Structural foam molding is an advanced and versatile manufacturing process that combines the benefits of traditional injection molding with the advantages of foam technology.
It is widely used to create lightweight yet durable parts and components for various industries, including automotive, aerospace, consumer goods, and more.
This process results in products that are stronger, more rigid, and lighter than solid plastic parts, making it ideal for applications where weight reduction and material efficiency are critical.
What is Structural Foam Molding
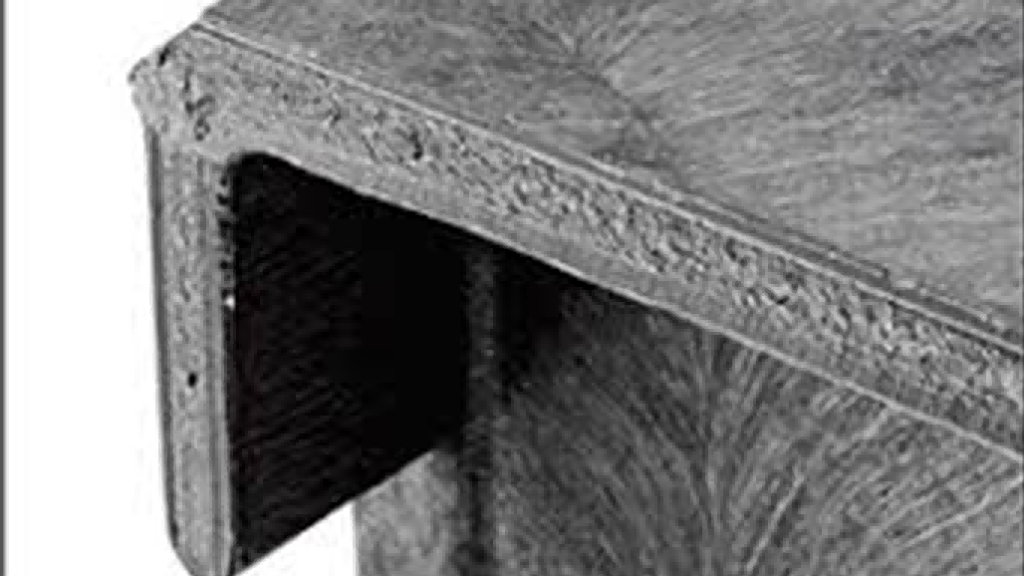
Structural foam molding (SFM) is a process that involves injecting a plastic material that contains a gas or foaming agent into a mold to create lightweight, thick-walled, and structurally strong parts.
The foaming agent is typically added to the resin before it is injected into the mold, resulting in a product that has a foam core with a solid outer surface.
The key advantage of structural foam molding over traditional injection molding is its ability to produce large, complex parts with reduced weight and improved mechanical properties.
The process is highly efficient and allows manufacturers to produce large parts in a single shot, reducing the need for additional steps like reinforcement or assembly.
The Role of Foam in Structural Foam Molding
The foam used in structural foam molding can be either a chemical foaming agent or a physical blowing agent.
When injected into the resin, these agents create gas bubbles within the material, causing it to expand and form a foamy structure.
The outer skin of the part remains solid, providing strength and durability, while the inner foam core offers lightweight and cost-effective benefits.
The Process of Structural Foam Molding
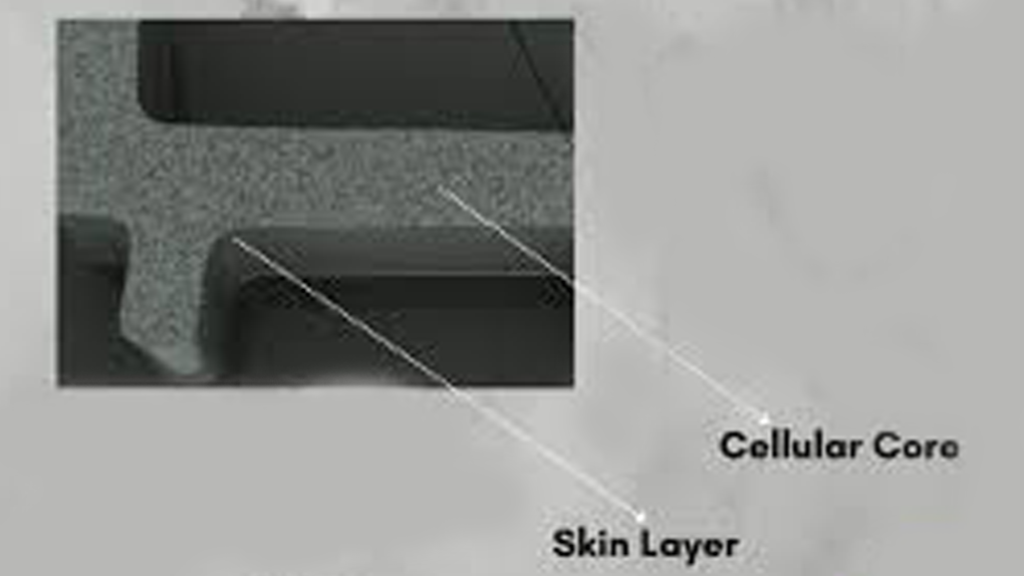
Step 1: Material Selection and Preparation
The first step in structural foam molding is the selection of the materials to be used.
Structural foam molding typically uses thermoplastic resins like ABS (Acrylonitrile Butadiene Styrene), polypropylene (PP), high-density polyethylene (HDPE), and polycarbonate (PC).
The resin is mixed with a foaming agent, which can be either a chemical blowing agent or a physical blowing agent.
- Chemical Blowing Agents: These agents release gas when heated, causing the resin to expand. Common chemical blowing agents include azodicarbonamide and sodium bicarbonate.
- Physical Blowing Agents: These agents are typically gases like nitrogen or carbon dioxide, which are injected into the resin to create bubbles when pressure is applied.
Once the material is selected and the foaming agent is mixed, the resin mixture is loaded into an injection molding machine.
The material’s temperature, pressure, and viscosity are carefully controlled to ensure that the foam core forms correctly while maintaining the integrity of the outer skin.
Step 2: Injection into the Mold
The prepared material is injected into the mold cavity using high pressure.
As the material flows into the mold, the foaming agent starts to react, causing the material to expand and create a foam structure.
This process takes place inside a closed mold, and the mold cavity is designed to shape the part according to the required specifications.
The injection process is crucial because it determines the distribution of the foam within the part.
The outer skin of the part remains solid, while the inner core becomes foamy and lightweight.
This structure enhances the part’s strength-to-weight ratio, making it ideal for applications where reduced weight is essential without sacrificing strength.
Step 3: Cooling and Solidification
Once the resin has been injected and the foam has formed, the part must cool down and solidify.
The mold is maintained at a specific temperature to allow the material to cure properly.
The cooling phase is essential to ensure that the foam has the right structure and that the part retains its shape after the injection process.
The cooling process also plays a role in the final mechanical properties of the part.
The thickness and density of the foam core can be controlled by adjusting the temperature and cooling time.
Parts that require higher strength or rigidity may need longer cooling times, while those that require a more flexible structure may cool faster.
Step 4: Demolding
After the part has cooled and solidified, the mold is opened, and the finished part is removed.
At this stage, the structural foam part is typically ready for further post-processing steps, such as trimming, surface finishing, or painting, depending on the requirements of the application.
The demolding process is critical to ensure that the part is removed from the mold without damage.
The mold design plays a significant role in this step, as it needs to allow for easy removal of the part while maintaining its structural integrity.
Advantages of Structural Foam Molding
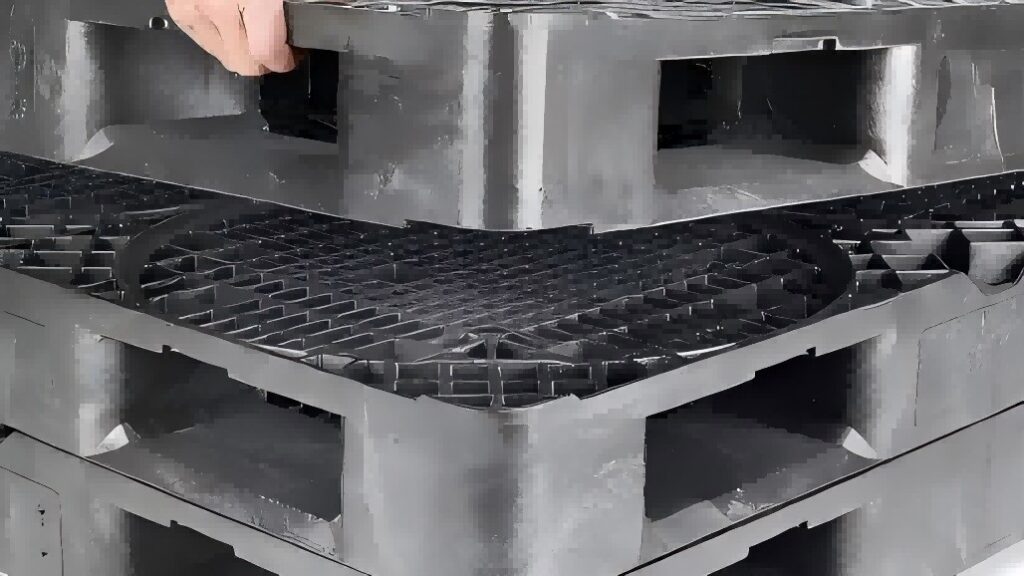
Structural foam molding offers several benefits that make it a preferred choice for many manufacturers.
These advantages make it especially appealing for industries that require lightweight, durable parts with complex geometries.
1. Lightweight and Strong Parts
One of the primary benefits of structural foam molding is its ability to create lightweight parts without compromising strength.
The foam core structure significantly reduces the part’s weight while maintaining its rigidity and strength.
This makes it an ideal choice for industries like automotive, aerospace, and packaging, where weight reduction is a critical factor.
2. Cost Efficiency
Structural foam molding is highly cost-effective due to its ability to produce large, complex parts in a single shot.
Traditional molding methods often require additional steps like reinforcement or assembly, which can add time and cost to the production process.
3. Design Flexibility
Structural foam molding offers excellent design flexibility.
The process can produce parts with varying wall thicknesses, intricate internal structures, and a smooth finish, making it suitable for a wide range of applications.
4. Improved Thermal Insulation
Because of the foam core, structural foam parts often exhibit excellent thermal insulation properties.
This makes them ideal for applications where temperature control is critical, such as in refrigeration, HVAC systems, and automotive parts.
5. High Structural Integrity
Despite being lightweight, structural foam parts retain high strength and durability due to the solid outer skin and the foamed core.
This combination of properties makes them suitable for use in demanding applications that require both strength and weight reduction.
6. Reduced Material Usage
Because the foam core is lightweight, structural foam molding requires less material to create parts compared to traditional solid plastic molding. This not only reduces material costs but also minimizes the environmental impact of production by using fewer resources.
Applications of Structural Foam Molding
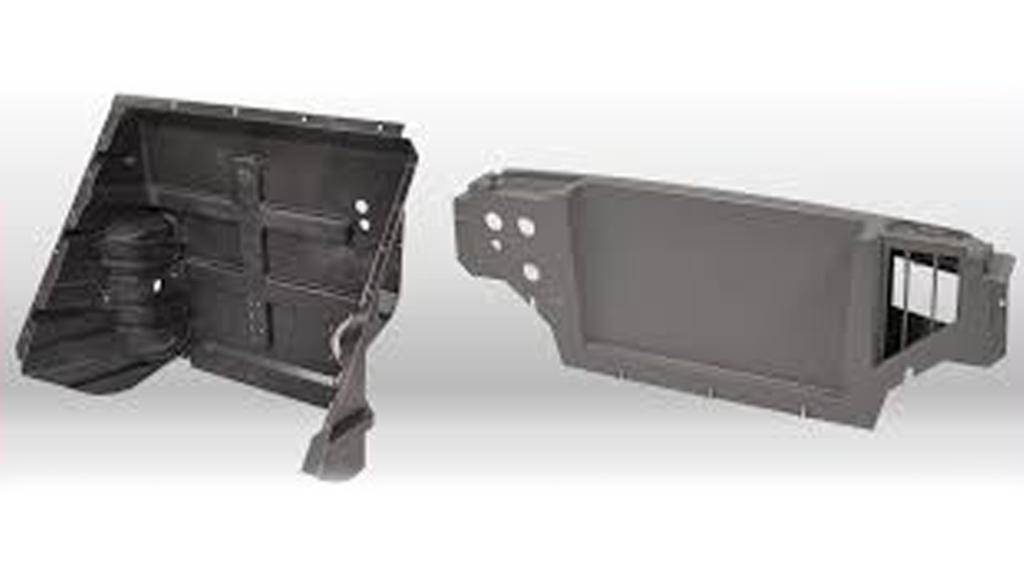
Structural foam molding is used in a wide range of industries and applications.
1. Automotive Industry
In the automotive industry, structural foam molding is used to produce lightweight, durable parts such as bumpers, door panels, dashboards, and under-hood components.
The process is ideal for creating parts with complex shapes that need to meet strict weight and performance requirements.
The foam core reduces the weight of the part, while the solid outer skin provides the necessary strength and durability.
2. Aerospace Industry
The aerospace industry uses structural foam molding to create lightweight yet strong components for aircraft.
Parts such as interior panels, bulkheads, and seat structures benefit from the foam core’s ability to reduce weight while maintaining the strength required to withstand the rigors of flight.
3. Consumer Goods
Structural foam molding is widely used to produce components for consumer goods, such as appliance housings, tool cases, and packaging.
The process allows manufacturers to create durable, lightweight products that are easy to handle and transport, while also reducing production costs.
4. Industrial Equipment
In industrial applications, structural foam molding is used to produce parts like machine housings, frames, and enclosures.
These parts need to be strong and durable, and the foam core provides the necessary strength without adding excessive weight.
5. Packaging Industry
Structural foam molding is used to produce protective packaging materials for fragile products.
The lightweight nature of structural foam makes it an ideal material for shipping and protecting sensitive items like electronics, glassware, and automotive parts.
Conclusion
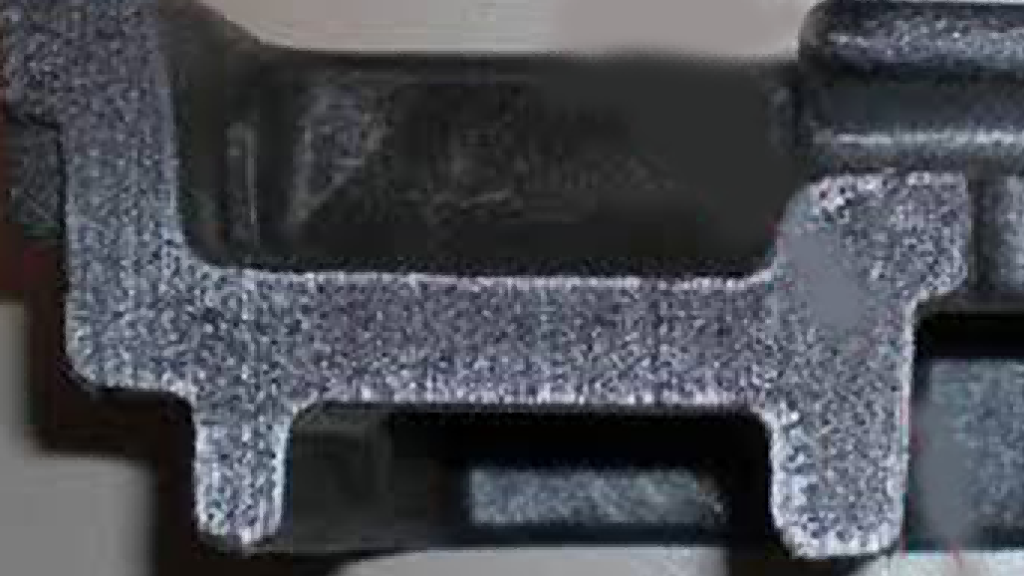
Structural foam molding is a powerful and versatile manufacturing process that provides manufacturers with the ability to create lightweight, durable, and cost-effective parts for a wide range of industries.
The combination of reduced weight, improved strength, and design flexibility makes it a preferred choice for automotive, aerospace, packaging, and consumer goods applications.