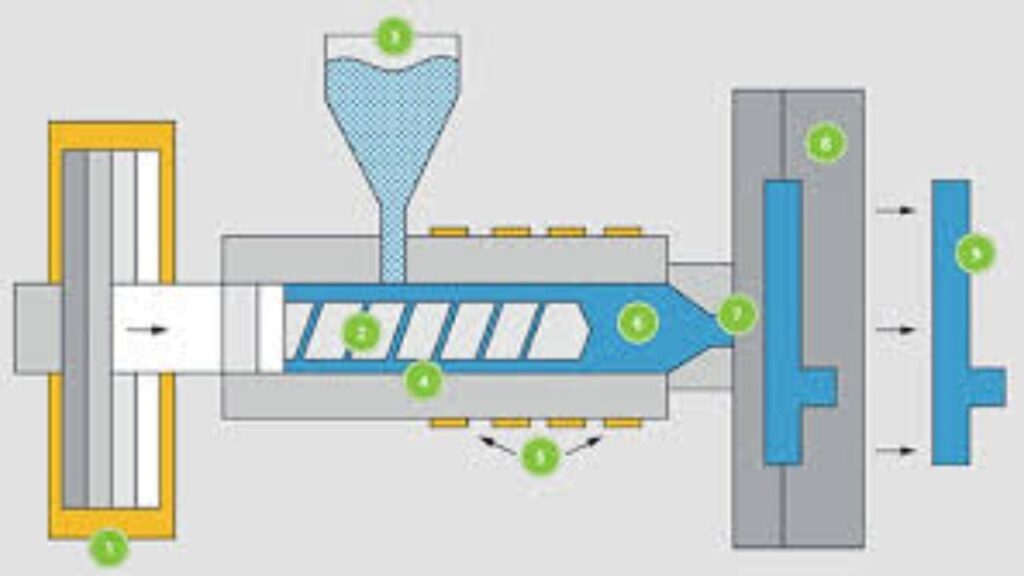
Plastic Melting Phase
Pellet Transition:
- Solid pellets → molten plastic
- Gradual heating through barrel zones
- Shear heating from screw rotation
Viscosity Changes:
- Non-Newtonian fluid behavior
- Shear thinning effect
- Temperature dependence
Material Homogenization:
- Mixing by screw flights
- Colorant dispersion
- Additive distribution
Flow Dynamics in the Mold
Fountain Flow Effect:
- Melt front advancement pattern
- Outer layers freeze first
- Core remains molten longer
Weld Lines:
- Where flow fronts meet
- Potential weak points
- Design and process solutions
Orientation Effects:
- Polymer chain alignment
- Anisotropic properties
- Affects part strength
Process Control and Optimization
Key Parameters
Temperature Control:
- Barrel zones (rear to front)
- Nozzle temperature
- Mold temperature (cooling channels)
Pressure Profiles:
- Injection pressure (10,000-30,000 psi)
- Pack/hold pressure
- Back pressure (screw recovery)
Speed Settings:
- Injection velocity
- Screw rotation speed
- Ejection speed
Monitoring Systems
Real-Time Sensors:
- Melt temperature
- Cavity pressure
- Mold temperature
Process Visualization:
- Fill pattern simulation
- Pressure curve analysis
- Defect prediction
Closed-Loop Control:
- Automatic adjustments
- Quality assurance
- Consistency maintenance
Advanced Injection Molding Techniques
Multi-Component Molding
Two-Shot Molding:
- Sequential injection of different materials
- Bonded substrates
- Color combinations
Overmolding:
- Adds soft-touch surfaces
- Improves grip/ergonomics
- Multi-material benefits
Insert Molding:
- Metal/electronic components encapsulated
- Reduced assembly
- Enhanced functionality
Specialized Processes
Micro Molding:
- Extremely small parts (mg weight)
- Precision medical devices
- Miniature connectors
Gas-Assisted Molding:
- Internal gas channels
- Reduced weight/sink marks
- Hollow sections
Liquid Silicone Rubber (LSR) Molding:
- Cold runner systems
- Platinum-cured materials
- Medical/consumer applications
Quality Assurance in Injection Molding
Common Defects and Solutions
Defect Type | Causes | Corrective Actions |
---|---|---|
Sink Marks | Insufficient packing, thick sections | Increase pack pressure/time, modify wall thickness |
Flash | Excessive injection pressure, worn mold | Reduce pressure, repair mold, increase clamp force |
Short Shots | Inadequate material, low temperature | Increase shot size, raise melt/mold temp |
Warpage | Uneven cooling, internal stresses | Optimize cooling, adjust packing, modify design |
Inspection Methods
Dimensional Checks:
- Coordinate Measuring Machines (CMM)
- Optical comparators
- Functional gauges
Visual Inspection:
- Surface defects
- Color consistency
- Ejector pin marks
Performance Testing:
- Mechanical properties
- Fit and function
- Environmental resistance
Applications Across Industries
Automotive Components
Interior Parts:
- Dashboard panels
- Control knobs
- Trim pieces
Underhood Applications:
- Fluid reservoirs
- Air intake components
- Electrical connectors
Exterior Features:
- Bumper systems
- Light housings
- Wheel arch liners
Medical Devices
Disposable Products:
- Syringes
- IV connectors
- Surgical instruments
Equipment Housings:
- Monitor casings
- Device enclosures
- Handheld tools
Implants and Prosthetics:
- Custom components
- Dental applications
- Surgical guides
Consumer Products
Electronics:
- Phone/tablet cases
- Computer housings
- Connector components
Household Goods:
- Storage containers
- Kitchen utensils
- Appliance parts
Toys and Recreation:
- Building blocks
- Sporting equipment
- Outdoor furniture
How Much Does Injection Molding Cost?
Injection molding costs vary dramatically based on part complexity, materials, production volume, and geographic location.
While this manufacturing process offers exceptional per-part economies at scale, the initial investments can be substantial.
Key Cost Components of Injection Molding
1. Mold/Tooling Costs (The Biggest Upfront Expense)
Mold Base Price Factors:
- Size: $1,000-$100,000+
- Small molds (<6″): $1,000-$5,000
- Medium molds (6-18″): $5,000-$20,000
- Large molds (>18″): $20,000-$100,000+
- Material:
- Aluminum molds: $1,500-$10,000 (softer, 10k-100k cycles)
- P20 steel molds: $5,000-$30,000 (100k-1M cycles)
- H13 hardened steel: $10,000-$100,000+ (1M+ cycles)
- Complexity:
- Simple 2-plate mold: Base price
- 3-plate mold: +20-40%
- Side-actions/core pulls: +$1,500-$5,000 per feature
- Micro-molding precision: +30-100%
Additional Tooling Expenses:
- Hot runner systems: $5,000-$50,000 (vs. cold runners)
- Surface finishes: $500-$5,000 (texturing, polishing)
- Mold flow analysis: $1,000-$3,000 (simulation software)
- Maintenance: 5-15% of mold cost annually
2. Part Production Costs (Per-Unit Pricing)
Material Costs:
- Commodity plastics: $0.50-$2.50/lb
- Polypropylene (PP): $0.70-$1.20/lb
- ABS: $1.00-$1.80/lb
- Polyethylene (PE): $0.60-$1.50/lb
- Engineering grades: $2.00-$10.00/lb
- Polycarbonate (PC): $2.20-$3.50/lb
- Nylon (PA6): $2.50-$4.00/lb
- PEEK: $40-$100/lb
- Material waste: 5-30% (sprue, runners, rejects)
Machine Time Rates:
- Hourly press costs: $30-$150/hour
- Small tonnage (<100T): $30-$60/hr
- Medium (100-500T): $60-$100/hr
- Large (>500T): $100-$150/hr
- Cycle time impact:
- Simple parts: 15-30 seconds
- Complex parts: 1-5 minutes
- Micro-molding: <10 seconds
3. Secondary Operations (Post-Processing)
Common Add-On Costs:
- Assembly: $0.10-$5.00/part
- Decoration:
- Pad printing: $0.10-$0.50/part
- Laser etching: $0.20-$1.00/part
- Painting: $0.50-$5.00/part
- Special finishes:
- EMI/RFI shielding: $1.00-$10.00/part
- Ultrasonic welding: $0.50-$3.00/part
Conclusion
Injection molding works through a meticulously engineered sequence of material preparation, high-pressure injection, controlled cooling, and precise ejection.
This cyclic process transforms raw plastic pellets into finished parts with remarkable efficiency and consistency.
The technology’s versatility stems from its ability to accommodate countless material formulations while producing complex geometries with tight tolerances.
Injection molding stands as the backbone of modern plastic manufacturing, offering unparalleled capabilities for mass-producing precision parts with remarkable efficiency.
From its ability to create intricate geometries to its cost-effectiveness at scale, this technology continues to evolve while maintaining its fundamental advantages.
As materials science advances and digital transformation reshapes manufacturing, injection molding adapts to meet new challenges in sustainability, performance, and smart production.