What is Stucco Foam Molding
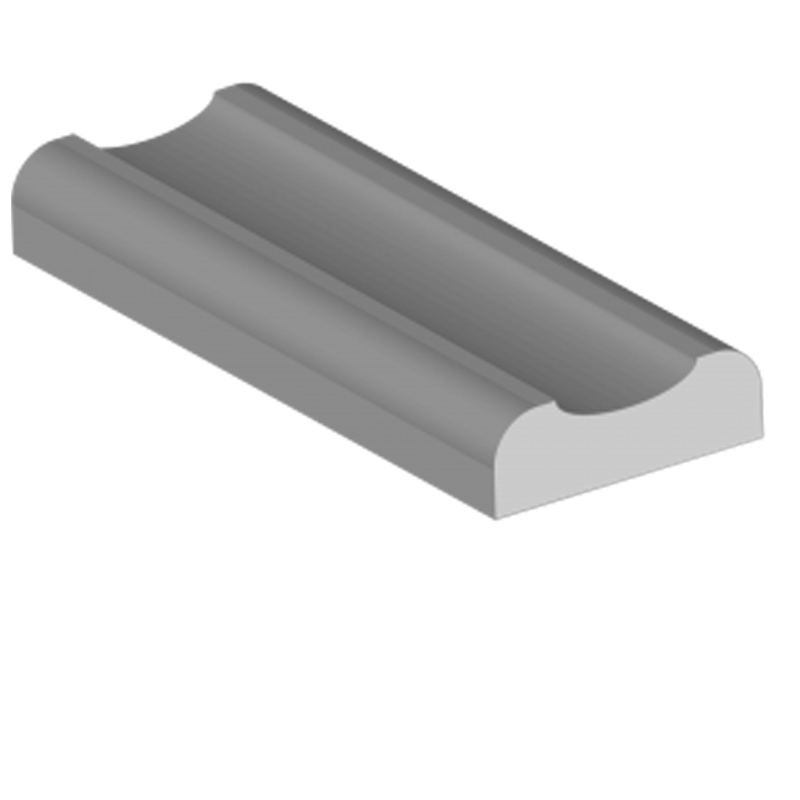
Stucco foam molding is a unique form of plastic molding that offers several distinct advantages.
The material used in stucco foam molding is typically a combination of polymers and additives that give it specific characteristics.
One of the key material characteristics is its lightweight nature.
This makes it easy to handle and install, reducing labor costs and time.
Additionally, it has excellent insulation properties.
This can help in reducing energy consumption by providing thermal insulation.
The material is also highly durable. It is resistant to moisture, rot, and insect damage.
This makes it suitable for a wide range of applications both indoors and outdoors.
In terms of application areas, stucco foam molding is commonly used in architectural design.
It can be used to create decorative elements such as cornices, columns, and arches.
These add aesthetic appeal to buildings and can mimic the look of traditional stucco while offering the advantages of foam.
It is also used in renovation projects. Due to its lightweight nature, it can be easily added to existing structures without adding significant weight.
This makes it an ideal choice for upgrading the appearance of older buildings.
Moreover, stucco foam molding can be used in commercial and residential construction.
In commercial buildings, it can be used to create unique facades and signage.
In residential homes, it can be used to add decorative touches to interiors and exteriors.
Preparation before installation
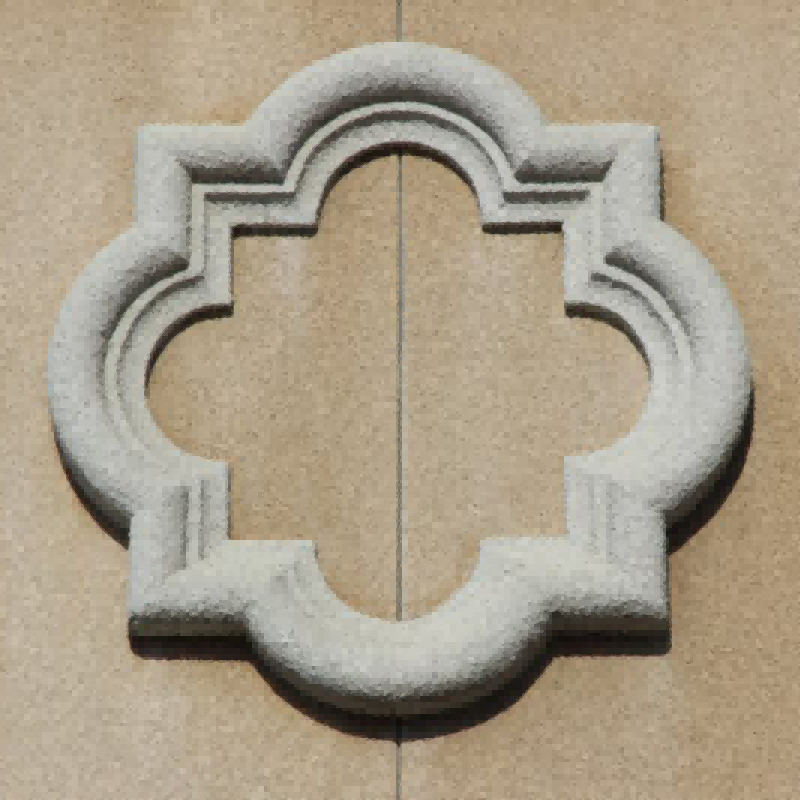
1.Preparation of materials and tools
Installing Stucco Foam Molding requires the preparation of a series of materials and tools.
In terms of materials, a specific foaming agent is one of the keys.
Common foaming agents include inorganic foaming agents such as sodium bicarbonate and ammonium carbonate, and organic foaming agents such as azodicarbonamide and azobisisobutyronitrile.
These foaming agents can release gas when heated to foam the plastic.
In addition, it is necessary to prepare suitable plastic raw materials, generally based on thermoplastic or thermosetting resins.
In terms of tools, injection molding machines are indispensable. Injection molding machines are used to melt plastic and inject it into molds to form products.
Different models of injection molding machines may be suitable for installation projects of different sizes.
At the same time, it is also necessary to prepare molds, which are tools used to make the shape of products, usually consisting of upper molds and lower molds.
The cooling system is also important, which can quickly cool and harden the plastic so that the product can be taken out as soon as possible.
The heating equipment is used to preheat the plastic so that it reaches a rheological state for easy injection into the mold.
The pressure control system can control the pressure during the injection molding process to ensure product quality.
Air compressors provide compressed air to operate injection molding machines and other auxiliary equipment.
Computer control systems can accurately control the operation of injection molding machines, improve production efficiency and product quality.
Cleaning equipment is used to clean molds and equipment to ensure product quality during the next production.
2.Site cleaning and measurement
Before installing Stucco Foam Molding, site cleaning and measurement are essential.
Cleaning the site can ensure the smooth progress of the installation process and avoid the impact of debris on the installation quality.
First, remove the remaining materials on the site, such as molding sand, rust, and chips.
For non-processed surfaces, chisels and wire brushes can be used to remove molding sand and iron slag; for rust and paint on the processed surface, use scrapers, lead knives, and emery cloth to remove.
After cleaning, clean it with a brush, leather bellows or compressed air.
Accurate site measurement is the key to successful installation.
First, determine the scope and purpose of the measurement, such as drawing a topographic map, building a three-dimensional model, etc.
Prepare measurement tools, such as total stations, laser rangefinders, GPS, electronic levels, etc., and confirm their accuracy and precision.
Select at least two benchmark points and record their coordinates as the starting point for site measurement.
Use surveying tools to conduct field measurements and obtain the required measurement data.
According to the purpose and requirements of the measurement, select the measurement data accuracy and remote sensing data for use.
Process the measurement data, perform data quality inspection, noise reduction, interpolation and other operations, and establish a digital elevation model or three-dimensional map.
Finally, output the processed data to the required format, such as digital elevation model (DEM), three-dimensional map, etc., and compile a report.
The obtained data, analysis and processing results are used to compile a report on site characteristics, advantages and disadvantages, and construction or planning implementation plans.
Within the scope of the site leveling on the topographic map, draw a grid in proportion and find the elevation of the four corner points of each square on the topographic map.
Subtract the specified site leveling elevation from the average of the elevations of the four corner points and multiply it by the area of the square to obtain the engineering volume of the square.
Positive values are cut and negative values are filled. Add the positive values of all squares to get the total cut volume, and add the negative values to get the total fill volume.
Detailed explanation of installation method
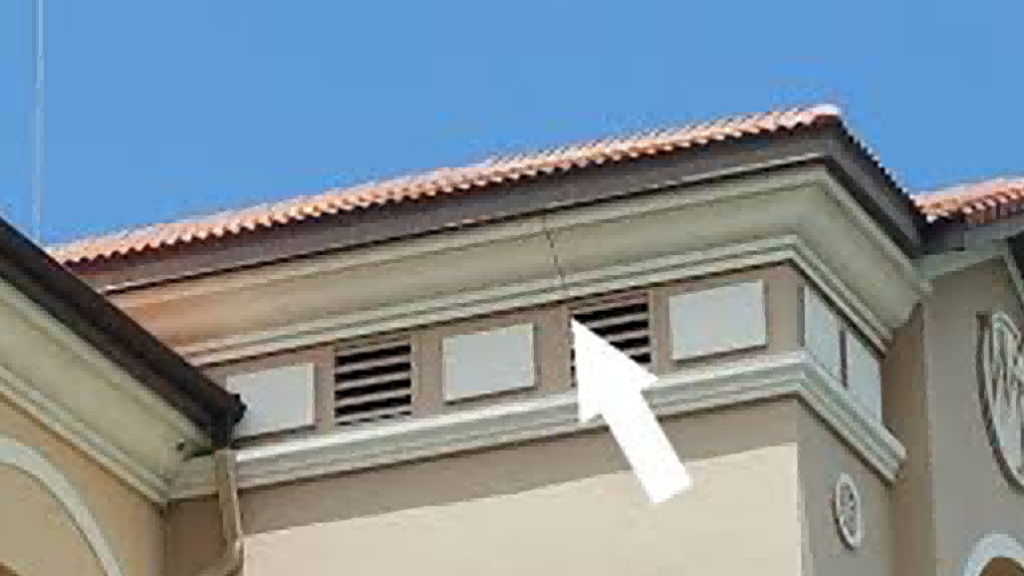
Physical foaming installation
1.Inert gas dissolution and decompression foaming method
The specific steps of this physical foaming method are as follows:
First, dissolve the inert gas in the plastic melt or paste under pressure.
This requires the use of specific equipment to control the pressure to ensure that the inert gas can be fully dissolved.
During the dissolution process, attention should be paid to controlling the stability of temperature and pressure to ensure the dissolution effect of the gas.
Then, the gas is released through decompression, thereby forming pores in the plastic and foaming.
During the decompression process, the speed should be moderate to avoid uneven foaming caused by too fast or too slow.
In terms of precautions, it is necessary to select suitable inert gases, such as nitrogen, carbon dioxide, etc., to ensure that they are non-toxic, odorless, non-corrosive, non-combustible, and have good thermal stability.
At the same time, the sealing of the equipment should be ensured to prevent gas leakage.
In addition, operators need to undergo professional training and be familiar with the operation and safety specifications of the equipment.
2.Low-boiling-point liquid evaporation and foaming method
The operation process is: first dissolve the low-boiling-point liquid into the polymer melt, and then evaporate the low-boiling-point liquid by heating to make it vaporize and foam.
In this process, the heating temperature must be accurately controlled to ensure that the low-boiling-point liquid can evaporate and vaporize at a suitable temperature without adversely affecting the performance of the plastic.
The key point is to select a suitable low-boiling-point liquid, which requires good solubility in the plastic, moderate evaporation temperature, and good foaming effect of the gas produced after vaporization on the plastic.
At the same time, pay attention to controlling the heating speed and time to avoid excessive heating that causes plastic decomposition or performance degradation.
3.Hollow ball addition foaming method
The installation process is to add hollow balls to the plastic to form a foam.
First, choose hollow balls of suitable size and material to ensure their compatibility with the plastic.
Then, the hollow balls are evenly mixed into the plastic, which can be achieved by stirring or other methods.
The advantage of this method is that the operation is relatively simple and does not require complex equipment and processes.
Moreover, the hollow balls can be customized as needed to meet different foaming requirements. In addition, the foaming method of adding hollow balls can control the degree of foaming, so that the product has better strength and stability.
Installation by chemical foaming method
1.Heating chemical foaming agent to decompose gas foaming
The principle is to heat the chemical foaming agent added to the plastic to decompose it and release gas to foam.
In actual operation, the key points include selecting suitable chemical foaming agents, such as sodium bicarbonate, ammonium carbonate, azodicarbonamide, etc.
According to the type and performance requirements of the plastic, determine the amount of foaming agent and the heating temperature.
During the heating process, ensure that the temperature is evenly distributed so that the foaming agent can be fully decomposed.
At the same time, pay attention to controlling the heating time to avoid excessive heating that causes the foaming agent to decompose too quickly and produce adverse effects.
2.Plastic component chemical reaction releases gas foaming
The installation process is to mix different plastic components together so that they react chemically under certain conditions to release gas and foam.
Technical requirements include precise control of the proportion of each plastic component and reaction conditions.
For example, factors such as temperature, pressure, and catalysts will affect the speed and degree of chemical reactions.
During the mixing process, ensure that all components are fully mixed and uniform to ensure the smooth progress of the chemical reaction.
At the same time, the reaction process should be monitored and controlled, and the reaction conditions should be adjusted in time to ensure that the foaming effect meets the requirements.
Structural foaming molding installation
1.Low-pressure foaming method
The difference between low-pressure foaming injection molding and ordinary injection molding is that the mold cavity pressure is lower, about 2-7Mpa, while ordinary injection molding is between 30-60Mpa.
The specific operation of the under-injection method is to inject a certain amount (not filling the mold cavity) of plastic melt (containing foaming agent) into the mold cavity, and the gas decomposed by the foaming agent causes the plastic to expand and fill the mold cavity.
During the operation, pay attention to selecting suitable foaming agents and plastic raw materials to ensure good foaming effects.
At the same time, control the injection speed and pressure to avoid rough surface of the product.
2.High-pressure foaming method
The mold cavity pressure of the high-pressure foaming method is between 7-15Mpa, and the full injection method is adopted, that is, the injection volume at one time is exactly equal to the volume of the mold cavity.
The principle of the cavity expansion method is that after the molten mixture of plastic and foaming agent is injected into the cavity, it is delayed for a period of time.
Then the movable platen of the clamping mechanism moves back a short distance, so that the movable mold and the fixed mold of the mold are slightly separated, the cavity is expanded, and the plastic in the cavity begins to foam and expand.
In actual operation, attention should be paid to controlling the speed and amplitude of cavity expansion to ensure uniform foaming.
At the same time, it is necessary to select suitable foaming agents and plastic raw materials to meet the requirements of high-pressure foaming.
3.Two-component foaming method
The characteristic of the two-component foaming method is that two different components are mixed together for foaming.
One of the components is usually a plastic containing a foaming agent, and the other component can be a catalyst, stabilizer or other additive.
The installation points include precise control of the ratio and mixing time of the two components to ensure good foaming effect.
At the same time, attention should be paid to selecting suitable equipment and processes to meet the requirements of two-component foaming.
Post-installation treatment and maintenance
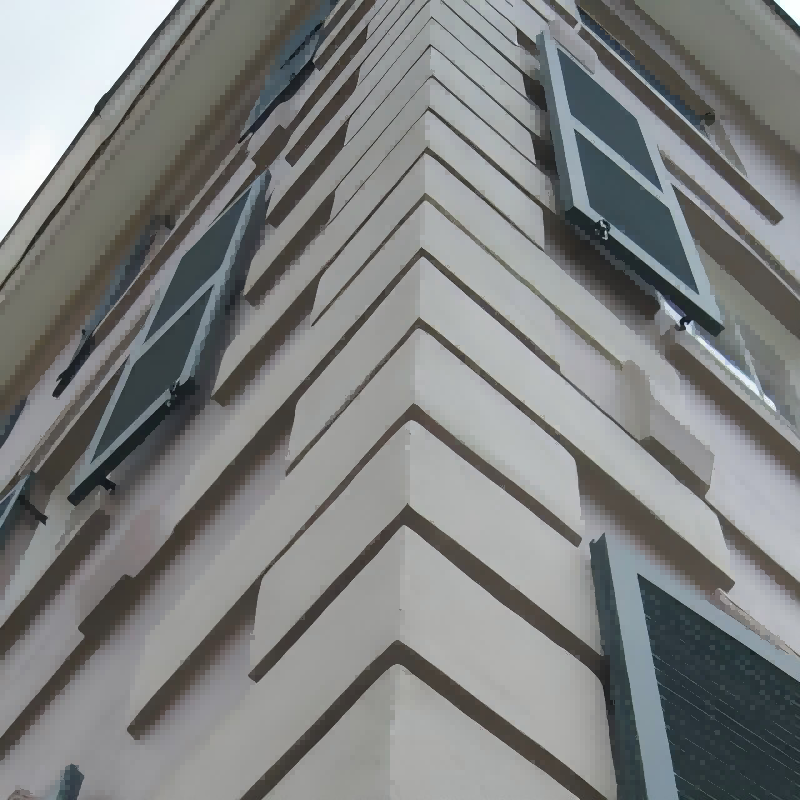
Surface treatment method
Cleaning: After installation, first use warm water (temperature 40-60℃) to clean Stucco Foam Molding to remove dust and impurities on the surface.
You can use a soft cloth or sponge to wipe it, and avoid using rough materials to avoid scratching the surface.
Degreasing: Add a degreaser (such as one or more of alkaline water, water-based detergent and trichloroethylene degreaser) to warm water, stir well and put the product in it for degreasing and oil removal.
After degreasing, rinse with deionized water 2-3 times to ensure that there is no residual degreaser on the surface.
Drying: Put the cleaned and degreased product into the oven for drying, the drying temperature is 80-100℃, and the drying time is 1-2h.
Daily maintenance method
Avoid collision: In daily use, avoid collision and scratching of Stucco Foam Molding.
Protective devices such as railings, protective covers, etc. can be set around the product to prevent accidental collisions.
Regular inspection: Regularly check the surface of the product for damage, deformation or discoloration.
If any problems are found, they should be dealt with in time to avoid further expansion of the problem.
Waterproof and moisture-proof: Since Stucco Foam Molding has a certain degree of hygroscopicity, it is necessary to pay attention to waterproofing and moisture-proofing.
In a humid environment, moisture-proof agents or ventilation equipment can be used to keep the product dry.
Sun protection: Long-term exposure to sunlight will cause the color of the product to fade or fade, so pay attention to sun protection.
You can use awnings, curtains, etc. to block the sun, or apply sunscreen paint on the surface of the product.
Measures to extend the service life
Regular maintenance: Regularly maintain Stucco Foam Molding, such as cleaning, degreasing, drying and other surface treatments, as well as checking and repairing damaged parts.
A reasonable maintenance plan can be formulated according to the use of the product and environmental conditions.
Use appropriate cleaning and maintenance agents: Choose appropriate cleaning and maintenance agents, and avoid using chemicals that are harmful to the product.
You can consult professionals or refer to the product manual to choose suitable cleaning and maintenance agents.
Avoid excessive load: During use, avoid excessive load on the product to avoid deformation or damage.
The use method and load can be reasonably arranged according to the product’s load-bearing capacity and usage requirements.
Proper storage: If the product needs to be stored, a dry, ventilated, light-proof place should be selected, and contact with chemicals should be avoided.
Plastic bags, cartons and other packaging materials can be used for packaging to protect the product.
Through the above surface treatment and daily maintenance methods, the service life of Stucco Foam Molding can be extended to keep it in good appearance and performance.
Experience Sharing
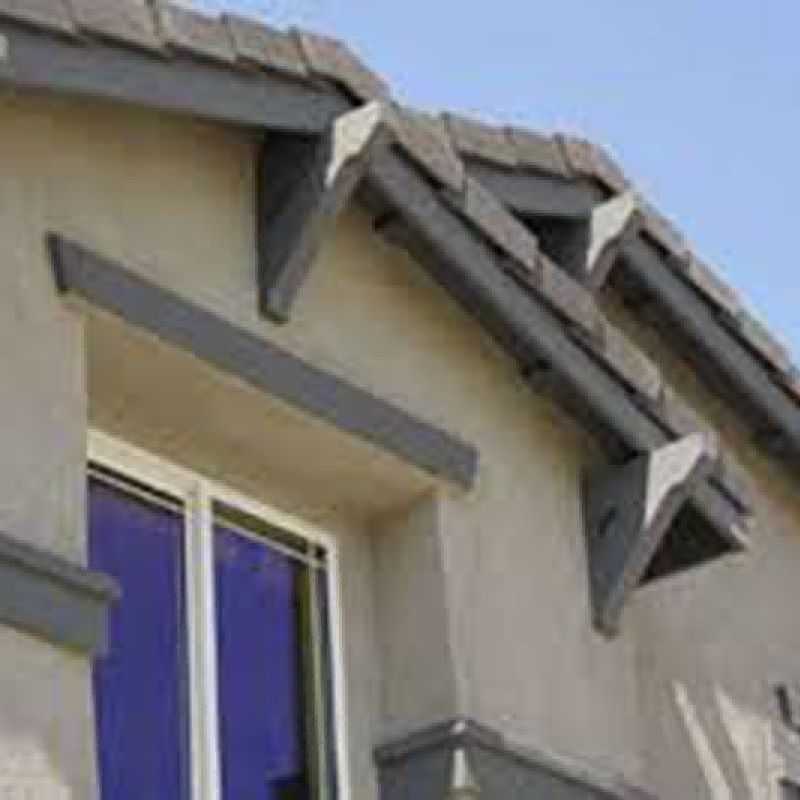
The Importance of Material Selection
When selecting foaming agents and plastic raw materials, the needs of the project and environmental factors should be fully considered.
Different foaming agents and plastic raw materials have different performance characteristics, such as foaming effect, strength, durability, etc.
When selecting, it is necessary to make a comprehensive consideration based on the actual situation and select the most suitable material.
For example, in some humid environments, materials with good moisture resistance should be selected; in occasions where higher strength is required, plastic raw materials and foaming agents with higher strength should be selected.
Preparation of tools and equipment
Installing Stucco Foam Molding requires a series of tools and equipment, such as injection molding machines, molds, heating equipment, pressure control systems, etc.
Before installation, ensure that these tools and equipment perform well and can meet the needs of the project.
At the same time, tools and equipment should be regularly maintained and maintained to ensure that they can operate normally during the installation process.
If tools and equipment fail, it may affect the installation progress and quality.
Accuracy of site cleaning and measurement
Site cleaning and measurement are important links in the installation process, which directly affect the quality and effect of the installation.
When cleaning the site, make sure to thoroughly remove debris and residues to provide a clean and flat surface for installation.
When measuring, use accurate measuring tools to ensure the accuracy of the measurement data.
If the measurement data is inaccurate, it may cause deviations in the installation position and size of the decorative elements, affecting the aesthetics and use effect.
Selection of installation method
Choose a suitable installation method according to the specific situation of the project.
Physical foaming, chemical foaming and structural foaming molding each have their own advantages and disadvantages, and should be selected according to actual needs.
For example, in some occasions where the foaming effect is required to be high, the chemical foaming method can be selected; in some occasions where there are requirements for cost and operation difficulty, physical foaming or structural foaming molding can be selected.
Skills and experience of operators
Installing Stucco Foam Molding requires operators to have certain skills and experience.
Before installation, operators should be trained to ensure that they are familiar with the installation process and operation methods.
At the same time, operators should be encouraged to continuously summarize their experience during the installation process to improve the quality and efficiency of installation.
If the operator is not skilled or lacks experience, problems may occur during the installation process, affecting the progress and quality of the project.
Common Problems
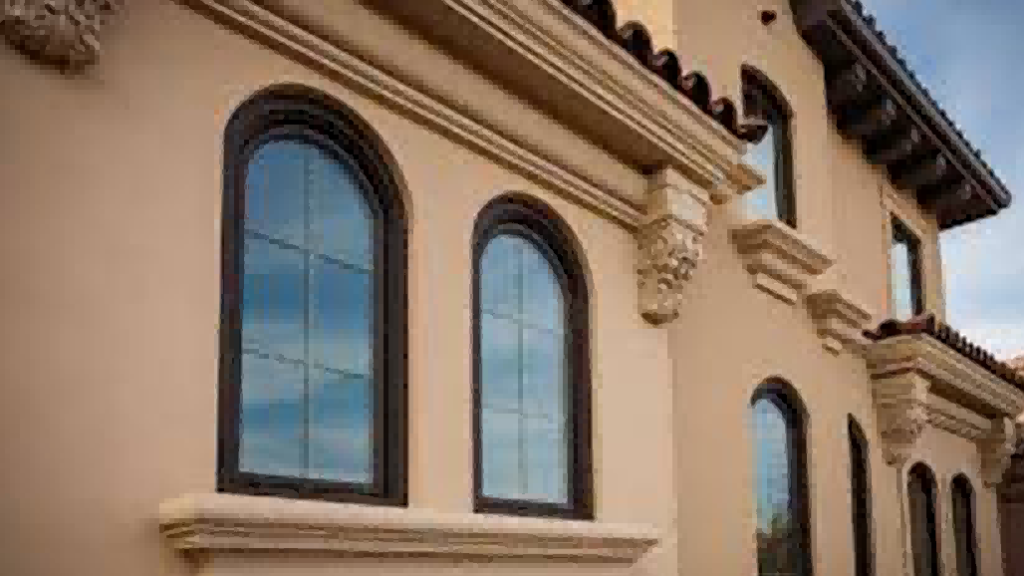
Uneven foaming is one of the common problems during installation.
Possible reasons include uneven amount of foaming agent added, improper temperature and pressure control, etc.
Check the foaming agent addition equipment to ensure that the foaming agent can be evenly added to the plastic.
At the same time, strictly control the temperature and pressure to ensure that they are within the appropriate range.
If uneven foaming is found, it can be solved by adjusting the amount of foaming agent added, temperature and pressure and other parameters.
Surface roughness may be caused by reasons such as too fast injection speed and rough mold surface.
Reduce the injection speed to ensure that the plastic can fully fill the mold.
At the same time, the mold should be regularly maintained and maintained to ensure that the mold surface is smooth.
If the surface roughness is more serious, consider grinding and polishing the product.
Insufficient strength may be caused by improper selection of plastic raw materials, excessive amount of foaming agent, etc.
Select plastic raw materials with higher strength and adjust the amount of foaming agent according to actual conditions.
At the same time, consider adding reinforcing materials such as glass fiber to the plastic to improve the strength of the product.
Dimensional deviation may be caused by inaccurate measurement, mold making errors, etc.
During the measurement and mold making process, the accuracy must be strictly controlled to ensure that the size is accurate.
If the size deviation is found, it can be solved by adjusting the mold size or remaking the mold.