Expandable Polypropylene (EPP) is a specialized foam plastic material that has revolutionized impact protection, thermal insulation, and lightweight design across multiple industries.
Unlike conventional polypropylene, EPP consists of small beads containing a blowing agent that can be expanded and molded into complex shapes with exceptional energy-absorbing properties.
This unique material combines the chemical resistance and durability of polypropylene with the lightweight cushioning characteristics of foam, making it ideal for automotive components, protective packaging, and consumer products.
What Is Expandable Polypropylene?
Fundamental Composition
Expandable Polypropylene consists of:
- Polypropylene resin base: Provides chemical resistance and durability
- Physical blowing agents: Typically CO₂ or N₂ gas that enables expansion
- Additive packages: May include flame retardants, colorants, or UV stabilizers
Key Characteristics
EPP stands out for its unique combination of properties:
- Closed-cell foam structure: Provides excellent buoyancy and moisture resistance
- Outstanding impact absorption: Can withstand repeated impacts without permanent deformation
- Temperature resistance: Performs consistently from -40°C to +130°C
- Chemical inertness: Resists most solvents, acids, and alkalis
- Lightweight: Typical densities range from 20-200 kg/m³
- Hygienic: Non-toxic and food-contact approved grades available
Manufacturing Process
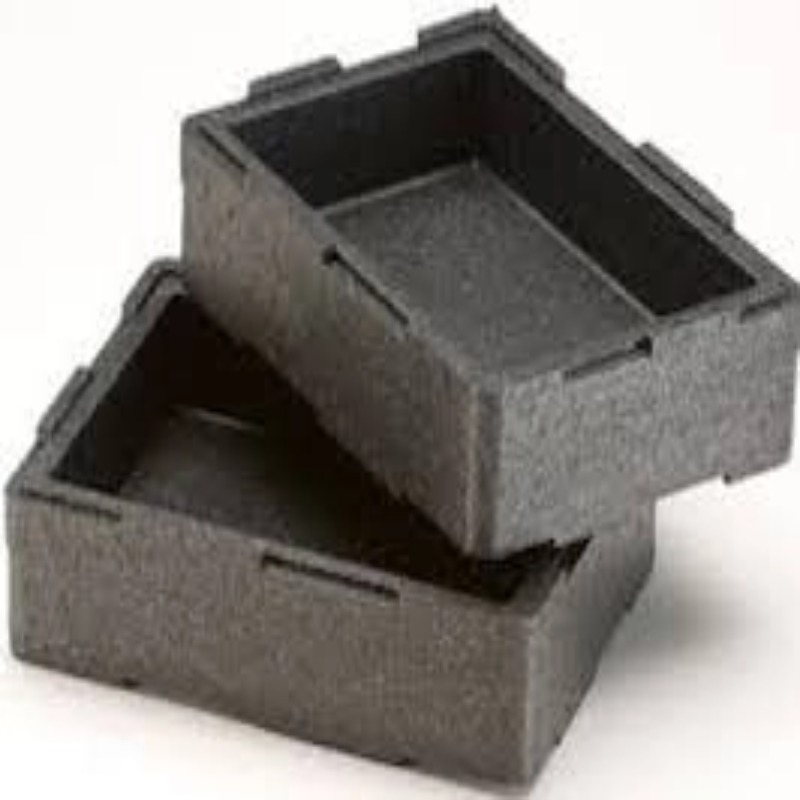
Raw Material Production
- Polymerization: Creation of polypropylene resin with controlled molecular weight
- Impregnation: Incorporation of physical blowing agents under pressure
- Pelletizing: Formation of small beads (0.5-3mm diameter) containing blowing agent
Expansion Process
The transformation from raw beads to finished foam involves:
Pre-expansion:
- Beads heated with steam (100-150°C)
- Blowing agent activates, expanding beads 20-50 times original size
- Density reduced to 20-200 g/L
Conditioning:
- Expanded beads stabilize for 6-24 hours
- Internal pressure equalizes
- Moisture content adjusts
Molding:
- Beads placed in steam-heated mold
- Further expansion fills mold cavity
- Beads fuse together at contact points
- Cooling solidifies the final shape
Material Properties and Performance
Physical Properties Table
Property | Typical Value | Importance |
---|---|---|
Density | 20-200 kg/m³ | Affects weight and strength |
Compressive Strength | 0.1-2.5 MPa | Determines load capacity |
Thermal Conductivity | 0.030-0.040 W/mK | Insulation performance |
Water Absorption | <1% by volume | Moisture resistance |
Operating Temperature | -40°C to +130°C | Environmental stability |
Rebound Elasticity | 60-80% | Impact absorption |
Comparison with Other Foams
Feature | EPP | EPS | PU Foam |
---|---|---|---|
Impact Resistance | Excellent | Good | Fair |
Temperature Range | Very Wide | Moderate | Varies |
Chemical Resistance | Excellent | Good | Fair |
Recyclability | High | Limited | Difficult |
Cost | Higher | Lower | Medium |
Advantages of Expandable Polypropylene
Performance Benefits
Superior Energy Absorption:
- Ideal for impact protection applications
- Maintains protective qualities after multiple impacts
- Excellent vibration damping characteristics
Thermal Management:
- Effective insulation for temperature-sensitive products
- Stable performance in extreme environments
- Low thermal conductivity
Design Flexibility:
- Can be molded into complex geometries
- Variable wall thickness in single parts
- Good surface detail reproduction
Economic and Environmental Advantages
Lightweighting Potential:
- Reduces material usage
- Lowers transportation costs
- Improves fuel efficiency in vehicles
Sustainability Features:
- Fully recyclable material
- Clean production process
- Long service life reduces waste
Cost Efficiency:
- Durable parts require less replacement
- Minimal production waste
- Reduced damage in shipping
Applications of Expandable Polypropylene
Automotive Industry
EPP has become essential for modern vehicles:
Safety Components:
- Bumper cores
- Door impact absorbers
- Knee bolsters
Comfort Features:
- Seat cushioning
- Headrests
- Armrest cores
Electric Vehicle Solutions:
- Battery impact protection
- Thermal management systems
- Lightweight structural components
Packaging Products
Superior protective qualities for:
Consumer Electronics:
- Television and monitor packaging
- Computer component holders
- Audio equipment protection
Industrial Packaging:
- Machine part transport systems
- Heavy equipment cushioning
- Sensitive instrument containers
Food Packaging:
- Insulated shipping containers
- Protective produce packaging
- Reusable cooler systems
Consumer and Industrial Products
Diverse applications include:
Sports Equipment:
- Helmet liners
- Protective padding
- Floatation devices
Furniture Components:
- Lightweight cores
- Cushioning elements
- Sound absorption panels
Construction Materials:
- Insulation boards
- Void fillers
- Expansion joint fillers
Processing Technologies
Molding Methods
Steam Chest Molding:
- Most common industrial process
- Uses steam to expand and fuse beads
- Produces complex 3D shapes
Compression Molding:
- Alternative for simpler geometries
- Uses heat and pressure
- Faster cycle times for certain parts
Injection Molding:
- Emerging technology
- Combines EPP with injection molding
- Allows multi-material components
Secondary Processing
Common finishing techniques:
Cutting and Trimming:
- CNC machining
- Hot wire cutting
- Die cutting
Assembly Methods:
- Adhesive bonding
- Mechanical fastening
- Welding techniques
Surface Treatments:
- Painting and coating
- Laminating
- Texture application
Design Considerations for EPP Products
Wall Thickness Guidelines
Optimal design parameters:
- Minimum Thickness: 5mm
- Typical Range: 10-50mm
- Thick Sections: Possible with proper venting
- Uniformity: Less critical than solid plastics
Draft Angles and Demolding
Essential for quality production:
- Standard Draft: 1-2° per side
- Textured Surfaces: Additional 0.5-1°
- Undercuts: Generally avoided or handled with special tooling
Venting Requirements
Critical for proper filling:
- Vent Placement: Along parting lines
- Vent Size: 0.02-0.05mm
- Number: More vents improve bead fusion
Environmental Impact and Sustainability
Recycling and Circular Economy
EPP’s environmental advantages:
Mechanical Recycling:
- Grinding and reprocessing
- Multiple reuse cycles possible
- Minimal property degradation
Chemical Recycling:
- Depolymerization back to monomers
- Energy-intensive but effective
- Emerging technologies improving efficiency
Industrial Take-Back Programs:
- Automotive manufacturer initiatives
- Packaging collection systems
- Closed-loop recycling models
Life Cycle Assessment
Compared to alternative materials:
Production Phase:
- Lower energy than many plastics
- Clean manufacturing processes
Use Phase:
- Lightweight reduces transportation impact
- Durability extends service life
End-of-Life:
- Recyclability superior to many foams
- Non-toxic decomposition products
How Expanded Polypropylene (EPP) is Made
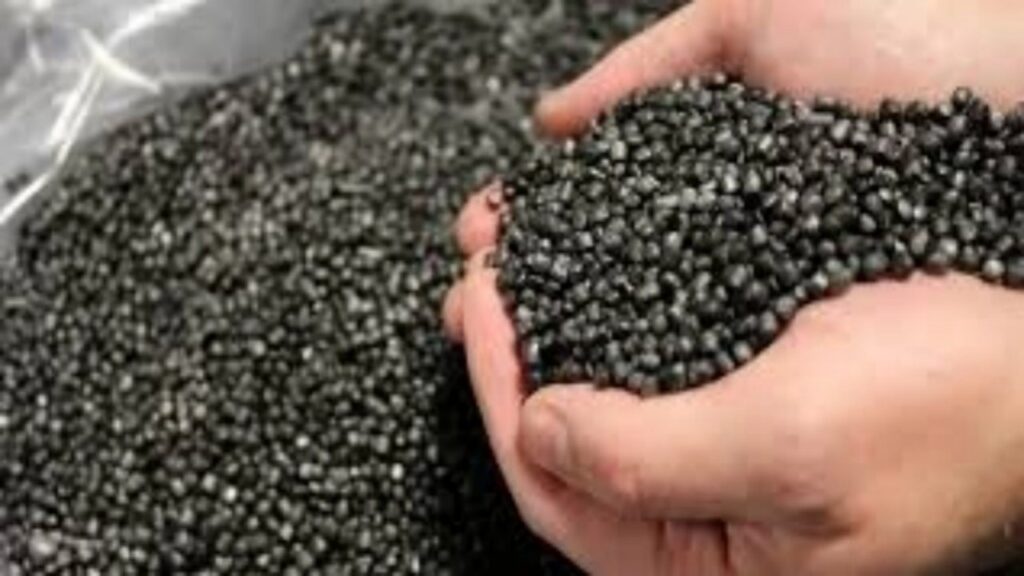
Expanded Polypropylene (EPP) is manufactured through a sophisticated multi-stage process that transforms solid polypropylene beads into lightweight, resilient foam products.
This unique manufacturing method combines polymer science with precise thermal and pressure controls to create a material with exceptional impact absorption, thermal insulation, and durability properties.
The production of EPP involves specialized equipment and carefully controlled conditions to achieve consistent foam quality across various densities and applications.
Raw Material Preparation
Base Polymer Composition
The EPP manufacturing process begins with the creation of specialized polypropylene resin:
Polymer Selection:
- High melt-strength polypropylene (HMS-PP) is typically used
- Custom formulations with specific molecular weights
- May include additives for color, UV resistance, or flame retardancy
Blowing Agent Incorporation:
- Physical blowing agents (usually CO₂ or N₂) impregnated under pressure
- Concentration typically 3-8% by weight
- Uniform distribution throughout the polymer matrix
Bead Formation
The impregnated polymer is processed into small beads:
Extrusion and Pelletizing:
- Polymer extruded through die plates
- Cut into small cylindrical pellets (0.5-3mm diameter)
- Carefully controlled size distribution
Quality Control:
- Bead size consistency checks
- Blowing agent content verification
- Moisture content analysis
Pre-Expansion Process
Initial Expansion Phase
The first critical transformation of the material:
Pre-Expansion Equipment:
- Pressurized vessels with steam injection
- Temperature-controlled environments
- Continuous or batch systems available
Expansion Mechanism:
- Beads heated to 100-150°C
- Blowing agent activates, creating internal pressure
- Beads expand 20-50 times original volume
- Density reduced to target level (typically 20-200 g/L)
Conditioning Stage
Essential stabilization period:
Storage Conditions:
- Controlled temperature environment
- Regulated humidity levels
- Typically 6-24 hours duration
Physical Changes:
- Internal pressure equalization
- Moisture content stabilization
- Bead surface conditioning
Molding Process
Mold Preparation
Setting up for final shaping:
Mold Design Features:
- Aluminum or steel construction
- Precision steam channels
- Venting systems for air escape
- Cooling water passages
Pre-Mold Steps:
- Heating to 110-150°C
- Application of release agents (if needed)
- Verification of clean surfaces
Bead Loading and Expansion
Transforming beads into finished products:
Filling Methods:
- Gravity filling for simple parts
- Pressure filling for complex geometries
- Specialized systems for large components
Steam Application:
- Steam injected through mold vents (1-4 bar pressure)
- Even distribution critical for uniform expansion
- Typical steam time: 10-60 seconds depending on part size
Fusion Process:
- Beads expand to fill mold completely
- Surface fusion creates cohesive structure
- Internal bead boundaries remain for energy absorption
Cooling and Demolding
Finalizing the product:
Cooling Phase:
- Water circulated through mold channels
- Controlled cooling rate prevents warping
- Typical cooling time: 1-3 minutes
Demolding:
- Mold opens automatically
- Ejector systems remove finished part
- Manual removal for delicate components
Post-Molding Processing:
- Trimming of flash or excess material
- Drying if necessary
- Quality inspection
Quality Control Measures
Density Verification
Ensuring consistent material properties:
Gravimetric Analysis:
- Weight/volume calculations
- Multiple sample points
Ultrasonic Testing:
- Non-destructive density measurement
- Identifies density variations
Structural Integrity Checks
Verifying proper bead fusion:
Visual Inspection:
- Surface quality assessment
- Fusion point examination
Mechanical Testing:
- Compression testing
- Cut-section analysis
- Rebound elasticity measurements
Dimensional Accuracy
Precision verification:
Coordinate Measurement:
- CMM machines for critical dimensions
- Laser scanning for complex geometries
Fixture Testing:
- Functional fit checks
- Assembly verification
Specialized Manufacturing Variations
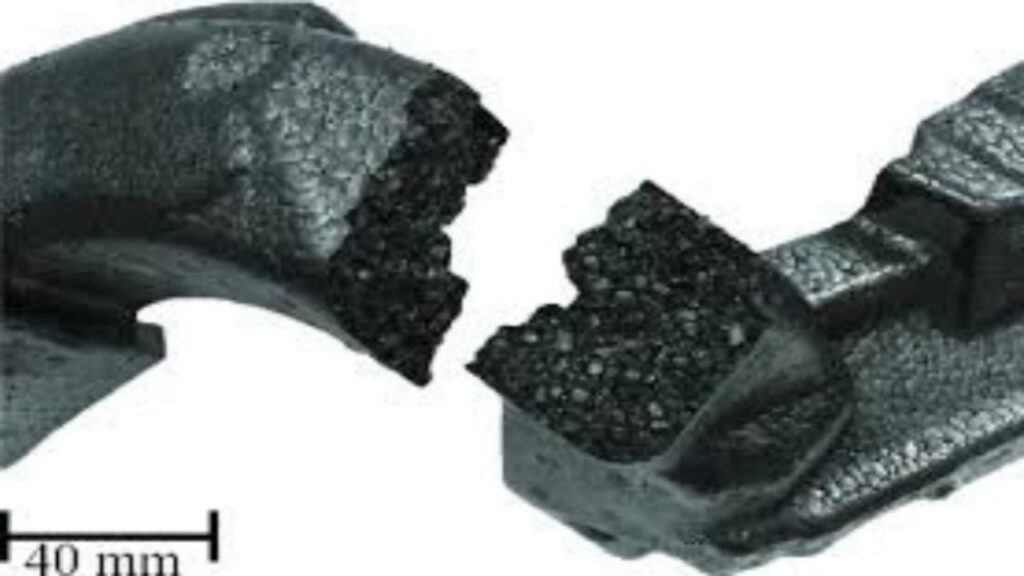
Multi-Density Parts
Advanced molding techniques:
Differential Density:
- Varying densities within single part
- Achieved through controlled filling
- Used for customized energy absorption
Co-Molding:
- Combining EPP with other materials
- Insert molding applications
- Hybrid component production
Surface Finishing Options
Enhanced product aesthetics:
Texture Molding:
- Mold surface patterning
- Replicates wood grain, leather, etc.
In-Mold Lamination:
- Fabric or film application during molding
- Bonded surface layers
Post-Mold Treatments:
- Painting and coating
- Hot stamping
- Laser etching
Environmental Considerations
Sustainable Production Practices
Eco-friendly manufacturing:
Energy Efficiency:
- Heat recovery systems
- Optimized steam usage
- Efficient cooling processes
Waste Reduction:
- Minimal production scrap
- Closed-loop water systems
- Reuse of off-spec material
Emissions Control:
- Clean steam generation
- VOC capture systems
- Responsible blowing agent management
Recycling and End-of-Life
Circular economy integration:
Mechanical Recycling:
- Grinding and reprocessing
- Multiple life cycles possible
- Minimal property degradation
Chemical Recycling:
- Advanced depolymerization
- Monomer recovery
- Emerging technologies
Industrial Programs:
- Automotive take-back initiatives
- Packaging collection systems
- Manufacturer responsibility
Conclusion: Why Choose Expandable Polypropylene?
Expandable Polypropylene represents a unique class of engineering foam that combines exceptional physical properties with environmental responsibility.
From the initial impregnation of polypropylene beads with blowing agents to the final molded products, each step in the EPP manufacturing process requires careful control and specialized expertise.
Its outstanding energy absorption characteristics, combined with chemical resistance and temperature stability, make it the material of choice for demanding applications where performance and durability are paramount.
As industries increasingly prioritize lightweight design and sustainable materials, EPP’s advantages continue to grow in importance.
The material’s recyclability and clean production process align with circular economy principles, while its technical performance satisfies even the most rigorous application requirements.